3.2 制板工艺要求
PCB设计的目的是为了实现电气性能设计要求,设计的图形文件必须可生产、可装配,并具有可靠性、可测试性、方便维修等特点。因而PCB设计需要满足一定的生产工艺要求。
常规的PCB加工说明主要包含PCB板厚、叠层设计、阻抗设计、表面处理工艺、阻焊设计、丝印设计、翘曲度、检验标准等要求。
1. PCB板厚
板厚包含了各种材质和铜箔的厚度,指的是成品厚度。PCB板厚的选取应该依据结构、PCB尺寸大小和所安装元器件的重量来选取。一般贴装机允许的板厚为0.5~3mm,也有的板厂能力能达到4.5mm。
常规PCB的设计板厚一般是1mm、1.6mm、1.8mm、2mm、2.2mm等。单板多采用层压的方式生产,板厚还要满足一定的生产公差要求,如下所示。
- 板厚≤1mm:±0.1mm;
- 板厚>1mm:±10%;
- 其他特殊公差要求。
2. 阻抗、叠层设计
阻抗和叠层主要依据板厚、层数、阻抗值要求、载流大小、信号要求等因素确定,叠层设计必须以满足信号的基本阻抗要求为前提,兼顾制板工艺要求。图3-15所示为一个典型的4层叠层结构。

图3-15 4层叠层结构
阻抗设计的常规值要求是单端布线50Ω、差分线100Ω,特殊走线要求85Ω和90Ω等,一般的设计误差为10%。阻抗设计需要保证其连续性,差分布线建议采用紧耦合,差分间距小于等于2倍线宽。
叠层设计的一般要求如下:
- 需要具有对称性,避免PCB翘曲。
- 元件下面最好为地平面,保证信号靠近参考层,避免跨分割布线。
- 相邻层间要拉大距离,如果信号层夹在电源层和地层之间,则信号尽量靠近地层。
- 设计叠层时,控制线宽最好调整在4~6mil范围,避免极限设计。
- 层压半固化片≤3张,并且次外层至少有一张7628、2116或3313。
- 半固化片使用顺序为7628→2116→3313→1080→106。
3. 阻焊设计
阻焊层的主要目的是防止氧化、防止焊接时桥连现象的产生,并起绝缘的作用,阻焊膜的设计主要是确定开窗方式和焊盘余隙。
阻焊设计主要包含焊盘阻焊、过孔阻焊设计,其一般设计原则如下:
- 阻焊开窗一般比焊盘大5mil以上(单边2.5mil)。
- 相邻焊点间若要保留阻焊桥,最小阻焊桥宽度为4mil。
- 阻焊开窗边缘到附近的导体应保留5mil以上的间隔。
- 当SMT元器件焊盘间隙≥7mil时,采用单焊盘式窗口设计;间隙<7mil时,采用开整窗处理方式。
- 散热用途的铺铜可以阻焊开窗。
- 金手指的阻焊开窗应开整窗,上面和金手指的上端平齐,下端要超出金手指下面的板边,金手指顶部开窗与附近焊盘距离需要≥20mil。
- 一般信号过孔为塞孔不开窗,测试孔需要按常规比焊盘大5mil开窗处理。
- BGA过孔一般进行塞孔处理,如果需要做测试孔,可在元件面开小窗,背面测试焊盘32mil,阻焊开窗37mil。
- 注意阻焊油墨的厚度和阻焊桥的宽度,基铜厚度≤1oz时,至少4mil间隙;基铜厚度为2~4oz时,可按6mil间隙处理。
