1.2 动力性和经济性设计理论和方法
汽车性能设计的原则来源于基础物理力学,根据牛顿第二定律,车辆运动时(包括静止状态)的加速度取决于作用在其上所有外力的合力。
车辆沿其行进方向的运动特性取决于该方向上的受力情况。在建立车辆模型进行仿真时,首先要做的就是分析其受力情况。图1-9所示为作用于行驶中车辆上的力。驱动轮的轮胎与路面接触面上的牵引力 F t 驱动车辆向前运动。该作用力由驱动系统的转矩产生,并通过传动系统传递,最终带动驱动轮。车辆运动时还会受到阻碍其运动的作用力 F r 。该阻力通常包括空气阻力、轮胎滚动阻力、传动系统阻力、坡道阻力和加速阻力。
车辆的最大牵引力存在两个限制因素:一是满足轮胎与地面的附着条件下的最大牵引力;二是驱动单元通过传动系统所能提供的最大转矩对应的牵引力。这两个因素中较小的一个决定了车辆的最大牵引力。对于高附路面上行驶的车辆,其性能主要受限于第二个因素。不论是何种车辆构型,其驱动系统都包含了驱动单元、传动系统和储能系统。
本节着重论述车辆驱动的基本原理、车辆动力学方程的建立、动力性和经济性的理论计算、以最大牵引力为目标的驱动单元、传动系统和储能系统的性能设计,同时要考虑高压电系统对于电动汽车性能的限制。
1.2.1 牵引力、阻力与车辆动力学方程
车辆的纵向运动状态,取决于车辆的牵引力 F t (最大牵引力受限于轮胎与地面间的附着力)和阻力 F r 之间的关系,分为以下三种情况:
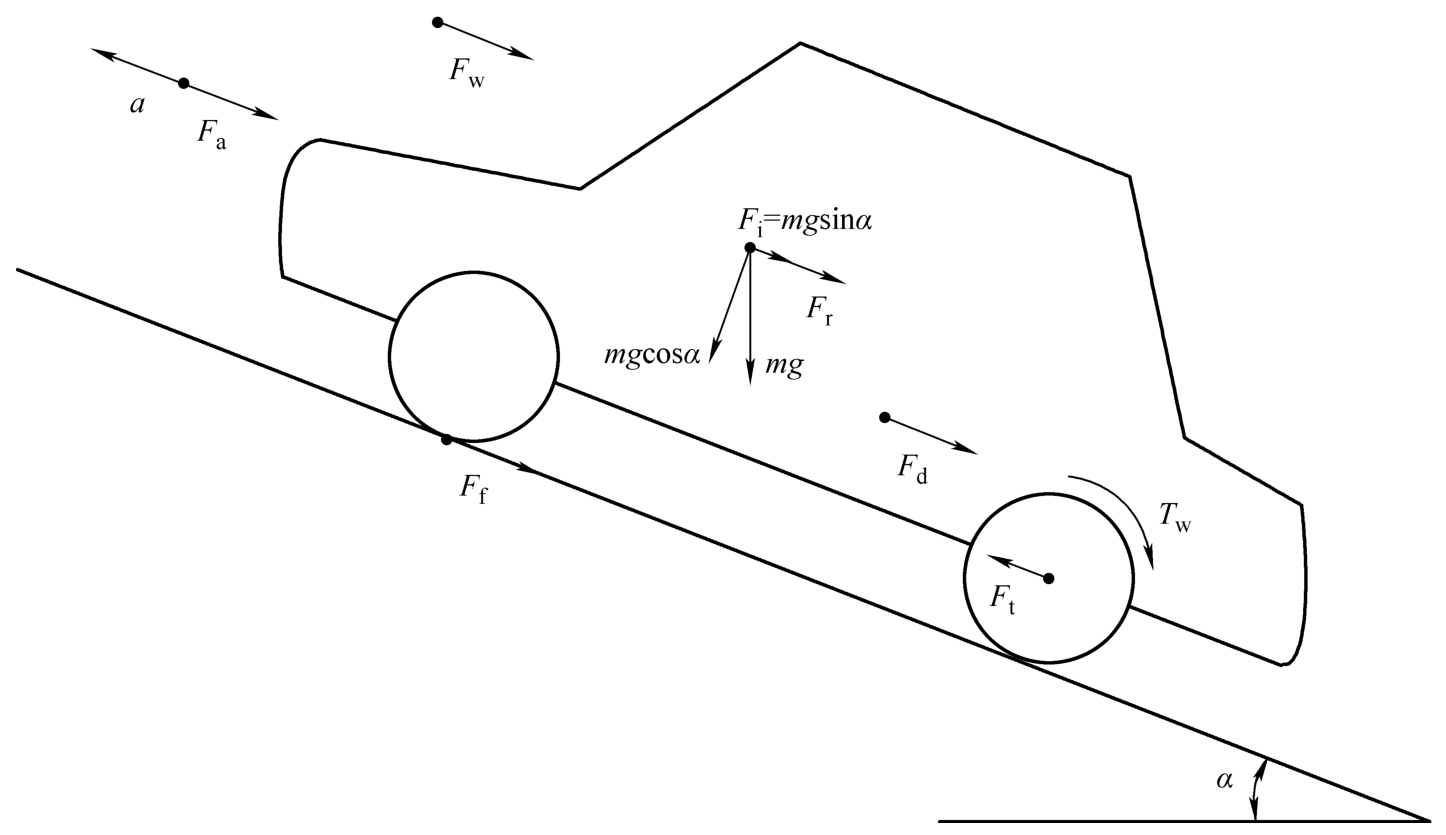
图1-9 作用于行驶中车辆上的力
:
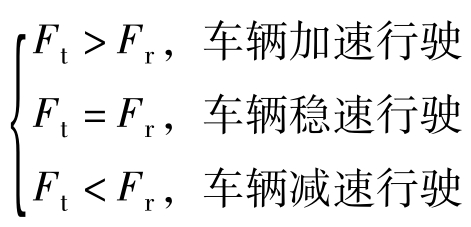
1.牵引力
车辆的牵引力由驱动单元的转矩产生,通过传动系统传递到驱动轮,克服车辆的阻力,以驱动车辆行驶。在满足附着条件的前提下,车辆的最大牵引力决定了车辆的动力性。牵引力受到驱动单元的特性、传动系统的传动比和效率等因素的影响。
由驱动单元传递到驱动轮的转矩可以用以下公式表示:

式中 T w ——驱动轮的转矩(N·m);
T p ——驱动单元的转矩(N·m);
i g ——变速器的传动比, i g = n in / n out , n in 为输入端转速, n out 为输出端转速;
i 0 ——主减速器的传动比;
η t ——从驱动单元到驱动轮的传动链的总效率,为离合器、变速器、传动轴、主减速器等传动系统的机械效率的乘积。
驱动轮上的牵引力,可表示为

式中 r ——轮胎滚动半径(m)。
将式(1-1)代入式(1-2)中,即得

2.车辆阻力
车辆的阻力包括空气阻力、轮胎滚动阻力、传动系统阻力、车辆行驶道路阻力、坡道阻力和加速阻力。
(1)空气阻力 空气阻力定义为车辆行驶时受到的阻碍其运动的空气的阻力,其主要有两方面的影响因素:迎风面积 A 和空气阻力系数 C D 。空气阻力的表达式如下:

式中 F w ——空气阻力(N);
C D ——空气阻力系数;
A ——迎风面积(m 2 );
u a ——车辆的行驶速度(km/h)。
(2)轮胎滚动阻力 轮胎滚动阻力基本上是源自于轮胎材料的滞变作用。轮胎滚动阻力的表达式如下:

式中 F f ——轮胎滚动阻力(N);
m ——车辆的质量(kg);
g ——重力加速度, g =9.806m/s 2 ;
f ——滚动阻力系数;
α ——路面的倾斜角(°),一般是在平直道路上测试轮胎滚动阻力,所以 α =0。
滚动阻力系数取决于轮胎的材料、结构、温度、充气压力、花纹形状、路面的粗糙度、路面的材料和路面上有无液体等因素。它对应于各种不同特征路面的典型值见表1-2。
表1-2 典型路面特征下的滚动阻力系数
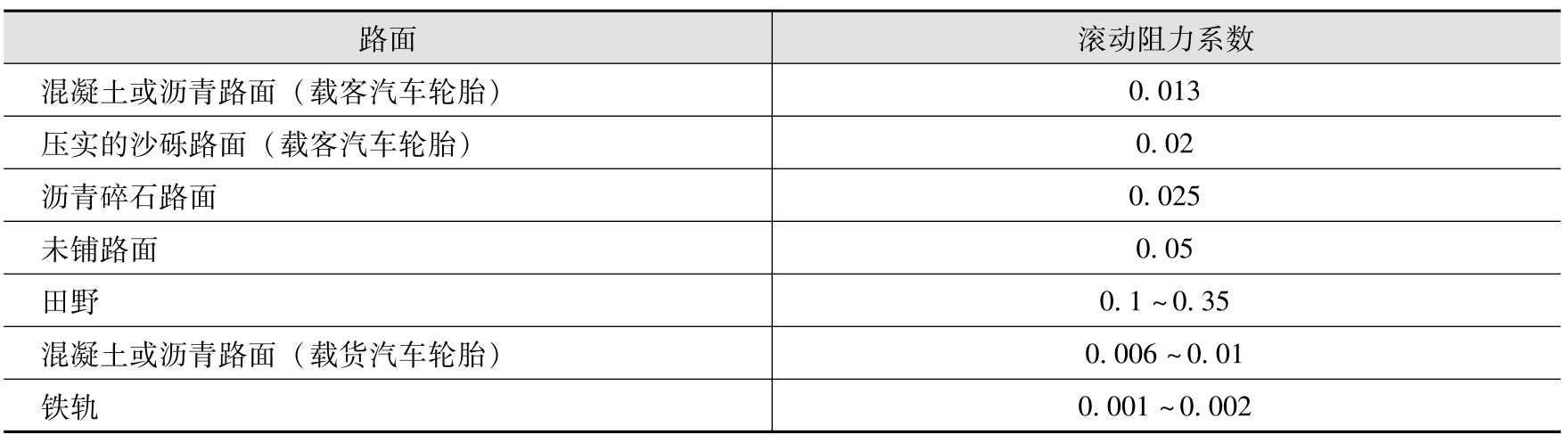
表1-2中给定的滚动阻力系数未考虑与车速之间的变化关系。基于实测结果,为计算在硬路面上的滚动阻力,博世公司提出了以下经验公式,该公式在车速≤128km/h的范围内有足够的精确度:

式中 f ——滚动阻力系数;
u a ——车辆的行驶速度(km/h)。
(3)传动系统阻力 传动系统阻力 F d 主要来源于变速器(及主减速器)、传动轴、轮毂轴承和制动拖滞力矩四个方面。
变速器和主减速器均主要由配对的齿轮系组成,阻力主要由摩擦阻力和寄生阻力组成。摩擦阻力的大小主要与传递转矩的大小有关,随转矩的增大而增大,主要来源包括齿轮啮合点的摩擦和与载荷相关的轴承摩擦。寄生阻力的大小主要与转速相关,随转速增大而增大,主要来源包括齿轮和轴的搅油损失,因润滑方式而异,如轮齿啮合时的挤油损失、齿轮在空气和油雾中的空气阻力、轴承内的挤油和游隙损失等。
传动轴阻力同样由摩擦阻力和寄生阻力组成。其中摩擦阻力主要来源于万向节球环/钢球与保持架间的摩擦;寄生阻力则来源于万向节内油脂的黏滞阻力、护套挤压的阻力。
轮毂轴承的阻力主要由以下几部分组成:密封圈摩擦阻力,约占总阻力的50%;钢球滚动阻力,约占总阻力的44%;润滑脂阻力,约占总阻力的6%。
制动拖滞力主要包括制动卡钳与制动盘的滑动摩擦阻力和活塞滑动阻力两部分。其中前者为主要部分,因为制动动作结束后,制动卡钳不能完全回位,此时若制动盘表面有不平整的毛刺、凸起等,则制动卡钳与制动盘非完全脱开,产生滑动摩擦阻力。
(4)车辆行驶道路阻力 由于轮胎滚动阻力的经验计算公式有一定的局限性,而传动系统阻力目前还没有一个精确度足够高的模型可以正向计算,一般通过滑行试验可以获得包括空气阻力、轮胎滚动阻力和传动系统阻力在内的车辆行驶道路阻力 F c :

进行滑行试验时,在平直干燥的路面上,将车辆加速至某车速(一般为130km/h),将变速器置于空档,车辆滑行至较低车速(一般为5km/h),记录滑行试验过程中的时间、车速,通过计算此过程中的减速度,再结合车辆的质量,可计算出车辆的滑行阻力,即车辆行驶道路阻力 F c ,其表达式如下:

式中 F c ——车辆行驶道路阻力(N);
A ——滑行阻力系数常数项(N);
B ——滑行阻力系数一次项[N/(km/h)];
C ——滑行阻力系数二次项[N/(km/h) 2 ];
u a ——车辆的行驶速度(km/h)。
上述试验规程的要求和滑行阻力系数的计算方法详见GB 18352.6—2016中附件CC。
(5)坡道阻力 当车辆爬坡时,其重力将产生一个指向下坡方向的分力,阻碍车辆爬坡。该分力的表达式如下:

式中 F i ——坡道阻力(N);
m ——车辆的质量(kg);
g ——重力加速度, g =9.806m/s 2 ;
α ——路面的倾斜角(°)。
路面的倾斜角 α 与坡度 i 之间有以下关系:

(6)加速阻力 车辆加速行驶时,需要克服因其质量产生的惯性力和惯性力矩。前者是由平移质量加速运动产生的阻力,后者是由旋转质量(如飞轮、离合器、变速器轴及齿轮、主减速器齿轮、传动轴及车轮等)加速旋转运动产生的惯性阻力矩。由于各旋转部件产生的阻力以内燃机的飞轮和车轮的数值为最大,故通常忽略其他部件的影响。
加速阻力的表达式如下:

式中 F a ——加速阻力(N);
J e ——内燃机飞轮的转动惯量(kg·m 2 );
J w ——全部车轮的转动惯量(kg·m 2 );
i g ——变速器的传动比, i g = n in / n out , n in 为输入端转速, n out 为输出端转速;
i 0 ——主减速器的传动比;
η t ——从驱动单元到驱动轮的传动链的总效率,为离合器、变速器、传动轴、主减速器等传动系统的机械效率的乘积;
g ——重力加速度, g =9.806m/s 2 ;
r ——轮胎滚动半径(m);
m ——车辆的质量(kg);
a ——车辆的加速度(m/s 2 )。
3.车辆动力学方程
车辆沿纵向运动的力学方程可表达为

车辆沿纵向运动的功率平衡表达式可表达为

即

由式(1-14)可以看出,尽可能地提高 F t 和减小 F c 是获得更好的动力性的关键。在建立了车辆动力学方程之后,就可以计算动力性和经济性了。
1.2.2 轮胎-道路力学模型
当车辆的牵引力超过轮胎与地面之间的附着力极限时,驱动轮将打滑。实际上,轮胎与地面的附着力有时是车辆性能的主要制约因素,这在潮湿、结冰、积雪或软土路面等低附路面上表现尤其明显。在这些情况下,作用于驱动轮的牵引转矩将使车轮在地面上产生显著的滑移。
(1)滑移率 汽车从纯滚动到抱死拖滑的过程是一个渐进的过程,经历了纯滚动、边滚边滑和纯滑动三个阶段。常用滑移率 s 来评价汽车车轮滑移成分所占比例的大小,在牵引状态下,其表达式为