4. 丝印设计
PCB丝印指的是标识符号,包括元器件丝印、板名版本号、条码丝印、安装孔丝印、防静电标识、无铅标识等其他要求丝印。如图3-16所示为防静电丝印标识。
丝印字符油墨颜色一般为白色、黄色、黑色。对全板喷锡板,建议采用黄色永久性绝缘油墨,以便看清字符;在无阻焊情况下,不建议丝印字符。丝印字符分为字符阳字和字符阴字两种,类似正片和负片。阳字为实体字符,阴字指镂空字符,如图3-17所示。
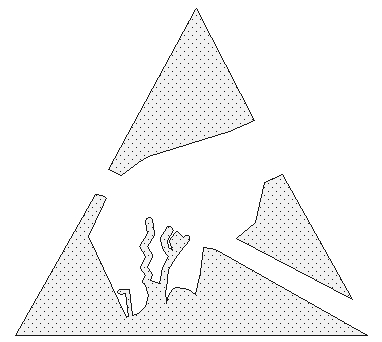
图3-16 防静电丝印标识
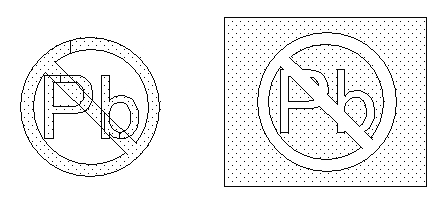
图3-17 丝印字符
如果设计为字符阴字,则线宽≥8mil,最小字符油墨宽度≥5mil;如果设计为字符阳字,则推荐字高与字符线宽之比≥6:1。常规设计要求如表3-5所示。
表3-5 丝印线宽与高度

5. 翘曲度
翘曲是弓曲和扭曲的统称,弓曲是指板以圆柱形或球面曲线形状偏离平面,即如果板是长方形的,则它只有四个角在同一平面上,其余则偏离平面不同程度地弯曲;扭曲是指平行于长方形对角线的板材变形,即一个角与其他三个角不在同一平面上,如图3-18所示。
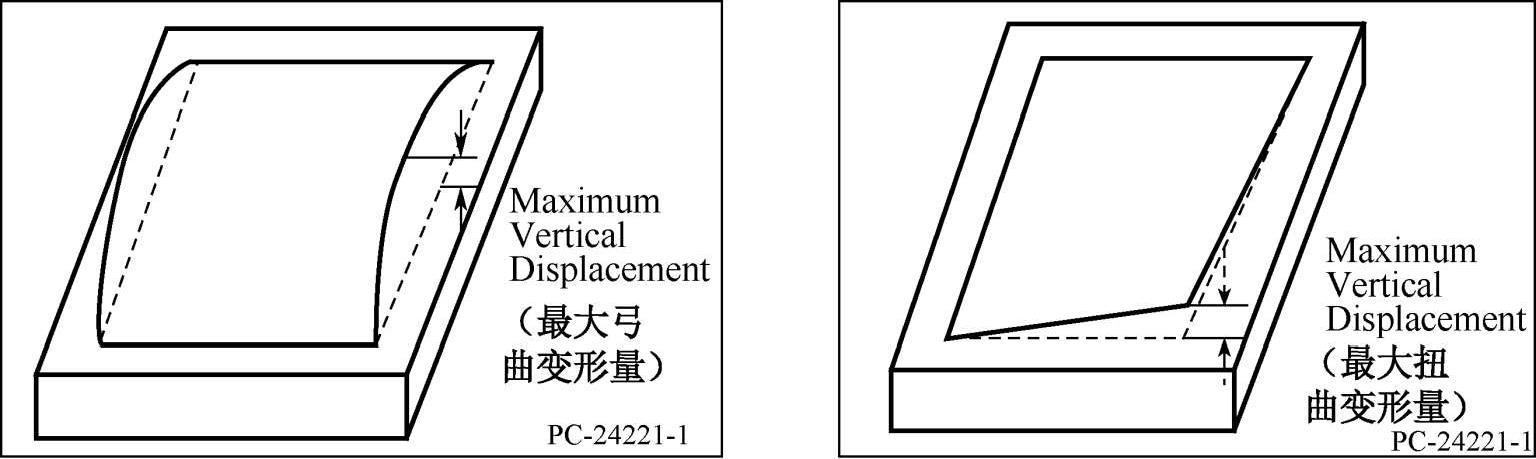
图3-18 平面翘曲示意图
IPC标准中对PCB印制板翘曲度有明确的要求,具体如表3-6所示。
表3-6 翘曲度要求

6. 检验标准
印制板依据产品特性、使用环境等,通常有如下三种PCB刚性板检验标准,即IPCII级、IPCIII级和GJB 362A—2009。
常规PCB设计一般分为民品和军品两大类,分别对应相应的IPC标准及国军标标准。
7. 表面处理工艺
表面处理工艺也是制板工艺要求的一部分,表面处理最基本的目的是保证良好的可焊性或电性能。由于自然界的铜在空气中倾向于以氧化物的形式存在,不大可能长期保持为原铜,因此需要对铜进行处理。随着人们对环保要求的不断提高,目前PCB生产过程中涉及环保的问题日益突出,有关铅和镍的话题是最热门的,无铅化和无卤化将在很多方面影响着PCB的发展。
常见的表面处理工艺包括热风整平、有机涂覆、沉金、沉锡和沉银等。
1)热风整平 又名热风焊料整平,它是在PCB表面涂覆熔融锡铅焊料并用加热压缩空气整(吹)平的工艺,使其形成一层既抗铜氧化,又可提供良好的可焊性的涂覆层。热风整平时焊料和铜在结合处形成铜锡金属间化合物。PCB进行热风整平时要浸在熔融的焊料中;风刀在焊料凝固之前吹平液态的焊料;风刀能够将铜面上焊料的弯月状最小化和阻止焊料桥接。热风整平分为垂直式和水平式两种,一般认为水平式较好,主要是水平式热风整平镀层比较均匀,可实现自动化生产。