式中 s ——滑移率(%);
u a ——车辆的行驶速度(km/h);
r ——轮胎滚动半径(m);
ω ——轮胎的角速度(rad/s)。
(2)最大牵引力 在一定的滑移率下,车辆的最大牵引力取决于附着系数。对于前轮驱动车型和后轮驱动车型,其表达式分别为
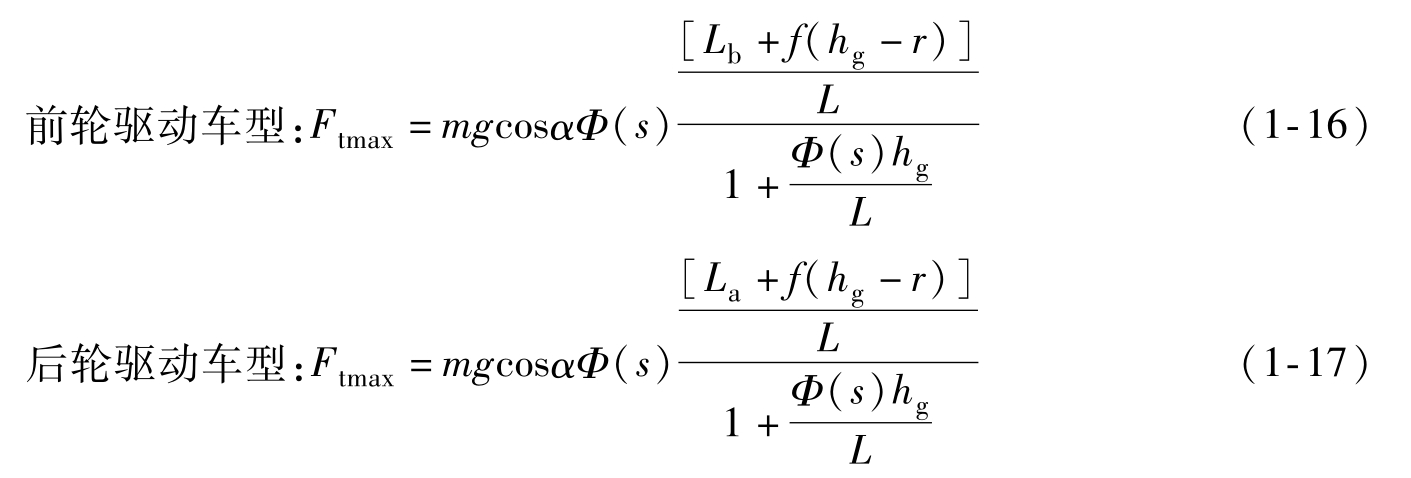
式中 F tmax ——车辆的最大牵引力(N);
m ——车辆的质量(kg);
g ——重力加速度, g =9.806m/s 2 ;
α ——路面的倾斜角(°);
Φ ( s )——附着系数,为滑移率的函数;
L ——车辆轴距(m);
L a ——车辆质心与前轴中心的距离(m);
L b ——车辆质心与后轴中心的距离(m);
f ——滚动阻力系数;
h g ——车辆的质心高度(m);
r ——轮胎滚动半径(m)。
干燥硬实路面附着系数与滑移率的关系如图1-10所示,车辆的纵向附着系数在滑移率为15%~20%时达到峰值,此时车辆能够获得最大的牵引力。
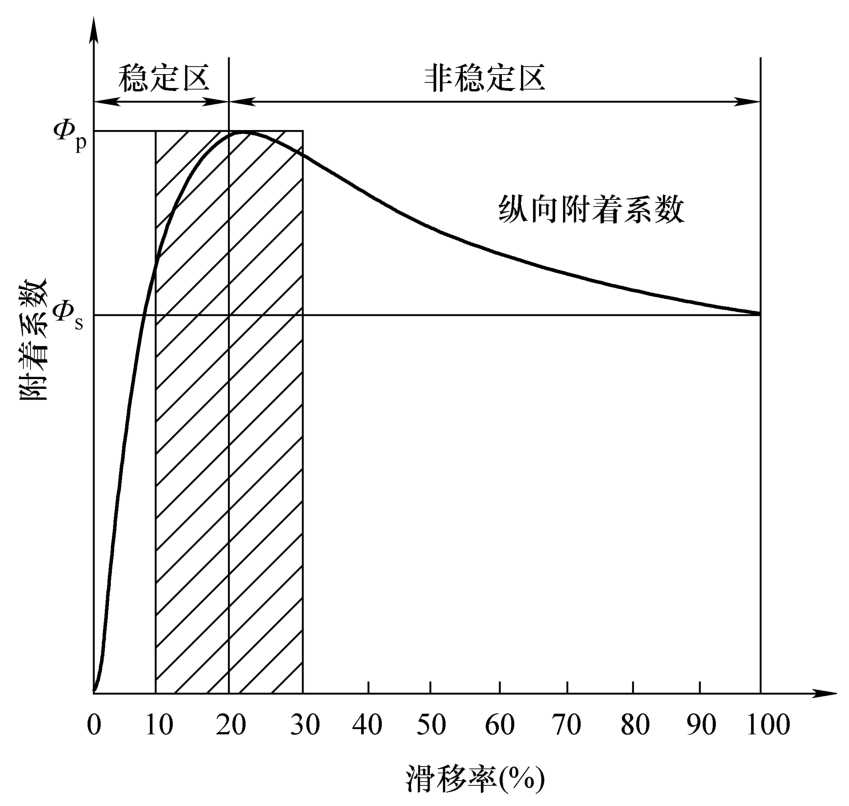
图1-10 干燥硬实路面附着系数与滑移率的关系
典型路面下的附着系数峰值和滑移值见表1-3。
表1-3 典型路面下的附着系数峰值和滑移值
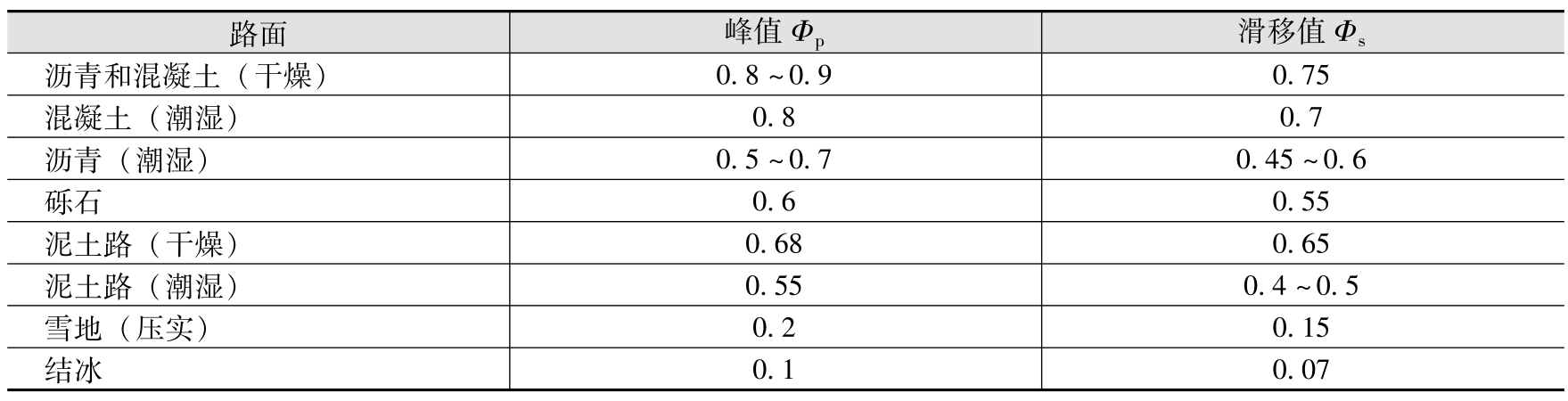
1.2.3 动力性和经济性理论计算
1.最高车速
最高车速受限于两方面因素:一是驱动单元的最大转速与传动系统传动比之间的平衡;二是车辆牵引力与阻力之间的平衡。
在上述第一种情况下,最高车速的表达式如下:

式中 u max ——最高车速(km/h);
n max ——驱动单元最高转速(r/min);
r ——轮胎滚动半径(m);
i g ——变速器的传动比, i g = n in / n out , n in 为输入端转速, n out 为输出端转速;
i 0 ——主减速器的传动比。
在第二种情况下,因为最高车速定义为在平坦路面上的最大稳速行驶车速,故而 a =0、 F i =0、 F a =0,则 F t = F c ,此时车辆动力学方程的表达式如下:

求解式(1-19)即可得到最高车速。
2.爬坡能力
根据爬坡能力的定义,最大爬坡能力出现在牵引力与道路行驶阻力加上坡道阻力之间达到平衡的时刻,此时 a =0、 F a =0,即 F t = F c + F i 。
此时车辆动力学方程的表达式如下:

因此

求解式(1-21)即可得到最大爬坡度。最大爬坡度一般出现在变速器置于一档时,因为一档的牵引力是最大的。
除了最大爬坡度以外,经常还要计算二档低速爬坡能力、高速爬坡能力和带拖车的坡起能力。
二档低速爬坡能力是为了确保车辆在较大坡度道路上行驶时能够稳定在一个较高的车速上(一般车速为 u =15~20km/h),以提高车辆的运行效率,避免影响山区道路的交通秩序。
高速爬坡能力(一般 u =120km/h)是为了保证车辆具有一定的高速巡航能力,而不至于在实际道路(国内部分地区的高速公路有最大坡度不超过3%的长坡道路)中巡航时产生较大的车速波动。有时为了弥补这种车速波动,需要调整换档策略以强制降档,获得更大的牵引力,这对于驾驶人的驾驶感来说是不可接受的。
某些车型还要考虑其拖拽能力,即带拖车状态下的性能。标准EU1230-2012要求车辆在拖挂制造商标称的拖车质量的状态下,能够在坡度≥12%的坡道上在5min之内坡起5次。这一要求主要考核的是车辆的爬坡能力和传动系统的承扭能力。
3.加速时间
根据加速时间的定义,车辆从低速 u 1 加速到高速 u 2 所需要的时间的表达式如下:

将式(1-12)代入式(1-22),此时车辆行驶在平坦路面上,故而 F i =0,可得

通过迭代计算式(1-23)即可得到加速时间。
4.能耗
(1)内燃机的油耗计算 针对1.1.2节介绍的能耗测试工况,可以根据内燃机的转矩需求和转速,在万有特性曲线中插值得到内燃机的比油耗BSFC,进而计算整个循环工况下内燃机的油耗。根据下式计算油耗:

式中 FC ——单个测试循环的油耗(g);
t c ——测试循环的时长(s);
BSFC——内燃机的比油耗(g/kW·h)。
可以将上述油耗值转换为百公里油耗值(L/100km),计算公式如下:

式中 ρ ——燃油密度(kg/L),通常国标汽油的密度为0.70~0.78kg/L,柴油的密度为0.83~0.855kg/L;
u a ( t ) ——t 时刻下测试循环要求的车速(km/h),详见1.1.2节描述的各循环工况的车速谱要求。
对于内燃机(ICE)车型,整车的轮边转矩需求都是靠内燃机来满足的,可以通过式(1-25)计算百公里油耗值。而对于混合动力电动汽车(HEV),整车的轮边转矩需求根据策略被全部或部分分配给内燃机,同时也存在完全依靠电机来满足转矩需求的情况,此时内燃机的油耗为0。针对这两种情况,需要计算加权油耗。
对于NEDC工况来说,HEV车型的加权油耗可以通过下式计算:

式中 C ——加权油耗(L/100km);
c 1 ——条件A试验中的油耗(L/100km);
c 2 ——条件B试验中的油耗(L/100km);
D e ——纯电续驶里程(km);
D av ——假设的储能装置两次充电之间的平均行驶里程,定义为25km。
其中关于条件A和条件B,以及纯电续驶里程的试验规程,详见GB/T 19753—2013。
对于WLTC和CLTC-P工况来说,HEV车型的加权油耗可以通过下式计算:

式中 C ——加权油耗(L/100km);
c 1 ——CD模式试验中的油耗(L/100km);
c 2 ——CS模式试验中的油耗(L/100km);
UF ——纯电利用系数,WLTC工况(相关规定详见GB 18352.6—2016)和CLTC-P工况(相关规定详见GB/T 19753—2013)针对其值的定义不同。
(2)电动汽车的电耗计算 针对1.1.2节介绍的能耗测试工况,纯电行驶工况时,可以根据整车的功率需求计算整个循环工况下车辆的电耗。可以根据下式计算电耗:

式中 EC ——单个测试循环的电耗(kW·h);
t c ——测试循环的时长(s);
P veh ( t ) ——t 时刻下整车的功率需求(kW)。
可以将上述电耗值转换为百公里电耗值(kW·h/100km),计算公式如下:

实际测试及计算百公里电耗值时,还需要考虑国家标准对于充电损耗方面的规定,对于上述计算值还需要进行修正。详见GB/T 18386—2017和GB/T 19753—2013的相关规定。
1.2.4 车辆模型构建及性能设计
理解车辆的构型,是对驱动单元、传动系统、储能系统和高压电系统进行模型构建,以及分析由这些模型组成的整车模型性能的基础。
1.车辆构型
车辆按照驱动系统的类别可以分为内燃机(ICE)汽车、纯电动汽车(BEV)、混合动力电动汽车(HEV)[包括插电式混合动力电动汽车(PHEV)]、氢燃料电池电动汽车等。图1-11所示为一些车型的基本构型。
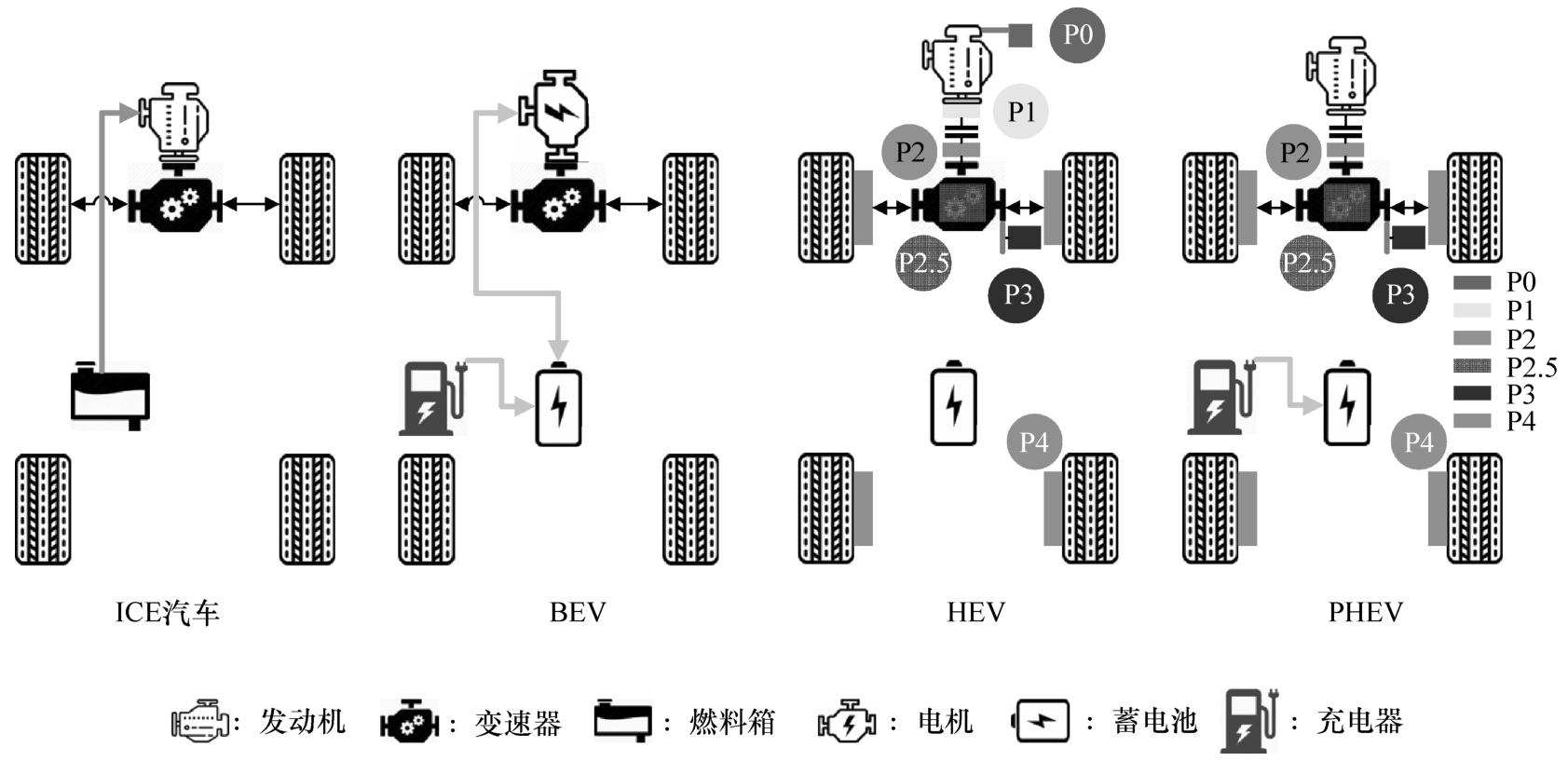
图1-11 车辆构型示意图
通过分析车辆的构型,可以得到整车模型包含的组成元件、各元件之间的关系、整车模型的运行模式,进而定义使整车模型性能最优的各组成元件的设计原则。
(1)内燃机(ICE)汽车 内燃机汽车的构型较为简单,内燃机是唯一的动力源,其组件布置如图1-12所示。
ICE车型的工作模式有两种,即驱动和内燃机制动。车辆驱动时,上述传动链的动力由内燃机通过传动系统最终传递到驱动轮;车辆滑行或制动时,道路阻力通过驱动轮、传动系统最终传递到内燃机,内燃机产生倒拖转矩,即内燃机制动。
(2)纯电动汽车(BEV)纯电动汽车的构型较为简单,电机是唯一的动力源,其组件布置如图1-13所示。
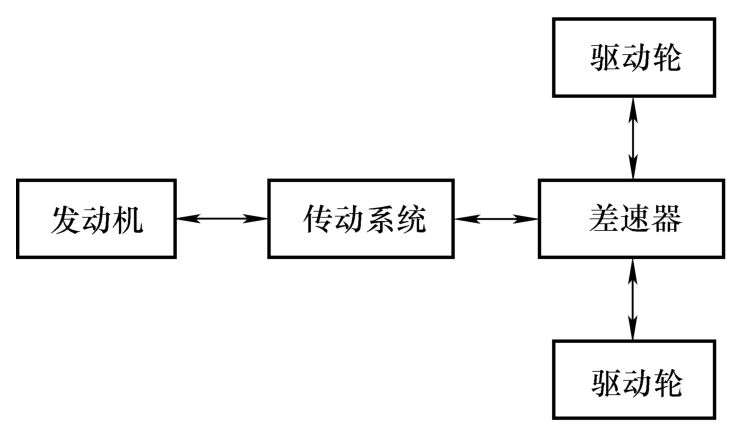
图1-12 ICE车型组件布置示意图
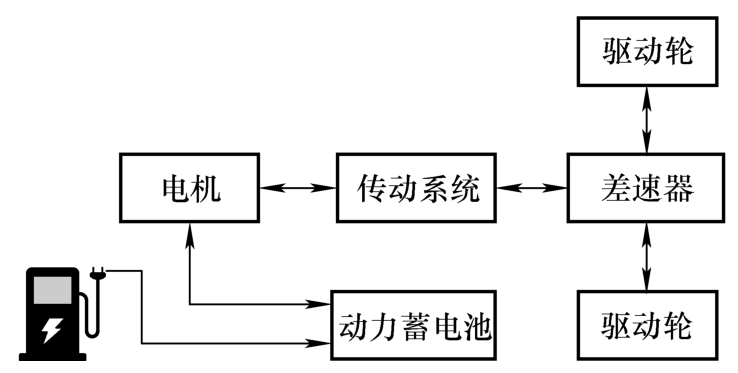
图1-13 BEV车型组件布置示意图
BEV车型的工作模式有两种,即电动和能量回收。车辆驱动时,上述传动链的动力由电机通过传动系统最终传递到驱动轮,此时电机的功能为电动,动力蓄电池放电;车辆滑行或制动时,道路阻力通过驱动轮、传动系统最终传递到电机,在满足能量回收策略要求的前提下,电机产生回馈转矩,此时电机的功能为发电,为动力蓄电池充电。
(3)混合动力电动汽车(HEV)混合动力电动汽车的优点是在满足日益严格的排放标准和驾驶质量需求提升的前提下显著提高汽车的燃油经济性。混合动力电动汽车结构复杂,驱动单元与传动系统控制有两种基本结构,其要求较高,而且这些控制过程通常是非线性的、参数变化迅速且在不确定和变化的环境下进行操作的,对于控制策略的合理性和鲁棒性有极高的要求。混合动力电动汽车基本上分为串联式、并联式和串并联混联式。
1)串联式HEV。串联式HEV中,电动机是唯一的动力源,内燃机驱动发电机发电,将电能储存于动力蓄电池中或者为电动机直接提供电能,动力蓄电池储存电能以驱动电动机,为车辆提供驱动力。其组件布置如图1-14所示。
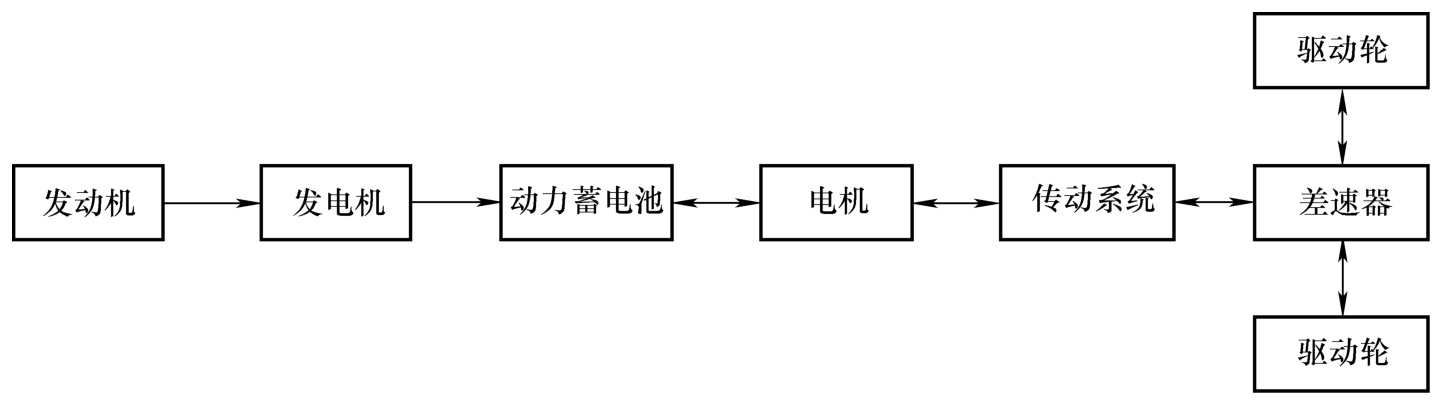
图1-14 串联式HEV车型组件布置示意图
串联式HEV的工作模式有三种:电动、发电、能量回收。
① 电动。当动力蓄电池的荷电状态满足驱动要求时,电动机驱动车辆行驶。
② 发电。当动力蓄电池的荷电状态不满足驱动要求时,内燃机驱动发电机发电,为动力蓄电池补充电能。
③ 能量回收。车辆滑行或制动时,道路阻力通过车轮最终传递到电机,在满足能量回收策略要求的前提下,电机产生回馈转矩,此时电机的功能为发电,动力蓄电池充电。
串联式HEV具有以下优点:
① 内燃机-发电机组的布置位置灵活。
② 传动系统简单。
③ 适用于需频繁起停的短途行驶。
串联式HEV具有以下缺点:
① 驱动系统需要3个组件:内燃机、发电机和电动机,这些组件均需为满足车辆的长距离、高速度行驶设计最高功率,成本较高。
② 仅有电动机驱动车辆,为满足车辆的需求,电动机要满足较大的功率要求(类似于BEV)。
2)并联式HEV。并联式HEV有多个动力源:一个内燃机和若干个电机。在并联式HEV中,内燃机和电机通过一个转矩耦合装置将两部分的转矩耦合。其组件布置如图1-15所示。
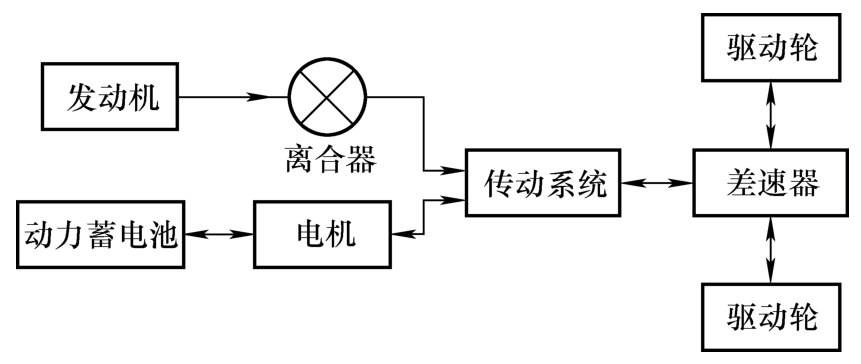
图1-15 并联式HEV车型组件布置示意图
根据电机在动力传动链上的布置位置,可以将并联结构分为以下几种类型:
① P0。电机通过传动带与内燃机曲轴相连,这种方式一般称为BSG,因混合度较低,也被称为微混。
② P1。电机与内燃机曲轴相连,位于离合器之前,在原本飞轮的位置上,这种方式一般称为ISG,因混合度较低,也是微混的一种。
③ P2。电机与变速器输入轴相连,在离合器之后。P2以上的构型,混合度较高,被称为强混。
④ P2.5。电机与变速器输入轴高度集成,可通过策略实现P2或P3的功能。
⑤ P3。电机的主减速器与变速器输出轴相连。
⑥ P4。电机的主减速器与驱动半轴相连。
并联式HEV具有以下优点:
① 驱动系统较串联式少,包括内燃机和电机,电机既可以作为电动机,也可以作为发电机。
② 内燃机和电机的功率可以设计得较小,两者并行运行为车辆提供其所需的全部功率。
并联式HEV具有缺点:
① 控制策略复杂,需要针对内燃机和电机进行功率分配。
② 内燃机和电机的功率耦合装置结构复杂。
3)串并联混联式HEV。串并联混联式结构结合了串联式和并联式结构的优点,可以工作在串联、并联和功率分配三种模式下。串并联混联式结构的控制策略有很大的灵活性,能够获得更好的动力性和燃油经济性。其组件布置如图1-16所示。
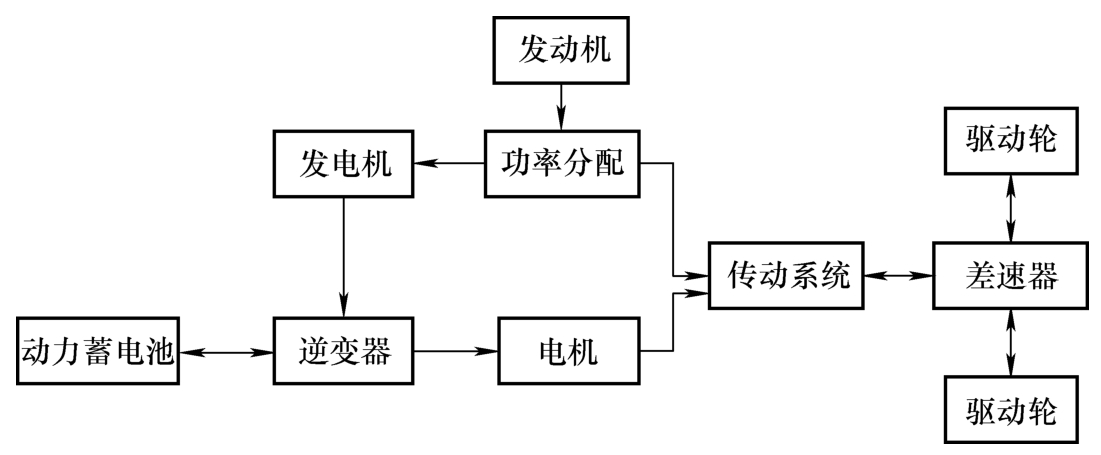
图1-16 串并联混联式HEV车型组件布置示意图
插电式混合动力电动汽车(PHEV)与一般的混合动力电动汽车(HEV)构型类似,只是比HEV多了可以与电网连接的充电接口。
串联式PHEV一般被称为增程式混合动力电动汽车(REEV),其组件布置如图1-17所示。
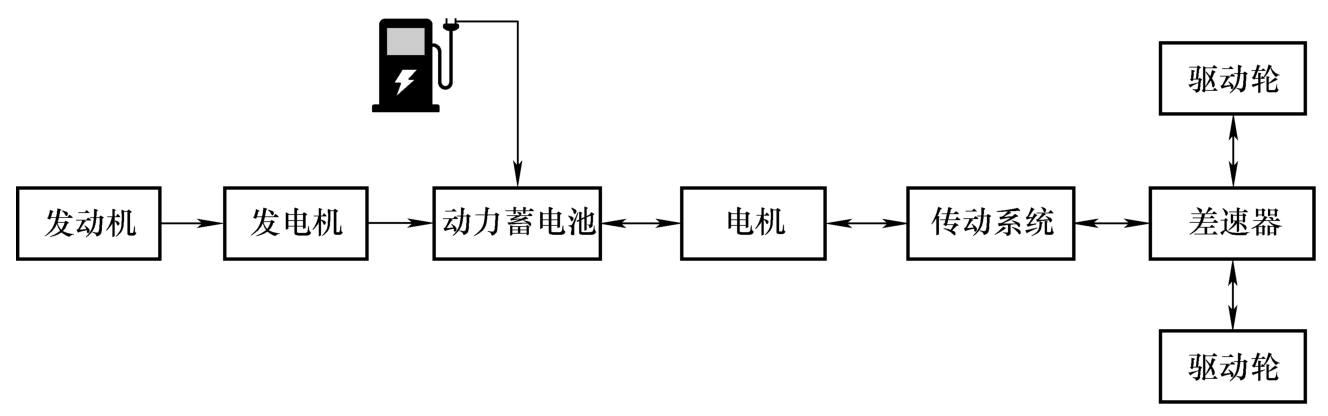
图1-17 串联式PHEV车型组件布置示意图
并联式PHEV的组件布置如图1-18所示。
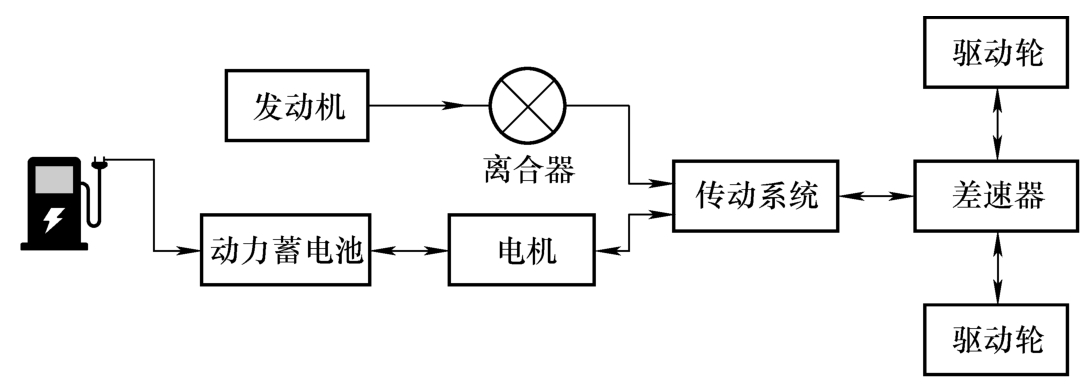
图1-18 并联式PHEV车型组件布置示意图
2.车辆模型的构建
Vehicle模块是Cruise仿真模型中最重要的模块之一。它包含了车辆的尺寸、质量、质心等基本参数,以及车辆行驶道路阻力和冷起动修正参数等必要参数。
(1)基本参数 Vehicle模块的基本参数见表1-4。
表1-4 Vehicle模块的基本参数

(续)
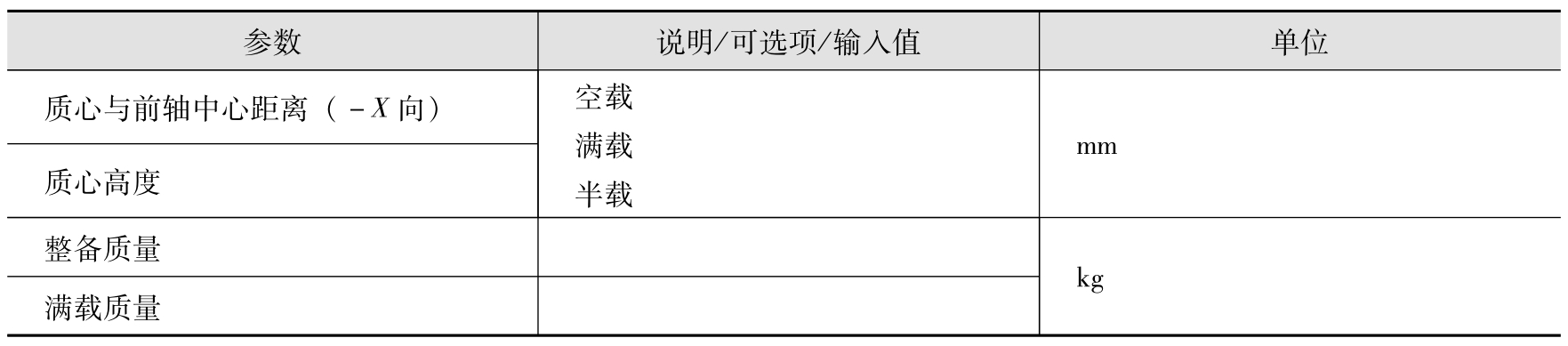
(2)车辆行驶道路阻力系数 车辆行驶道路阻力系数设定见表1-5。这组系数是计算车辆行驶道路阻力的必要参数。
表1-5 车辆行驶道路阻力系数设定
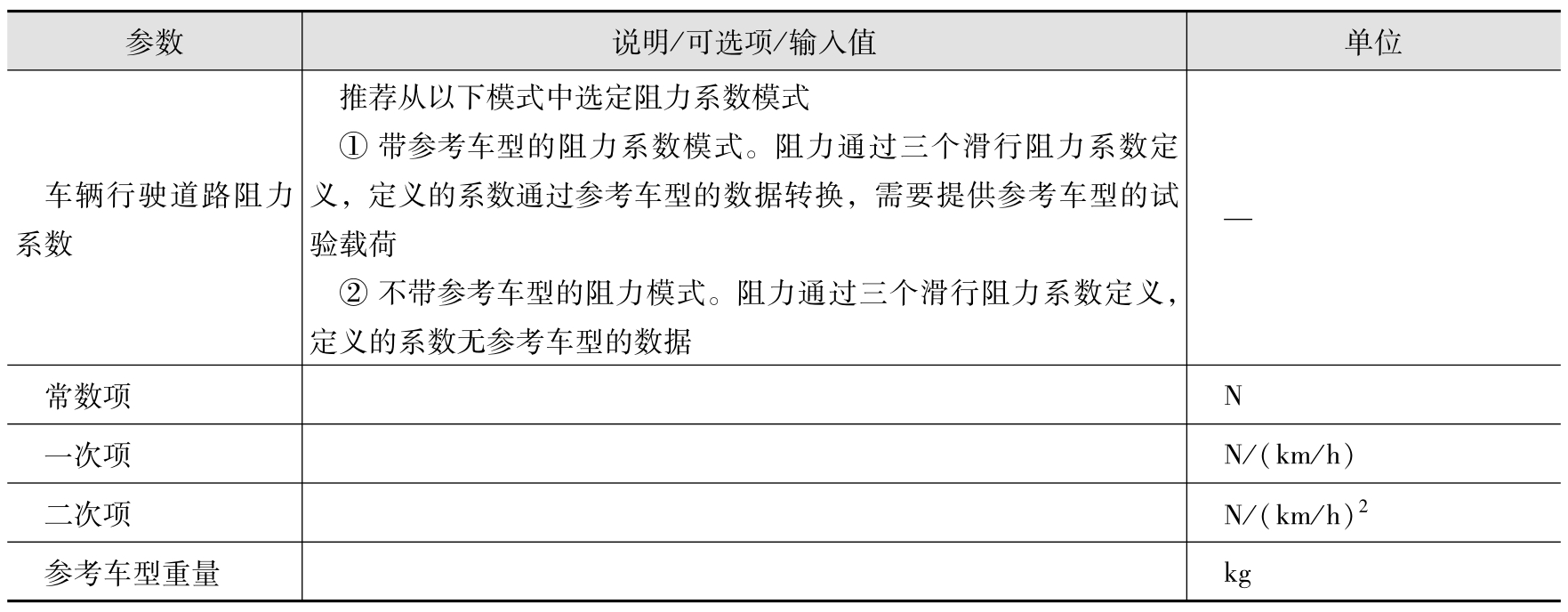
(3)冷起动修正参数 在内燃机处于冷态时,平均摩擦压力较高,且排放标定过程中为了在冷态下减少部分排放物而调整喷油参数,导致发动机多喷油,此时内燃机具有较高的燃油消耗率。为此,可以通过冷起动修正参数来修正循环工况下的实际油耗。如果激活了冷起动修正功能,则实际燃油消耗将始终乘以该冷起动修正系数。图1-19所示为自动变速车型NEDC工况下的冷起动修正系数建议值。
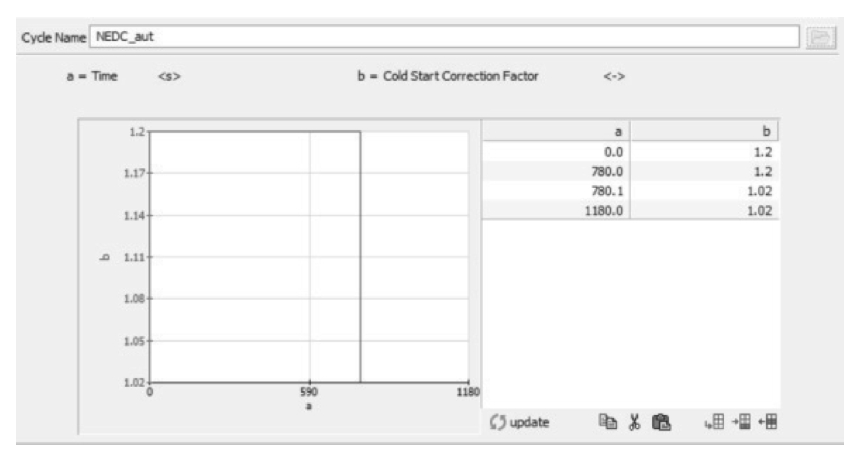
图1-19 自动变速车型NEDC工况下的冷起动修正系数建议值
1.2.5 驱动单元性能设计
驱动单元为车辆提供牵引力,通常由内燃机、电机或氢燃料电池中的一种或多种(取决于车辆构型)组成。驱动单元最理想的运行特性是在其全转速范围内为恒功率输出,此时转矩随转速呈双曲线形,驱动单元在任何车速下都能全功率输出,因而车辆的动力性是最佳的。以下分析内燃机和电机的实际运行特性。
1.内燃机
内燃机设计性能指标的首要考虑因素是在成本合适的情况下保证满足使用需求,其次是使用可靠,最后才是主要指标。本节主要论述影响车辆动力性的内燃机特性参数、内燃机模型的构建及提升内燃机性能的先进技术。
(1)类别及性能指征 内燃机通过内部燃烧将燃料的化学能转化为机械能。汽车用内燃机的分类方式及类别见表1-6。乘用车常用的内燃机为汽油机和柴油机,本书以介绍这两种内燃机为主。
表1-6 内燃机的分类方式及类别
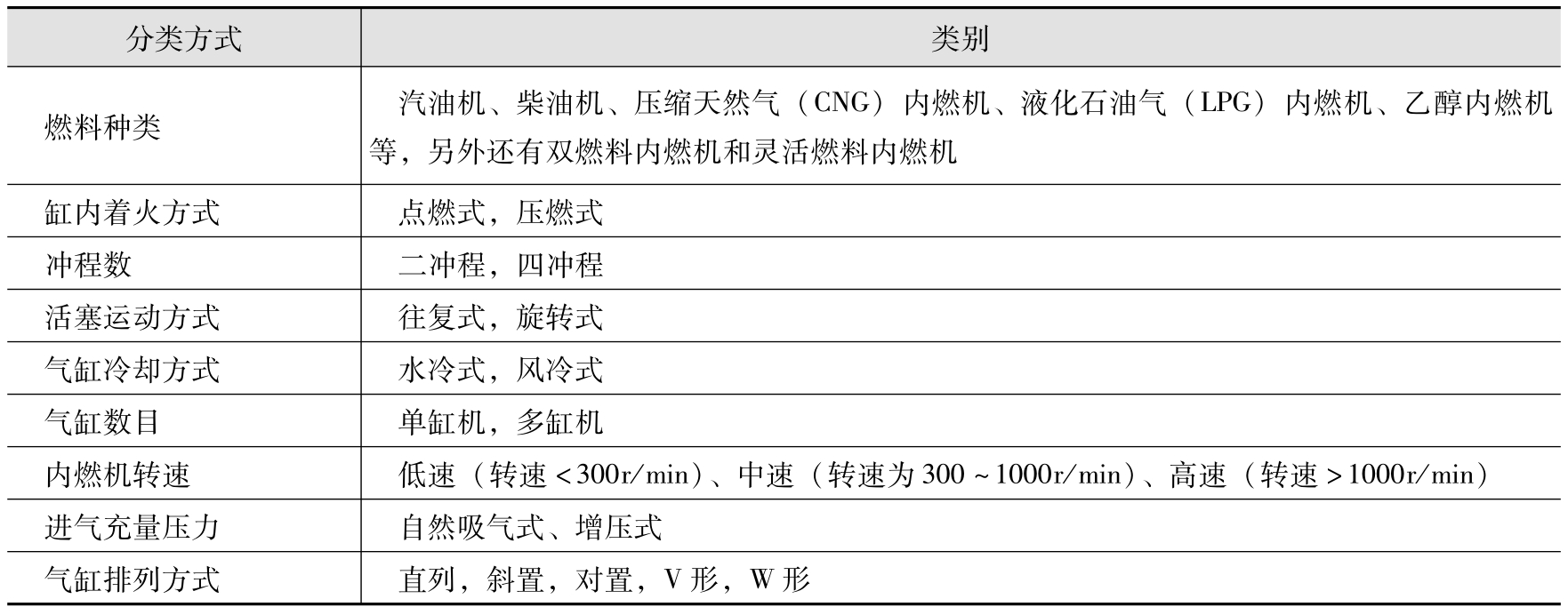
内燃机的基本原理已有大量的文献资料及专著进行了阐述,本书主要关注内燃机在汽车上应用时的设计要点,着重于与其性能相关的特性参数。
最大功率、最大转矩及其对应的内燃机转速,是内燃机的主要表征参数,它们决定了内燃机的主要性能指标。内燃机特定转速区间下的转矩决定了特定区间内的内燃机的性能。上述指标用于确定内燃机的外特性。
1)最大功率转速 n p 。 n p 值的选定对于最高车速有很大的影响。增大 n p 值是提高内燃机功率和减小质量最为有效的措施。
一般来说, n p 值可根据内燃机的技术水平进行计算:

式中 k ——技术水平系数,一般取 k =0.5~1.0,对于采用增压、增压中冷、谐波进气等特殊措施的内燃机,可偏于下限取值;
n pm ——内燃机最大功率转速的最高值,一般柴油机取4410r/min,汽油机取6750r/min。
2)最大转速 n m 。内燃机的最大转速由内燃机的最高允许转速决定。内燃机的最大转速一般可由下式计算:

因为汽车的最高车速相当于内燃机最大功率点的车速时是最大的,所以为了获得更好的适应性,式(1-31)中的系数偏于上限取值。
3)最大功率 P m 。 P m 值大,动力性就好,但过大时功率利用率低,燃油经济性差,且动力传动系统的质量也将增加。
一般来说, P m 值可根据最高车速的要求进行计算:

式中 F c ——滑行阻力(N),通过滑行试验测得;
η a ——内燃机外特性缩减系数,一般取0.95;
η t ——传动系的效率,包含变速器效率(0.94~0.98)、传动轴效率(0.96~0.98)、驱动桥效率(最大负荷工况下为0.94~0.96)等;
u max ——最高车速(km/h);
δ ——最高车速时的内燃机功率偏移系数,一般取1.03。
4)最大转矩 T m 。最大转矩决定了汽车的驱动力、加速性能和爬坡性能等动力性参数。最大转矩越大,汽车动力性越好。但转矩过大,除转矩利用率低外,还必然使内燃机和传动系统的质量增大。合理的最大转矩值应根据性能要求选定。
下面以最大爬坡度要求来计算需要的最大转矩:

式中 F c ——滑行阻力(N),通过滑行试验测得,这里一般考虑车速为0时的滑行阻力;
m ——满载质量(kg);
i max ——最大爬坡度(%);
r ——轮胎滚动半径(m);
i g ——变速器的传动比,这里一般是一档传动比 i g1 ;
i c ——分动器的传动比,一般分为高、低档。
项目定义初期, i g i 0 i c 一般暂未确定,可参考竞品车的参数,大致定义一个范围,项目的 i g i 0 i c 定义在17~19的范围内; r 也未确定,一般根据项目输入的轮胎数据选取经验值进行计算,某车型选取245/65 R16轮胎,则其 r ≈0.364m。
5)最大转矩转速 n t 。最大转矩转速与最大功率转速有密切的关系,过于靠近则内燃机对于负荷变化的适应能力降低,高档利用率降低,高档最低稳定车速偏高,变速器的换档频次增高。反之,如果过于拉开,则内燃机的平均加速功率下降,动力性变差。
一般来说, n t 值可根据动力特性的分配关系进行计算:

式中 λ ——分配系数,一般柴油机取2.4(1±10%),汽油机取3.0(1±10%);
e t ——转矩因子, e t = T m / T p 。
6)内燃机低转速区间的转矩。内燃机低转速区间的转矩影响汽车的低速爬坡性能,相关的动力性指标为20km/h车速下二档最大爬坡度。
下面以20km/h车速下二档最大爬坡度要求来计算需要的转矩:

式中 T i20 ——20km/h车速下二档时发动机的最大转矩需求;
F c ——滑行阻力(N),通过滑行试验测得,这里考虑车速为20km/h时的滑行阻力;
m ——满载质量(kg);
i 20 ——20km/h车速下二档最大爬坡度(%),动力性目标;
i g ——变速器的传动比,这里是二档传动比 i g2 。
(2)内燃机模型的构建 内燃机的实际工作过程非常复杂,在构建内燃机模型进行动力性、经济性仿真时需要做一些必要的简化,仅使用内燃机的基本参数和特性参数来描述内燃机输入-输出的静态机械特征,而不分析内燃机内部燃烧过程和热动力学特性。
1)内燃机的工作状态。了解内燃机的工作状态,才能有针对性地简化内燃机模型,以必须的特性参数进行性能仿真。内燃机通常有四个工作状态:起动、怠速、工作、关闭。
内燃机起动状态下,起动机克服内燃机的阻力,使内燃机达到稳速运行的状态。内燃机的阻力来源于内燃机转动惯量、机械附件损耗和闭节气门转矩。其中闭节气门转矩是由静摩擦、黏性摩擦、库仑摩擦和制动压缩转矩产生的。内燃机起动状态的原理图如图1-20所示。
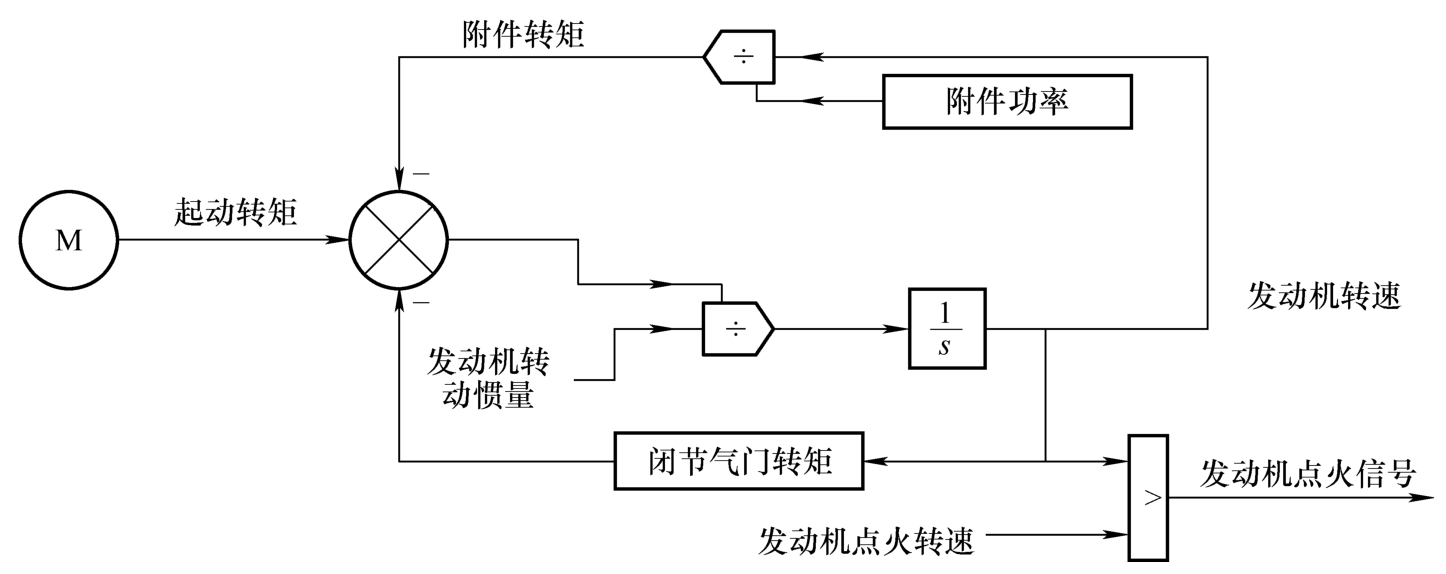
图1-20 内燃机起动状态的原理图
当离合器分离时,调节器使内燃机保持在理想的怠速转速状态下。一般调节器是PID(比例、积分、微分)控制器,关于PID控制器的原理,有兴趣的读者可以参阅其他相关书籍。内燃机怠速状态的原理图如图1-21所示。
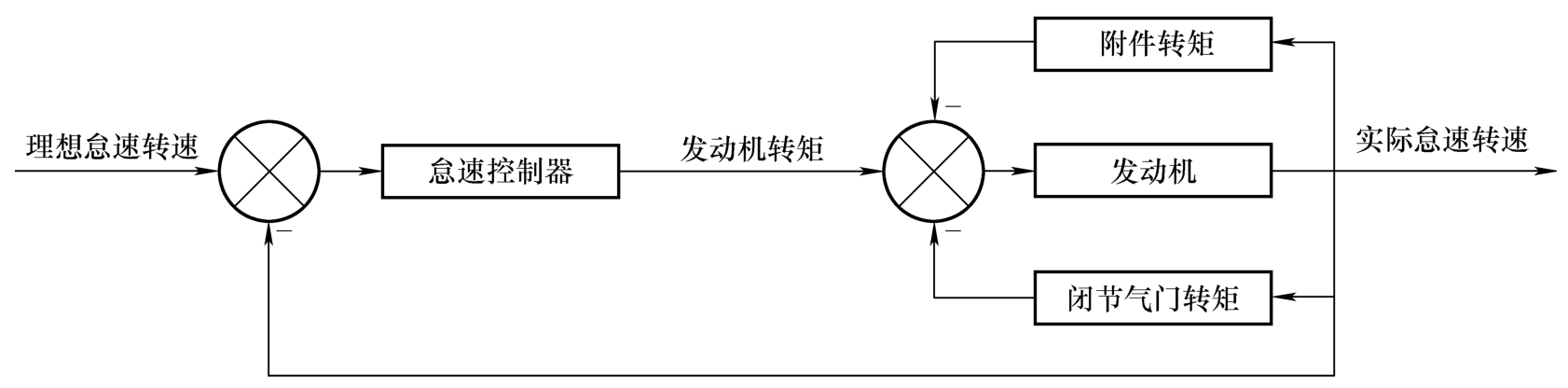
图1-21 内燃机怠速状态的原理图
内燃机工作时,离合器接合(或滑摩,此时离合器部分传递转矩),内燃机通过传动系统为车辆提供牵引力。
内燃机关闭时,产生反向转矩进行制动。内燃机的反向转矩由附件转矩和闭节气门转矩组成。
采用AVL Cruise进行车辆动力性仿真分析时,一般要用到以下内燃机基本参数、外特性曲线、万有特性曲线和倒拖转矩曲线。
2)基本参数。在AVL Cruise中设置内燃机模型,首先需要输入一些基本参数。必须的基本参数见表1-7。
表1-7 内燃机模型基本参数
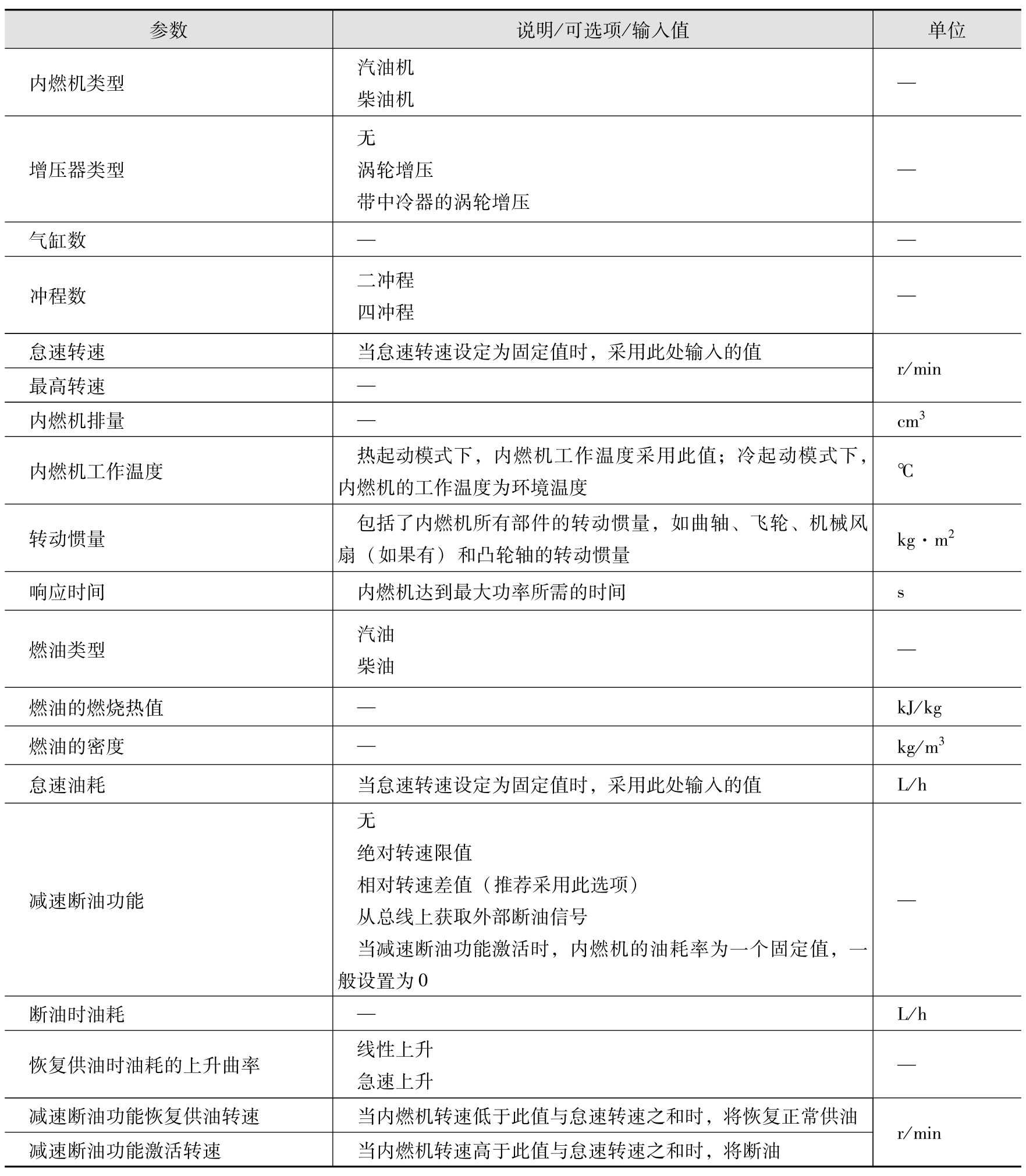
3)外特性曲线。内燃机外特性曲线是当内燃机节气门开度为100%时测得的内燃机输出功率(转矩)随转速变化的曲线。内燃机的外特性是计算其牵引力的最重要的参数。典型的内燃机外特性曲线如图1-22所示。
4)万有特性曲线。以转速 n 为横坐标,以转矩 T tq 或平均有效压力 P me 为纵坐标,画出等油耗率曲线和等功率曲线,组成内燃机万有特性曲线。根据需要还可以画出等过量空气系数曲线、等进气管真空度曲线、冒烟极限等。
万有特性曲线实质上是所有负荷特性和速度特性曲线的合成。它可以表示内燃机在整个工作范围内主要参数的变化关系,用它可以确定内燃机最经济的工作区域,当然也可以确定某一污染物排放量的最小值区域等。在内燃机参数匹配过程中,通过参数匹配使这些最佳性能区域落在最常用的工况范围内,这是内燃机性能匹配的重要原则之一。典型的内燃机万有特性曲线如图1-23所示。
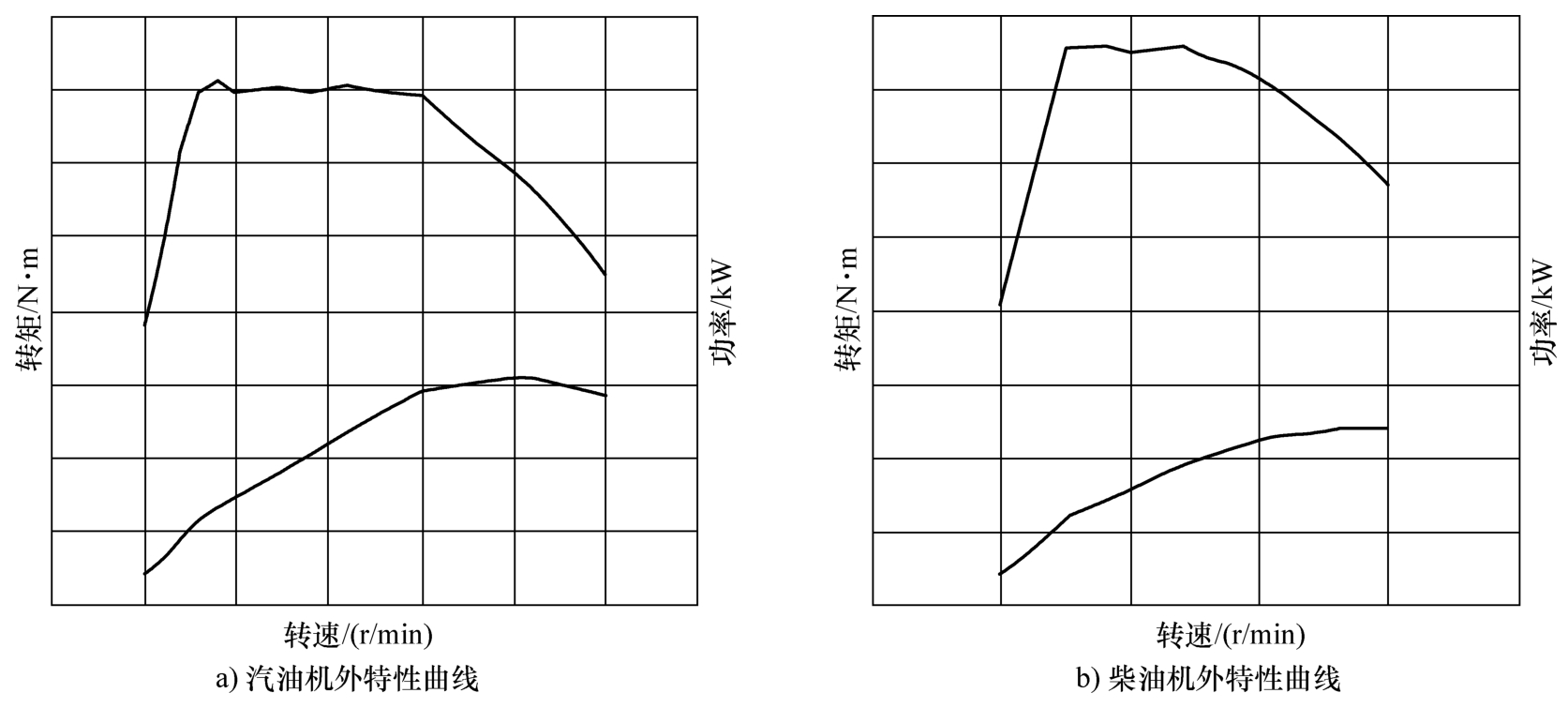
图1-22 典型的内燃机外特性曲线
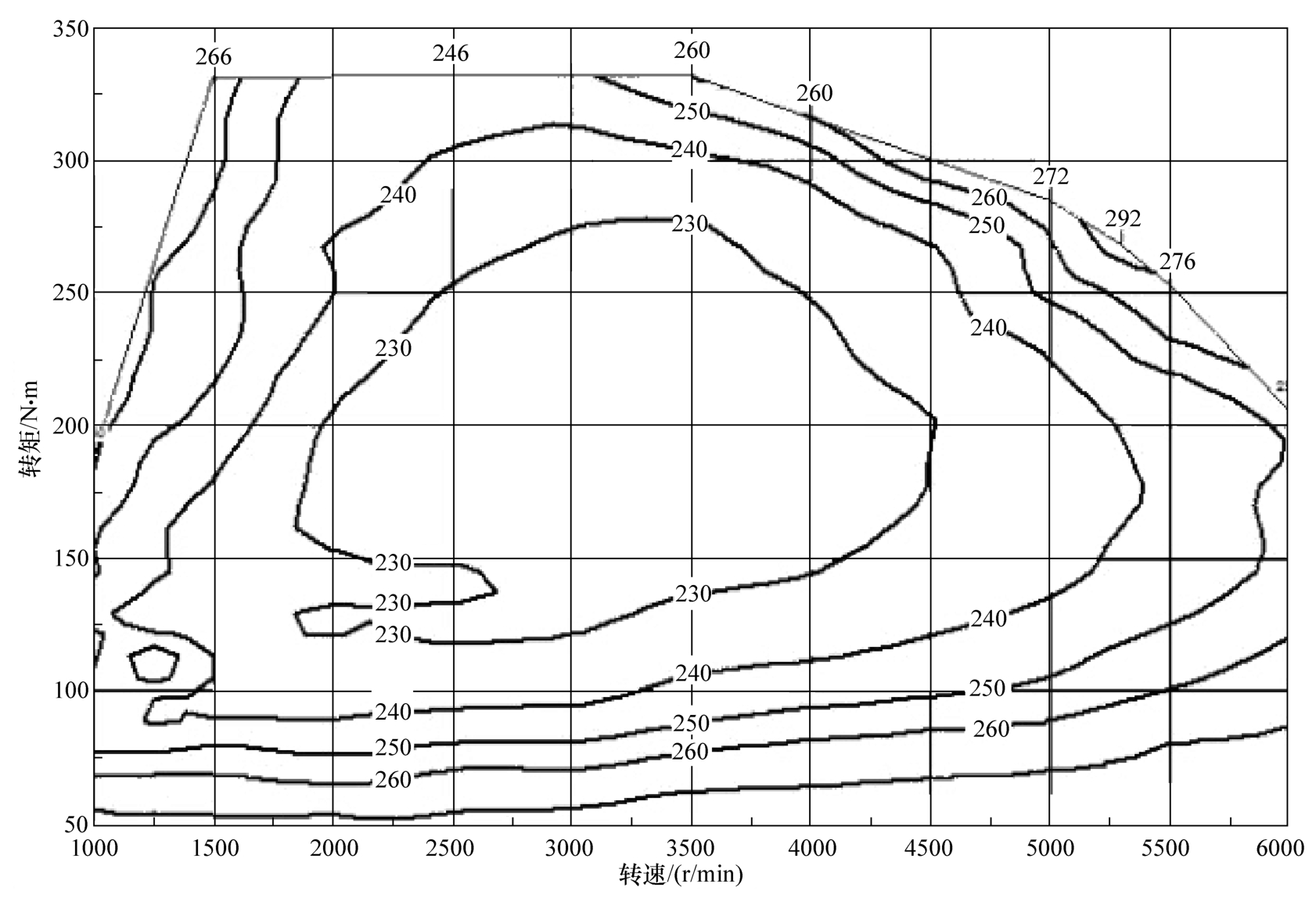
图1-23 典型的内燃机万有特性曲线
从台架试验中获取的万有特性一般包含了内燃机转速 n 、内燃机转矩 T tq 和比油耗BSFC。在AVL Cruise中,用质量流量来替代比油耗BSFC进行油耗计算,其表达式如下