2)有机涂覆工艺(OSP) OSP是防氧化及可焊性保护剂,用于保证裸铜在存储和组装过程中保持表面的可焊性。不同于其他表面处理工艺,它是在铜和空气间充当阻隔层;OSP工艺简单、成本低廉,这使得它能够在业界广泛使用。在后续的焊接过程中,如果铜面上只有一层有机涂覆层是不行的,必须有很多层,这就是化学槽中通常需要添加铜液的原因。在涂覆第一层之后,涂覆层吸附铜,接着第二层的有机涂覆分子与铜结合,直至二十甚至上百次的有机涂覆分子集结在铜面,这样可以保证进行多次回流焊。试验表明,最新的有机涂覆工艺能够在多次无铅焊接过程中保持良好的性能。
3)全板镀镍金 全板镀镍金是在PCB表面导体先镀上一层镍后再镀上一层金,镀镍主要是为了防止金和铜间的扩散。另外,它也具有其他表面处理工艺所不具备的对环境的忍耐性,这可以长期保护PCB。
现在的电镀镍金有两类:镀软金(纯金,金表面看起来不亮)和镀硬金(表面平滑和硬、耐磨,含有钴等其他元素,金表面看起来较光亮)。软金主要用于芯片封装时打金线,硬金主要用在非焊接处的电性互连。
4)沉金 沉金是在铜面上包裹一层厚厚的、电性良好的镍金合金,这可以长期保护PCB;另外,它也具有其他表面处理工艺所不具备的对环境的忍耐性。镀镍的原因是由于金和铜间会相互扩散,而镍层能够阻止金和铜间的扩散;如果没有镍层,金将会在数小时内扩散到铜中去。沉金的另一个好处是镍的强度,仅仅5μm厚度的镍就可以限制高温下 Z 方向的膨胀。此外,沉金也可以阻止铜的溶解,这将有益于无铅组装。
5)电镀硬金 为了提高产品的耐磨性能、增加插拔次数而电镀硬金。电镀硬金常用于金手指插头和接触性焊盘开关,不能用于常规器件焊接(可焊性不好)。设计板厚范围为0.2~7.0mm。
6)沉锡 由于目前所有的焊料都是以锡为基础的,所以锡层能与任何类型的焊料相匹配。从这一点来看,沉锡工艺极具发展前景。但是以前的PCB经浸锡工艺后出现锡须,在焊接过程中锡须和锡迁徙会带来可靠性问题,因此浸锡工艺的采用受到限制。后来在浸锡溶液中加入了有机添加剂,可使得锡层呈颗粒状结构,克服了以前的问题,而且还具有好的热稳定性和可焊性。
沉锡工艺可以形成平坦的铜锡金属间化合物,这个特性使得沉锡具有和热风整平一样的好的可焊性,而没有热风整平令人头痛的平坦性问题;沉锡也没有沉金金属间的扩散问题——铜锡金属间化合物能够稳固地结合在一起。沉锡板不可存储太久,组装时必须根据沉锡的先后顺序进行。
7)沉银 介于有机涂覆和沉金之间,工艺比较简单、快速;不像沉金那样复杂,也不是给PCB穿上一层厚厚的盔甲,但是它仍然能够提供好的电性能。银是金的“小兄弟”,即使暴露在热、湿和污染的环境中,银仍然能够保持良好的可焊性,但会失去光泽。沉银不具备沉金所具有的好的物理强度,因为银层下面没有镍。另外,沉银有好的储存性,沉银后放几年组装也不会有大的问题。
沉银是置换反应,它几乎是亚微米级的纯银涂覆。有时沉银过程中还包含一些有机物,主要是防止银腐蚀和消除银迁移问题;一般很难测量出来这一薄层有机物,分析表明有机体的重量小于1%。