式中 q m ——质量流量(kg/h);
n ——内燃机转速(r/min);
T tq ——内燃机转矩(N·m);
BSFC——有效燃油消耗率,即比油耗(g/kW·h)。
因为在台架试验过程中,一般以内燃机转速1000r/min为起点开始测量万有特性数据,故而在Cruise中,对于内燃机零转矩至该转速的倒拖转矩峰值区间内,比油耗需要根据该转速下相邻转矩下已有的比油耗值外推相应的值。这种外推值并不准确,为了避免Cruise外推比油耗值,可以手动插值得到0转矩时的比油耗值,然后使该转速下0转矩至倒拖转矩区间内的比油耗均等于该值,如图1-24所示,图中
表示不同的发动机转速(r/min)。
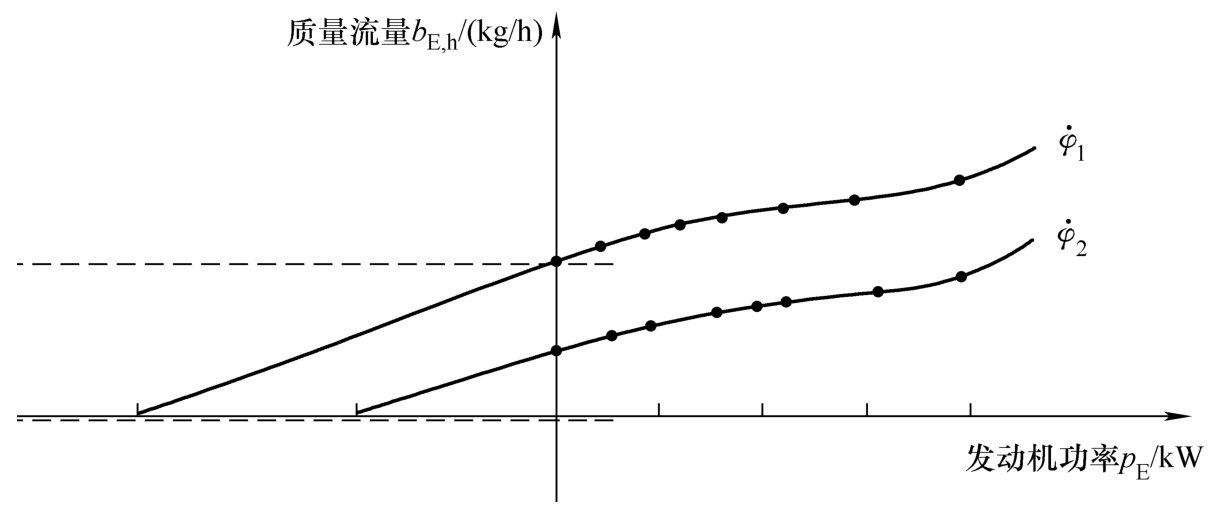
图1-24 万有特性曲线修正示意图
5)倒拖转矩曲线。当车辆滑行或制动时,内燃机因断油而处于关闭状态,此时内燃机产生倒拖转矩,触发内燃机制动。典型内燃机的倒拖转矩曲线如图1-25所示。
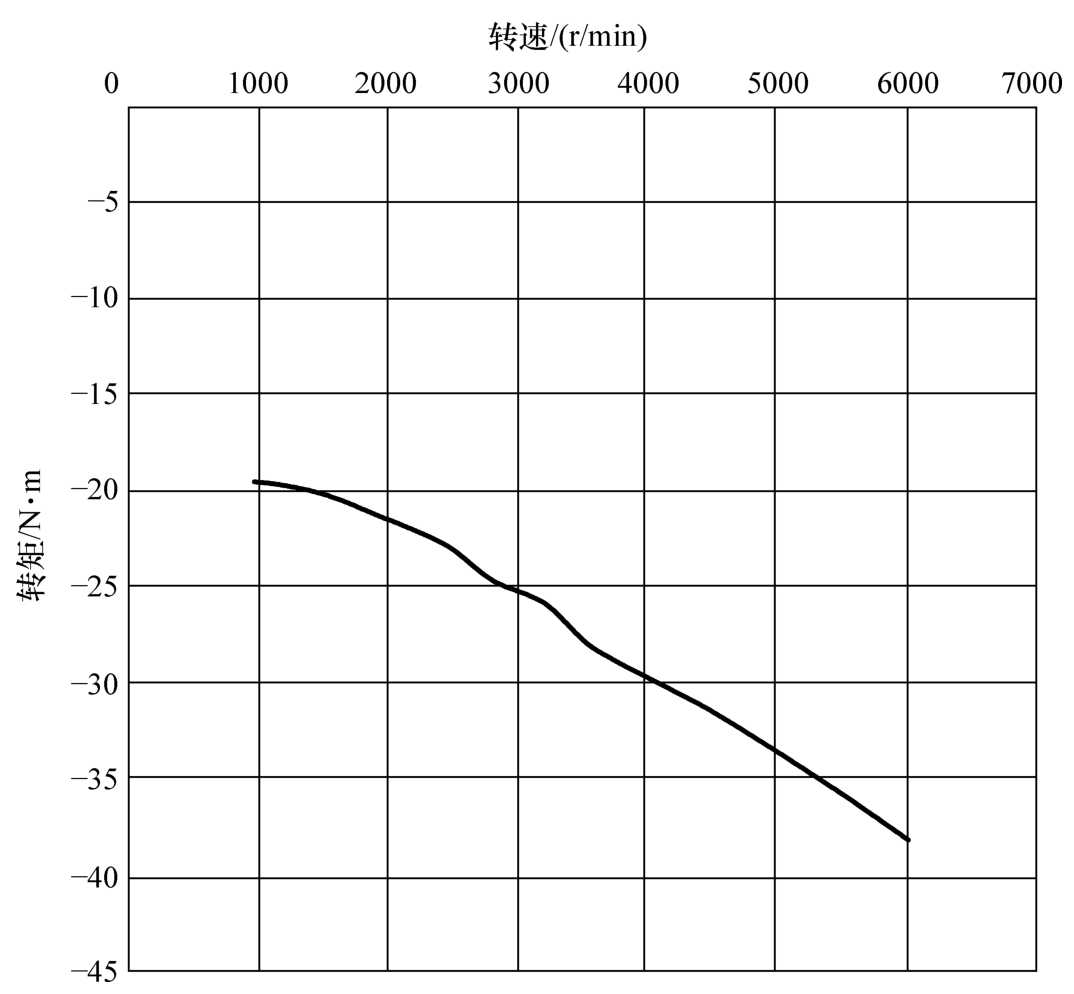
图1-25 倒拖转矩曲线
2.电机
电机是一种将电能与机械能相互转换的电磁装置。在车辆行驶时,电机可以处理储能系统所提供的能量并通过传动系统向轮边传递功率和转矩;当车辆制动时,还可以将车轮传递过来的机械能转换为电能并存储到储能系统中。
当电机将电能转化为机械能时,称为电动机;当电机将机械能转化为电能时,称为发电机。一般将电机的制动模式称为再生制动。
(1)类别及基本原理 汽车用电机有图1-26所示的分类方式,乘用车常用的是笼型异步电机(也被称为感应电机,IM)和永磁同步电机(PMSM)。本书以介绍永磁同步电机为主。
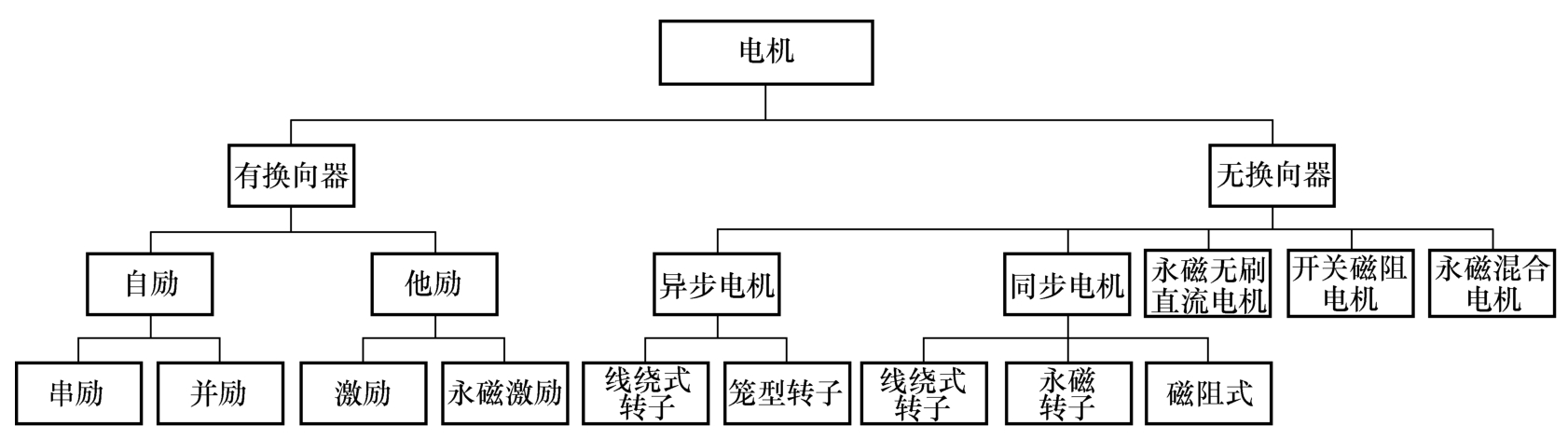
图1-26 汽车用电机分类
广义的电机指的是电机驱动系统,包括了电机和绝缘栅双极型晶体管(IGBT),并且通过直流-交流(DC-AC)变换器(逆变器)与动力蓄电池相连。
感应电机的控制原理图如图1-27所示。因为感应电机需要交流电的输入,需要通过逆变器将电池输出的直流电转换为交流电。一般通过矢量控制技术来控制感应电机的转矩-转速关系,总的来说,矢量控制技术利用感应电机的动力学等效电路将定子电流解耦成两个垂直分量,一个产生磁场,一个产生转矩,这样就可以像直流电机控制器一样独立控制。感应电机分析中最重要的一个变量为转差率,是转差速度与异步速度的比值。
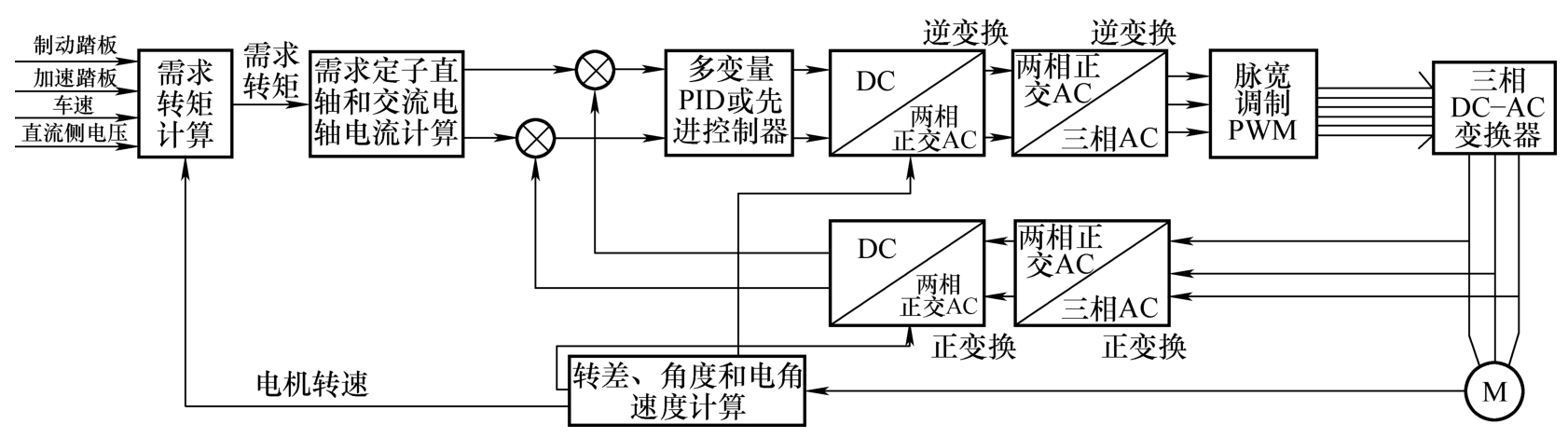
图1-27 感应电机的控制原理图
永磁同步电机的控制原理图如图1-28所示。永磁同步电机同感应电机一样,通过逆变器从动力蓄电池获取能量。在恒转矩区域,通过位置传感器和电流传感器的协助调整电机的电流,从而使电机输出平滑的转矩。而在恒功率区域,永磁同步电机工作在弱磁模式,使电机能够工作在较高的转速下。
感应电机和永磁同步电机具有表1-8所列的特点。
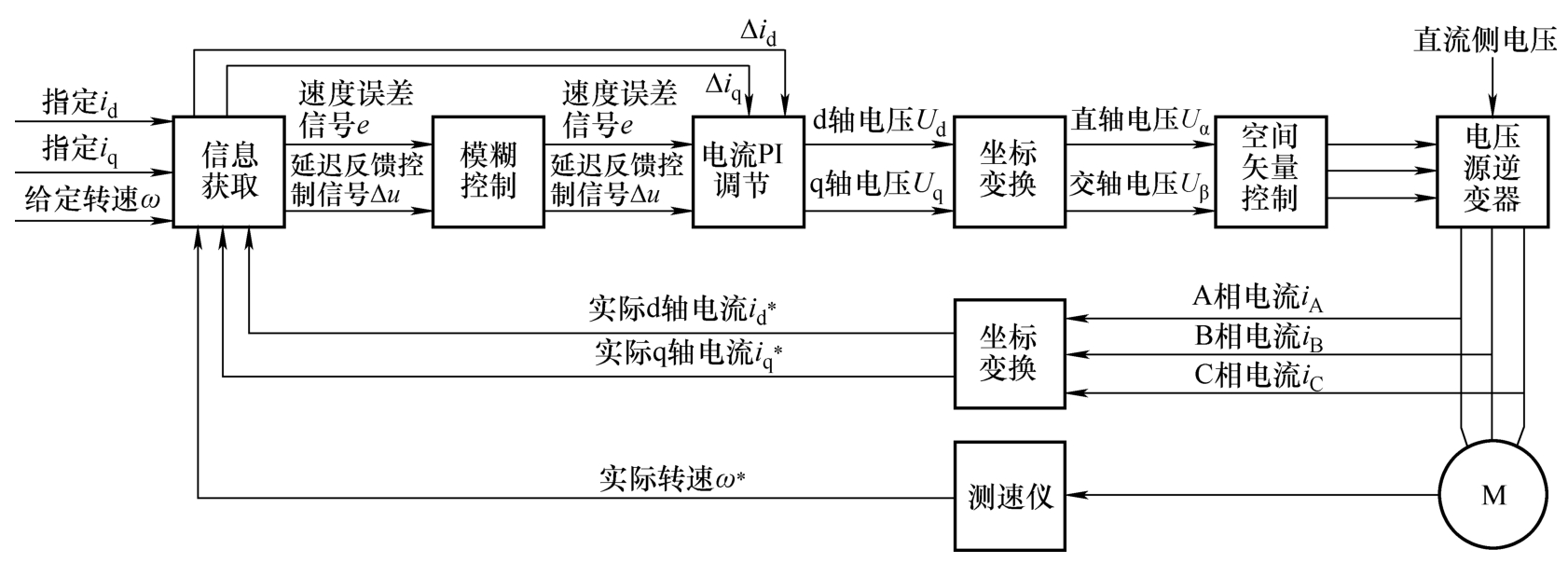
图1-28 永磁同步电机的控制原理图
表1-8 感应电机和永磁同步电机的特点
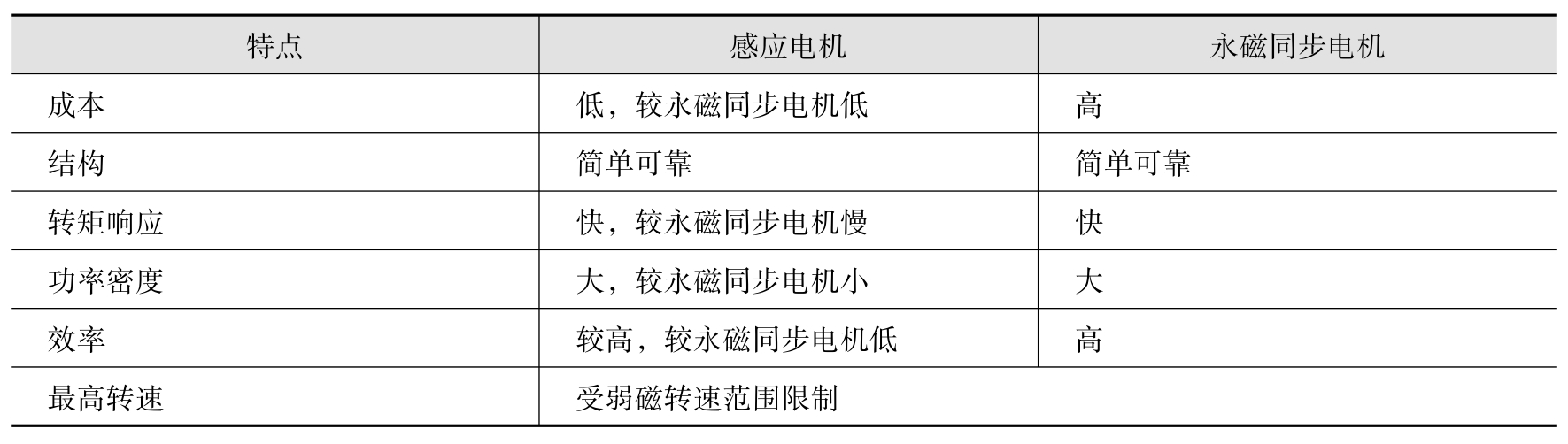
(2)电机模型的构建 不同种类的电机具有不同的结构和转矩-转速特性,但是在进行系统性能仿真时可以认为相同,因为只需要用到电机的外部电学特性和机械特性。
1)电机的工作状态。电机具有图1-29所示的四象限工作模式。因此电机控制器的主要任务就是在电机的四种工作模式下调节电机旋转方向、电机转速和维持所需的转矩。
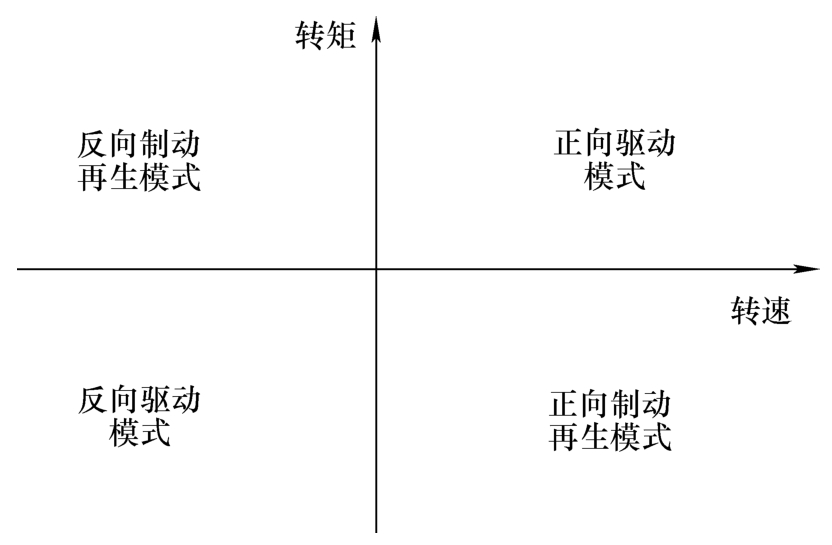
图1-29 电机的四象限工作模式
① 正向驱动模式。动力蓄电池给电机供电,电机驱动车辆正向行驶。
② 反向驱动模式。动力蓄电池给电机供电,电机驱动车辆反向行驶。
③ 正向制动再生模式。电机做制动能量回收,为动力蓄电池充电,车辆正向滑行或制动。
④ 反向制动再生模式。电机做制动能量回收,为动力蓄电池充电,车辆反向滑行或制动。
2)基本参数。在AVL Cruise中EM(Electric Machine)需要设定表1-9所列的基本参数。
3)外特性曲线。电机的理想输出特性曲线如图1-30所示,某电机实际峰值外特性曲线如图1-31所示。
表1-9 电机模型的基本参数
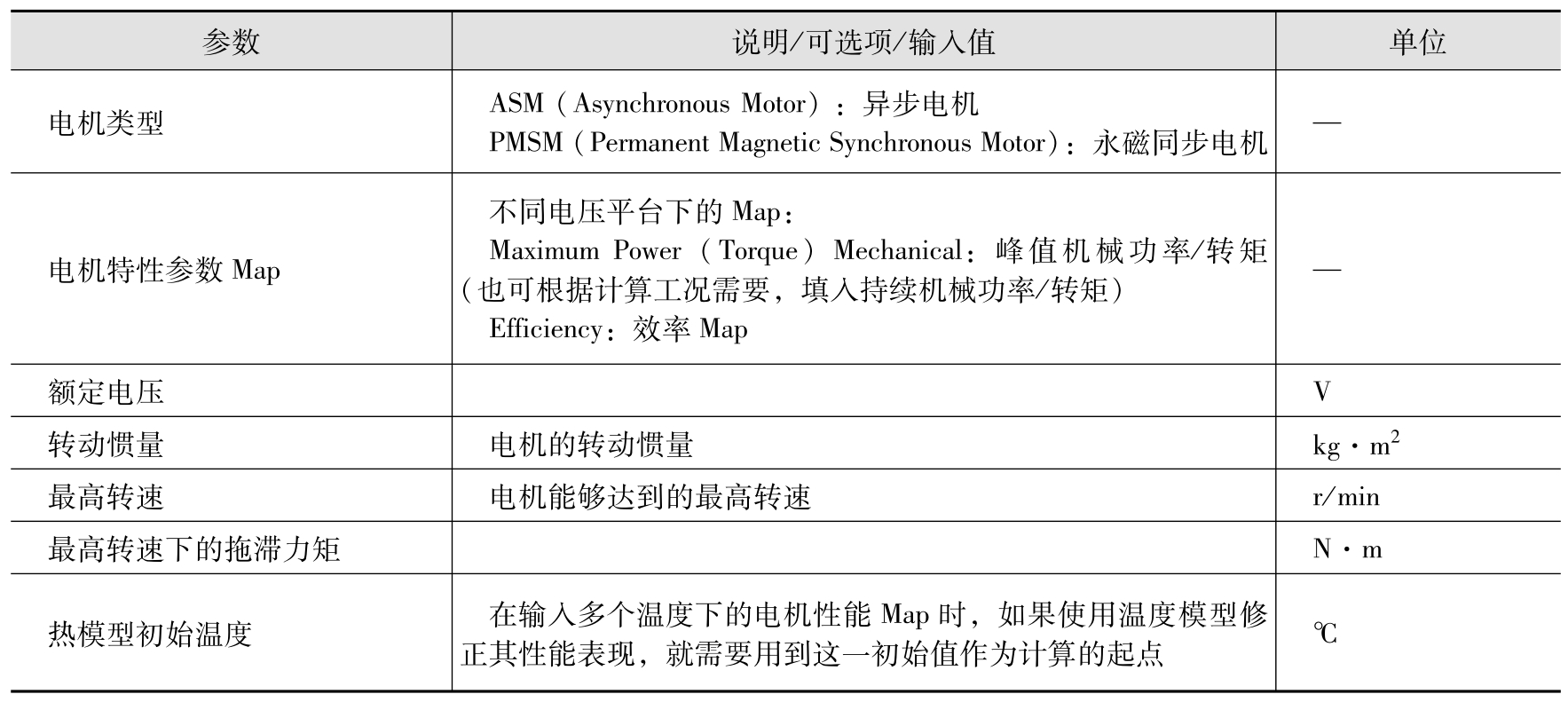
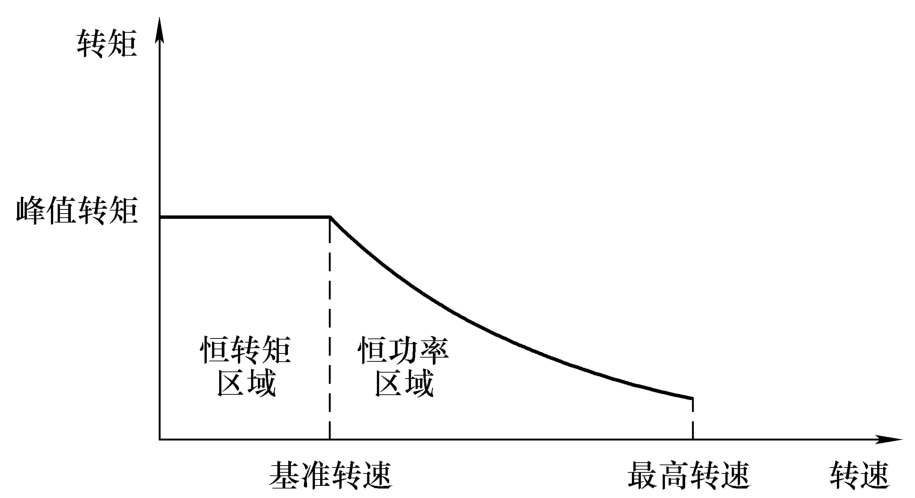
图1-30 电机的理想输出特性曲线
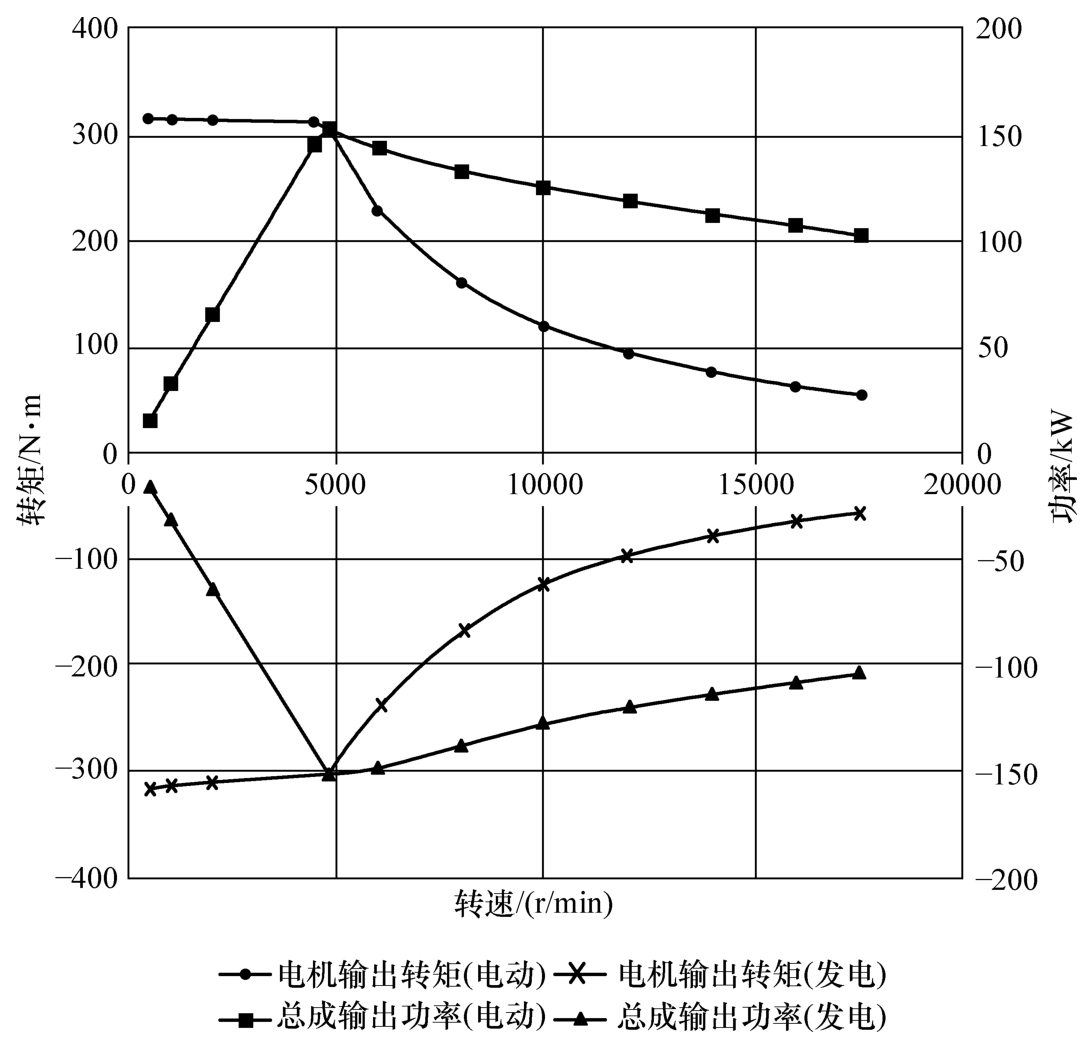
图1-31 某电机实际峰值外特性曲线
4)效率曲线。电机的效率曲线如图1-32所示。
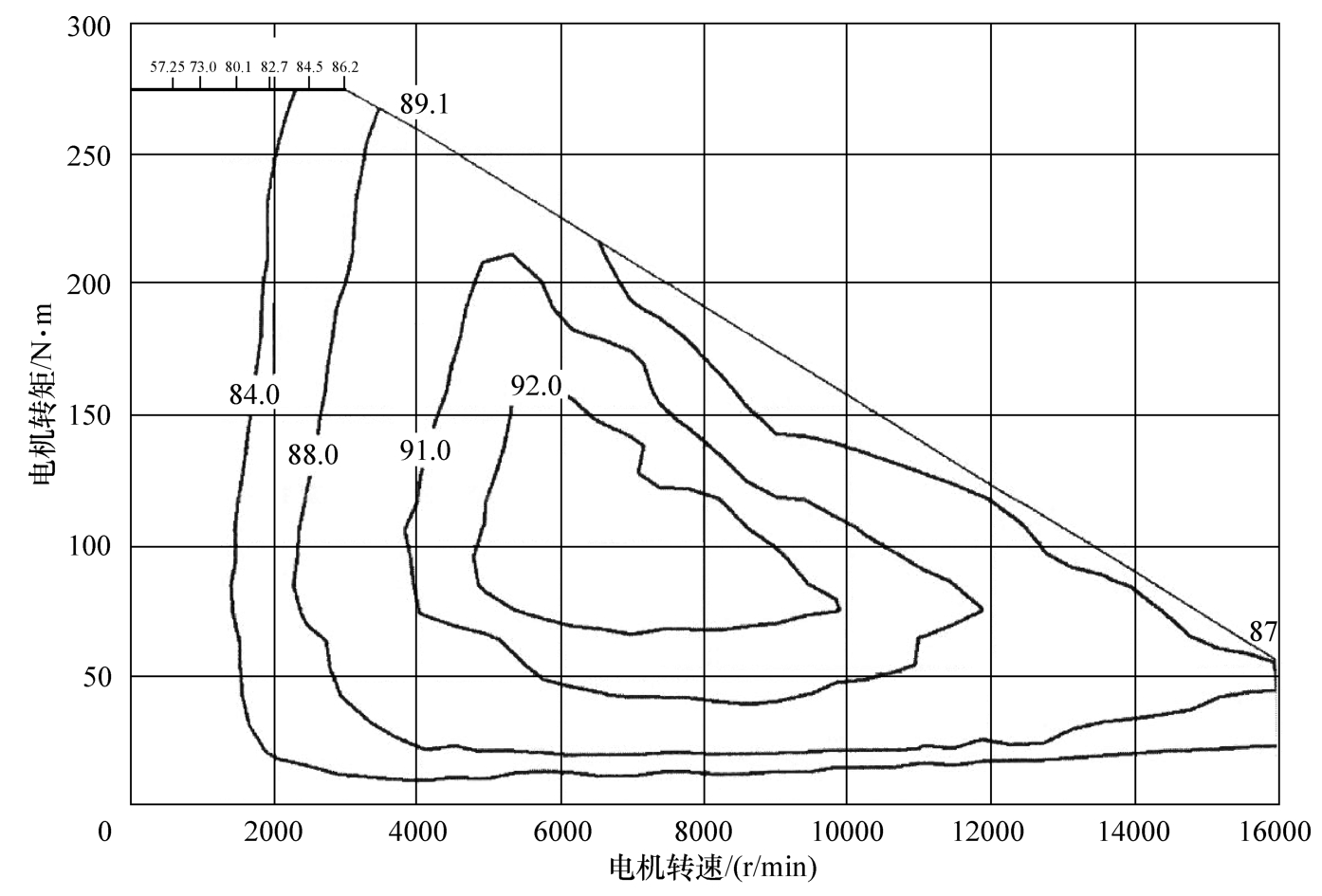
图1-32 电机的效率曲线
1.2.6 传动系统性能设计
传动系统用于确保驱动单元的实际运行特性尽可能地靠近理想运行特性。以下分析离合器、液力变矩器、变速器和主减速器等传统系统元件的性能设计。
1.离合器性能设计
基于动力性进行离合器的设计时主要考虑离合器的最大传递转矩的能力。当外部施加的转矩超过最大传递转矩的能力时,离合器会打滑。因此一般在设计离合器时,要求其传递的最大转矩大于或等于内燃机转矩。离合器最大传递转矩能力的计算如图1-33所示。
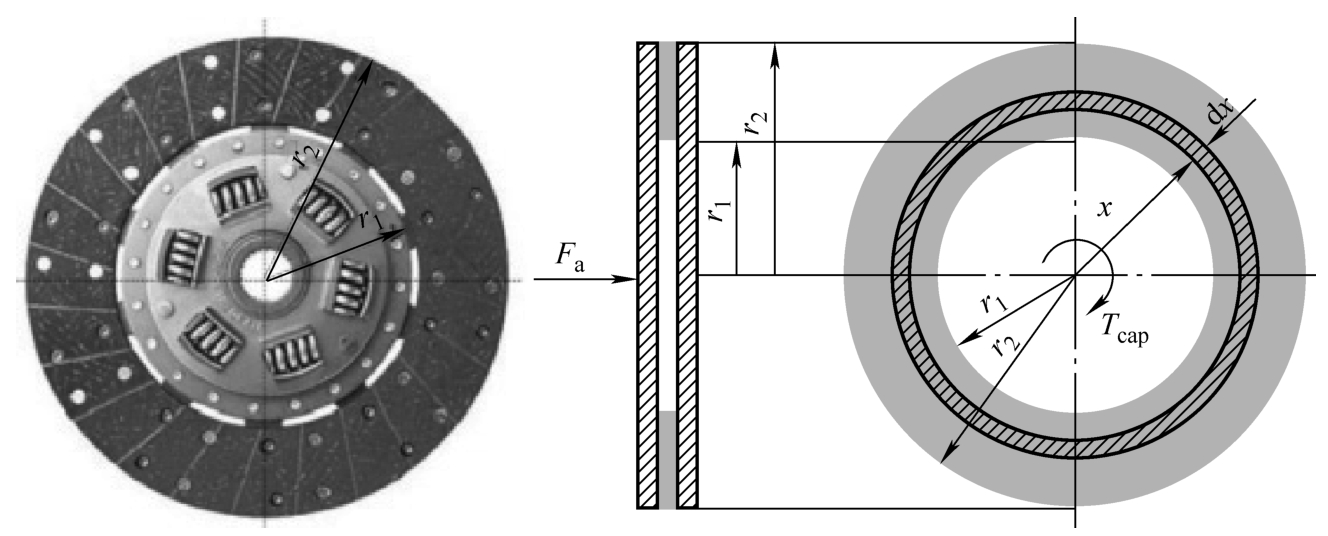
图1-33 离合器最大传递转矩能力的计算
离合器最大传递转矩的计算公式如下:

式中 T cap ——离合器最大传递转矩(N·m);
z ——离合器盘片数;
μ ——摩擦系数;
r 1 ——离合器摩擦片内径(mm);
r 2 ——离合器摩擦片外径(mm);
F a ——离合器盘片所受正压力。
2.液力变矩器性能设计
液力变矩器选型中,为满足整车性能要求,对其提出表1-10所列的一般要求。这些要求有时是相互矛盾的,这就为平衡设计要求提供了空间。
表1-10 液力变矩器的一般要求
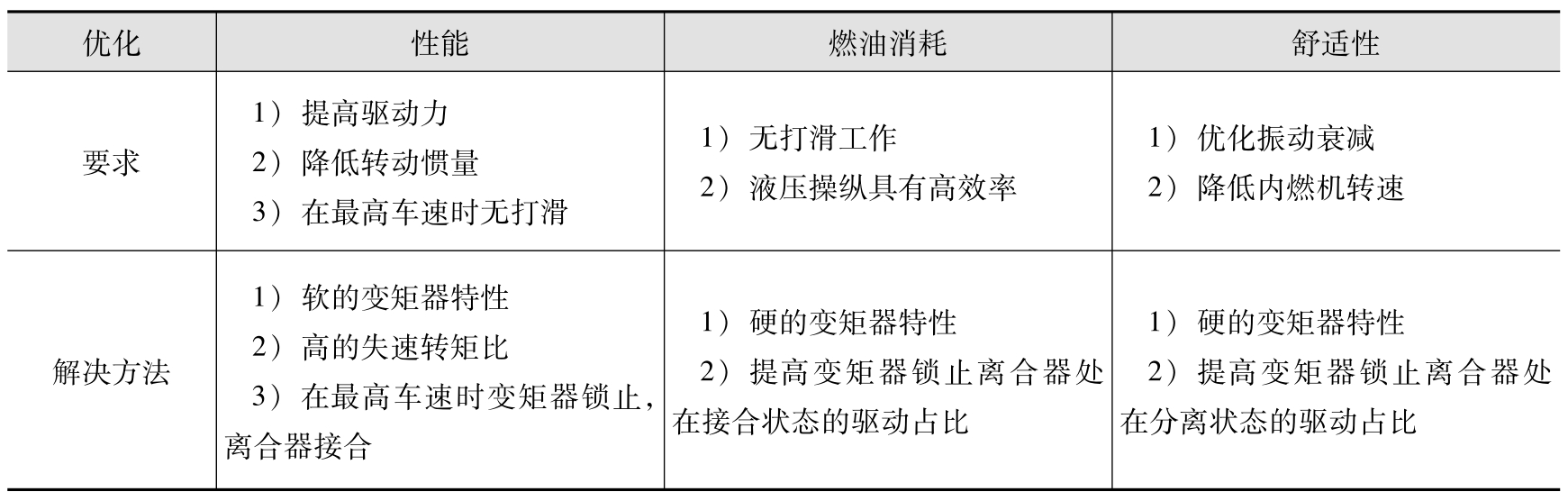
(1)基本参数 液力变矩器的运行特性是选型工作最重要及最先用到的参数,其对于液力变矩器选型工作有很大的影响。
液力变矩器的运行特性可通过以下四个参数来描述:
转速比 i :

转矩比 K :

效率 η :

容量系数(尺寸因数) K tc :
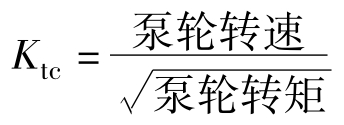
典型液力变矩器的运行特性如图1-34所示。图中描绘了转矩比、效率和输入端容量系数相对于转速比的关系。
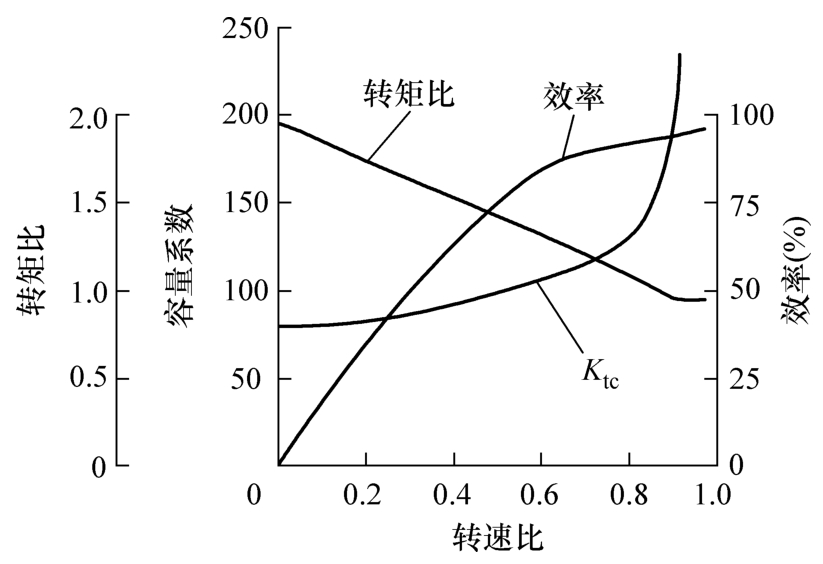
图1-34 典型液力变矩器的运行特性
(2)液力变矩器模型的构建 液力变矩器通过液体路径和机械离合器路径将驱动单元的转矩传递给变速器。这两条路径是并联的。液体路径中,液力变矩器的作用类似于液力耦合器,使驱动单元不受轮边转矩通过传动链传递至涡轮输出轴上的转矩的影响而独立转动,这也是自动变速器提高了驾驶舒适性的一大原因。
液力变矩器的工作原理图如图1-35所示。
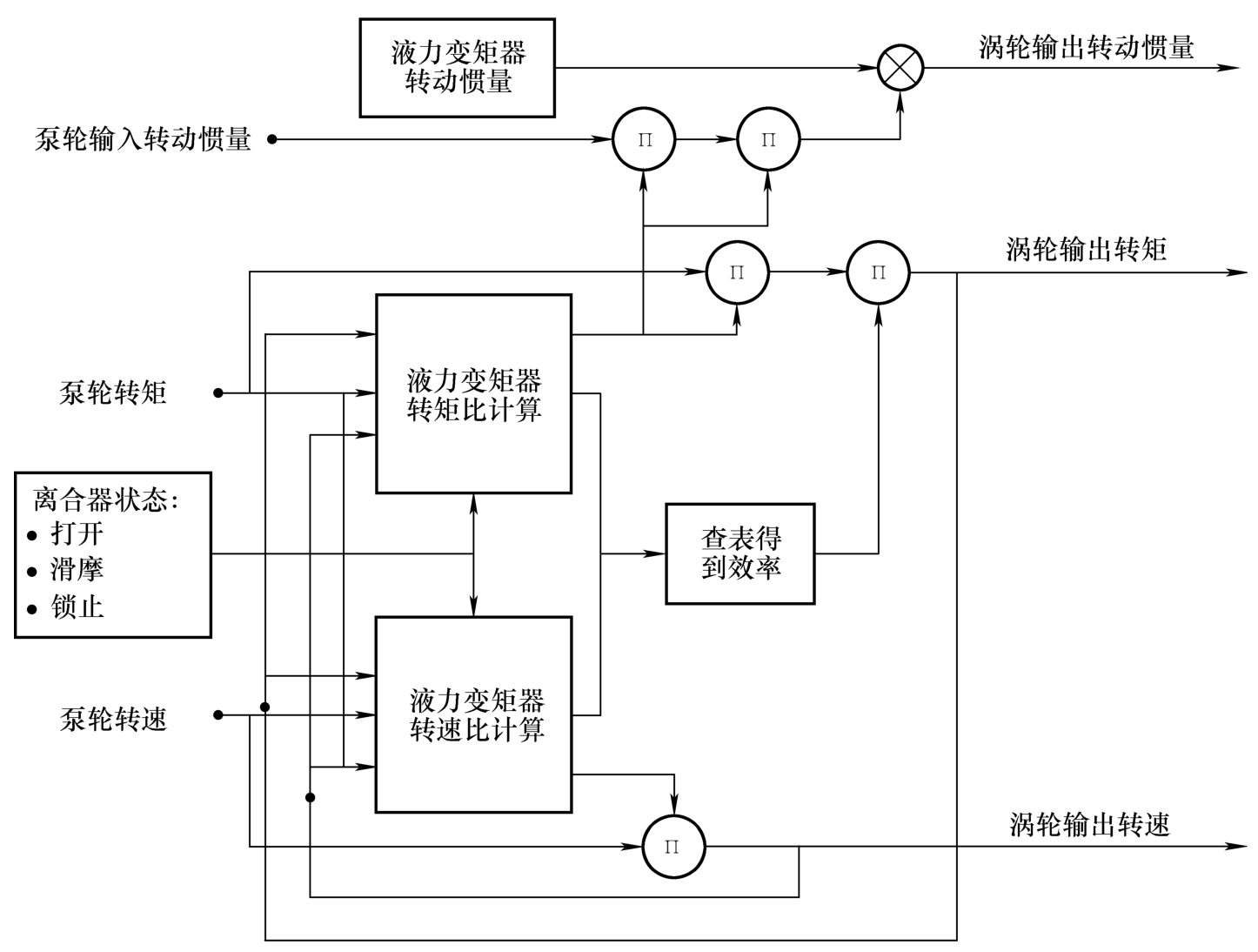
图1-35 液力变矩器的工作原理图
(3)液力变矩器的工作状态 液力变矩器根据其离合器的状态,分为以下三种工作状态:
1)打开。离合器完全分离,泵轮转矩通过液压油传动传递到涡轮,涡轮与变速器输入轴刚性连接,故而转矩被传递到变速器。泵轮与涡轮存在较大的转速差,转速比和转矩比通过查表得到。
2)滑摩。离合器处于半离合状态,内燃机转矩部分通过离合器传递到变速器。泵轮与涡轮存在较小的转速差,转速比和转矩比通过查表得到。
3)锁止。离合器完全锁止,此时泵轮与涡轮之间的转速差很小(一般≤20r/min),同时内燃机转矩通过离合器直接传递到变速器输入轴。转速比和转矩比均为1,此时自动变速器的功能类似于手动变速器。
(4)基本参数 AVL Cruise进行仿真计算时需用到的液力变矩器特性参数见表1-11,其中 T p2000 为在台架试验中,泵轮试验转速为2000r/min下测得的泵轮转矩。
表1-11 液力变矩器特性参数

(续)
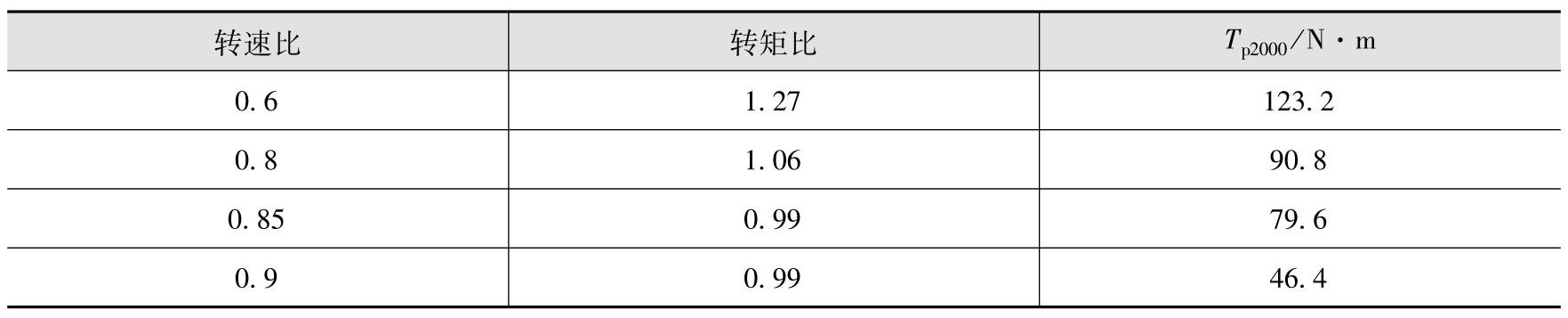
3.变速器与主减速器性能设计
变速器和主减速器均为齿轮系(主减速器可以看成是只有一对齿轮的单档变速器),对于前轮驱动车型而言,主减速器一般集成在变速器中。本书以前轮驱动车型为例,后文中若无特殊说明,所称变速器均包含了主减速器。
变速器和主减速器的设计要点均在于传动比和传动效率。无论是手动变速器(MT)还是自动变速器(AMT/AT/DCT/CVT),均拥有若干套齿轮用于传递驱动单元的转矩。变速器的作用是将驱动单元的输出特性尽可能转化为理想的输出特性。
(1)传动比的设计
1)最小传动比的选择。最小传动比的选择对于汽车的最高车速、后备功率和驾驶性能有很大的影响。下面以最高车速目标来定义最小传动比。
传动系统的总传动比是传动系统中各部件传动比的乘积,即

式中 i g ——变速器的传动比;
i 0 ——主减速器的传动比;
i c ——分动器或副变速器的传动比。
理论上, i g i 0 i c 选择到汽车的最高车速 u max 相当于内燃机最大功率点的车速 u p 时,最高车速是最大的,即

此时汽车达到功率平衡,即

式中 P max ——汽车最高车速时的内燃机功率(kW);
P r ——汽车的阻力功率(kW)。
近年来,为了提高燃油经济性,最小传动比有减小的趋势,即令 u p 稍大于 u max 。
这里为简化计算,可定义 i g =1、 i c =1(无分动器),则此问题变成选择最优的主减速器传动比 i 0 。
在选定主减速器传动比 i 0 后,可采用AVL Cruise的Matrix Calculation计算功能,分别以 i g 、 i c 值为单变量变化计算得到满足最高车速目标的 i g 、 i c 值。这两个值作为变速器选型的参考依据之一。
2)最大传动比的选择。最大传动比的选择对于汽车的最大爬坡度、附着率及汽车最低稳定车速有很大的影响。下面以最大爬坡度目标来定义最大传动比。
汽车爬坡时,汽车的最大驱动力与阻力平衡时,爬坡度是最大的,此时

即

则

式中 F c ——滑行阻力(N),通过滑行试验测得,这里考虑车速为20km/h时的滑行阻力;
m ——满载质量(kg);
i max ——最大爬坡度(%);
T m ——内燃机最大转矩(N·m)。
3)变速器档位数和各档传动比的选择。虽然增加档位数会改善汽车的动力性和经济性,但是对于手动变速器来说,档位数不宜过多,否则会导致结构复杂,换档困难。一般多采用5MT和6MT。自动变速器因为有自动变速器控制单元(TCU)控制换档,不需要驾驶人手动操作,故而目前的趋势是档位数越来越多,如8AT、9AT,甚至是10AT。
变速器中间档位传动比通过各档传动比来确定,它们可保证内燃机在汽车的加速过程中拥有最大的加速强度和最短的加速时间,同时还需兼顾经济性。一般有以下两种确定的方法:
① 等比级数法。等比级数的传动比比较适合于常行驶于良好路面且比功率较大的汽车。其缺点是高档利用率低,平均加速速度较低,油耗增加。
等比级数的传动比如下:

式中 i g1 、 i g2 、 i g3 …——各档传动比;
q ——常数。
最大、最小传动比已经确定,故可按以下公式计算等比级数的传动比 q g :

式中 n ——变速器档位数;
i g1 ——变速器最大传动比;
i g n ——变速器最小传动比。
② 等差级数法。等差级数的传动比比较适合于常行驶于恶劣环境且比功率较低的汽车。
最大、最小传动比已经确定,故可按以下公式计算等差级数的传动比 q a :

式中 n ——变速器档位数;
i g1 ——变速器最大传动比;
i g n ——变速器最小传动比。
上述两种方法均基于理想的加速过程,实际的加速过程更复杂,汽车变速器中间档位的实际传动比处于等比级数值和等差级数值之间,且偏向于等比级数值。故可在确定等比级数的传动比之后,按以下公式修正:

式中 λ ——修正系数,一般在0.90~0.98之间:比功率低,且常行驶于坏路的车辆,应取下限;比功率高,且常行驶于良好路面的车辆应取上限。
以修正系数为单变量(在0.90~0.98之间,步长为0.01),变化生成9种变速器,利用AVL Cruise的Component Calculation计算功能,得到G1~G9这9种变速器的动力性和经济性仿真数据,从中选出最优方案。
(2)变速器模型的构建
1)变速器的工作状态。变速器根据其齿轮系的转动方向,可以分为正转和反转两种工作状态。
① 正转。前进档位齿轮啮合,变速器将驱动单元的转矩传递到传动轴并最终输出到轮边。
② 反转。后退档位齿轮啮合,变速器将驱动单元的转矩传递到传动轴并最终输出到轮边。
上述两种工作状态,要求主减速器既能正转,也能反转。在校核其承扭能力时,要注意这两种工作状态下的差异。
2)变速器的工作原理。以自动变速器为例,其工作原理图如图1-36所示。
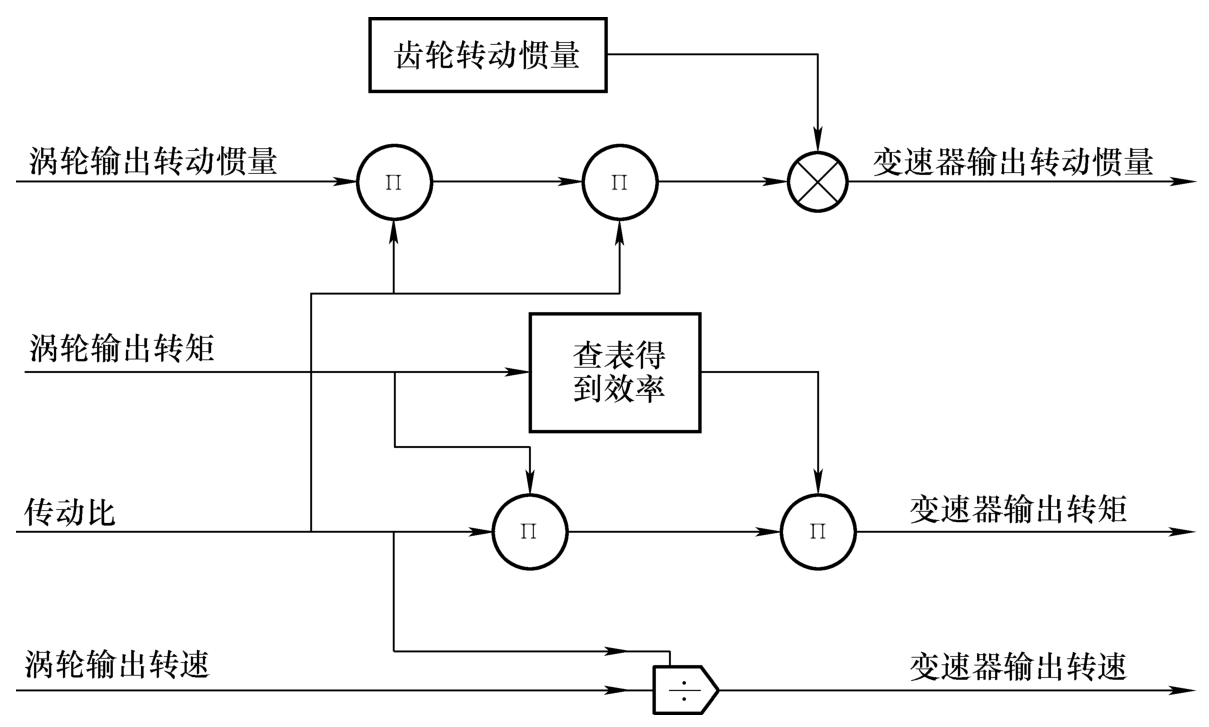
图1-36 变速器的工作原理图
1.2.7 储能系统性能设计
自然界中能够直接被人类转换和利用的能源称为一次能源。能量以化学能、热能、动能或者其他形式储存在一次能源中。经过一次或多次的能量转换的能源被称为二次能源。对于二次能源,一般要求转换效率尽可能高,便于储存和运输。常见的二次能源储能系统有动力蓄电池和储氢系统。本书主要介绍动力蓄电池。
1.动力蓄电池类别及基本原理
常见电池有铅酸电池、镍镉电池、镍氢电池、锂离子电池、磷酸铁锂电池等。这些电池具有表1-12所列的基本技术参数。
表1-12 各类型电池的基本技术参数
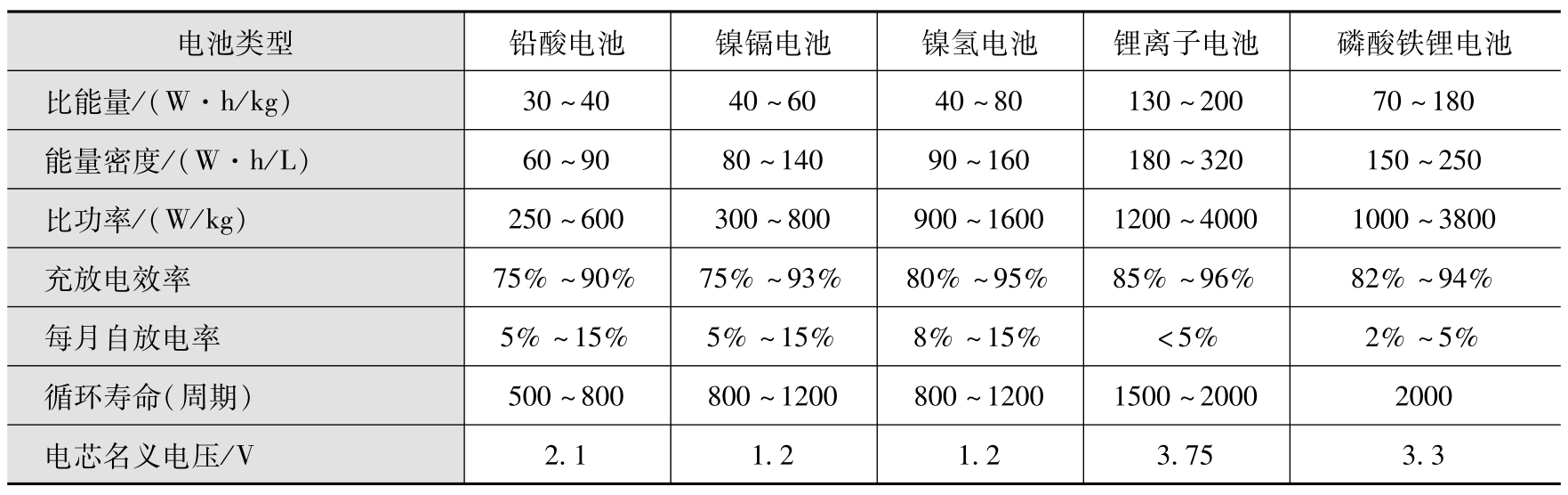
其中以锂离子电池在汽车行业中应用最广泛。锂离子电池具有一定的相似性,但是化学性质可以有很大的不同。锂钴、锂锰、锂镍锰氧化物和锂铝的相似之处在于它们具有高容量,可用于便携式应用。磷酸锂和钛酸锂具有较低的电压和较小的容量,但是非常耐用。表1-13列出了各种主要锂离子电池的特性。
表1-13 各种主要锂离子电池的特性
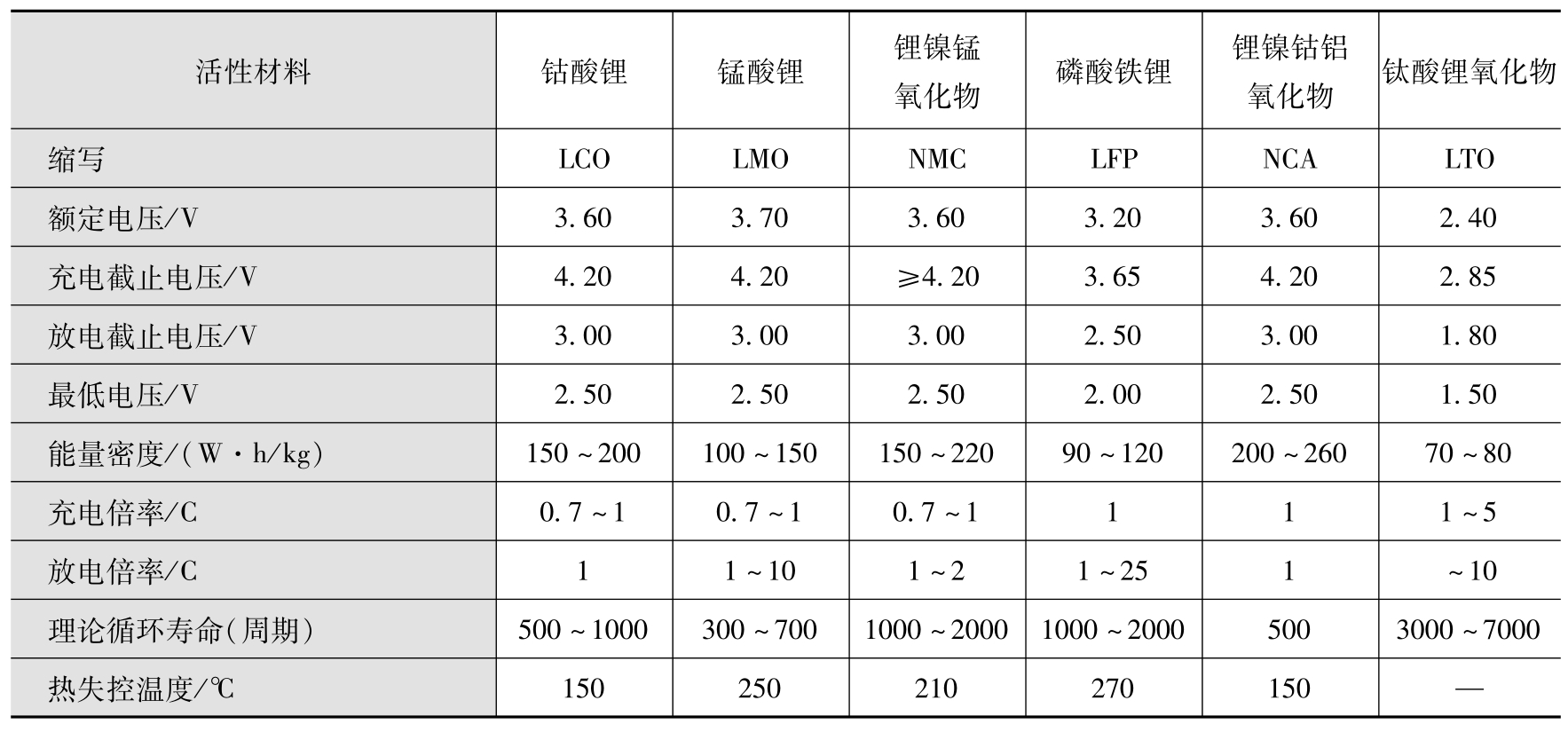
动力蓄电池系统由很多电芯组成,根据车辆的电压平台、功率和能量的要求,可通过串联、并联或者串并联混合的形式封装成电池组。
电池电芯的电化学反应示意图如图1-37所示。
2.动力蓄电池仿真模型构建
通常用电池等效电路模型来表征电池端电压和电流之间的关系,这是进行电池关键参数设计的基础。应用最广泛的等效电路模型为戴维南模型,如图1-38所示。
电池的输出参数主要有端电压、荷电状态(SOC)和热功率。戴维南模型假定所有参数均为定值,这显然是不正确的,也不足以支撑性能仿真,需要进一步明确电池的输入-输出特性,因此应建立改进的电池电学模型,如图1-39所示。
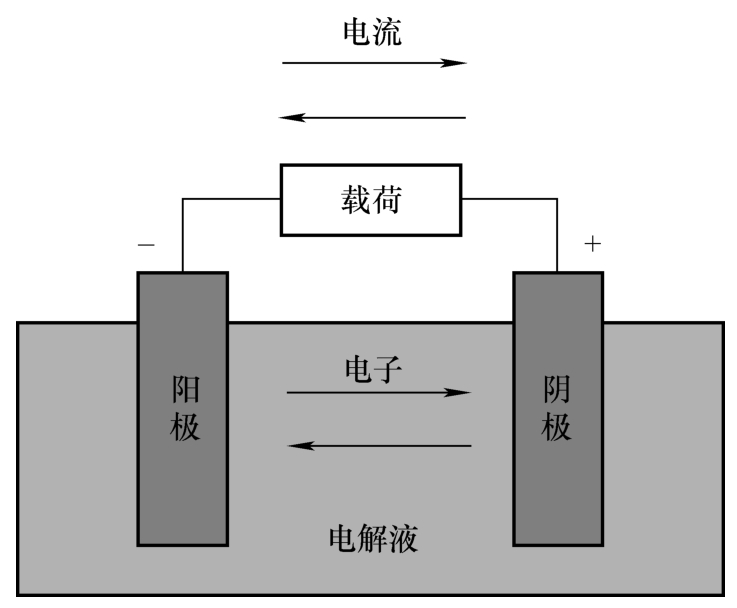
图1-37 电池电芯的电化学反应示意图
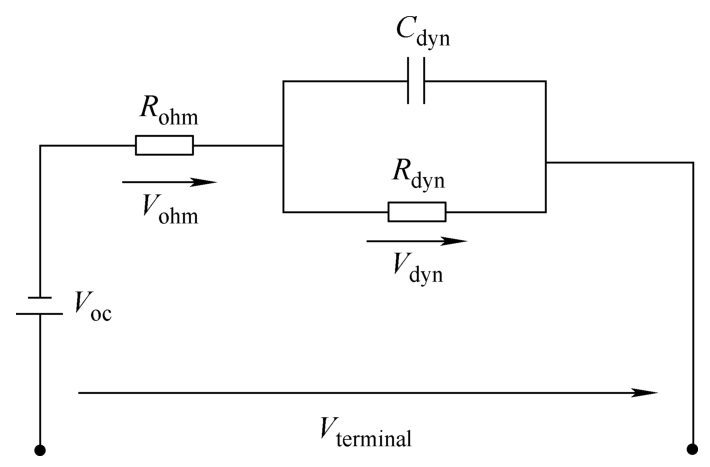
图1-38 戴维南模型
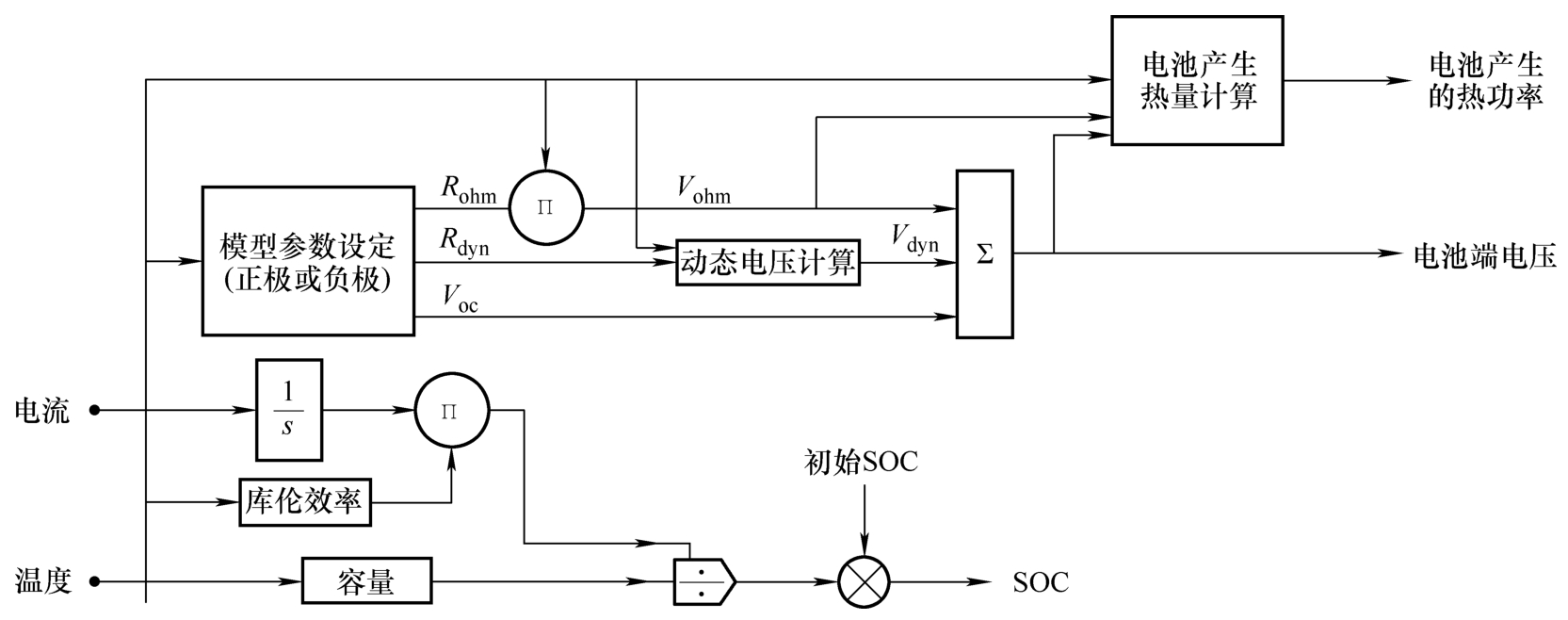
图1-39 改进的电池电学模型
1)基本参数。在进行动力蓄电池系统的匹配分析中,需要用到的关键基本参数见表1-14(若无特殊说明,均指电池组的参数)。
表1-14 动力蓄电池关键基本参数
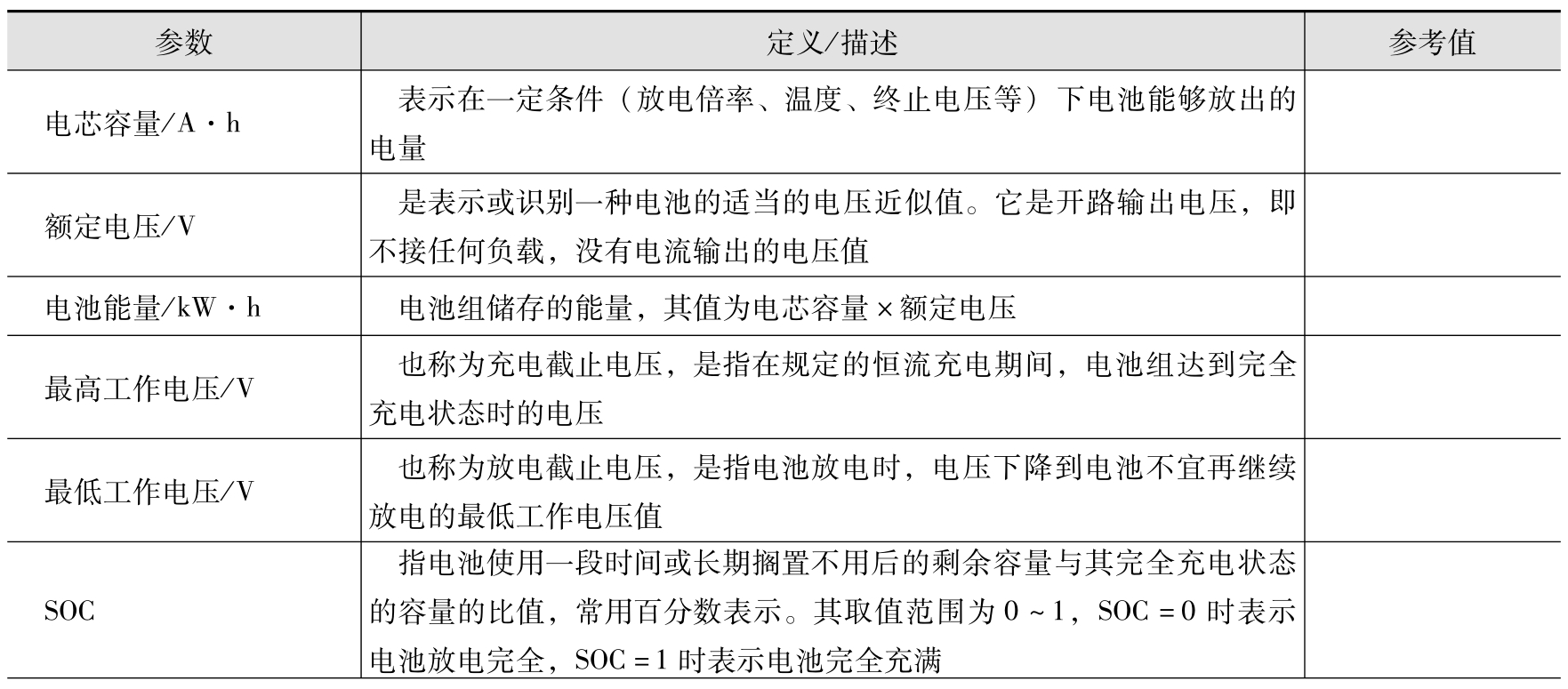
(续)
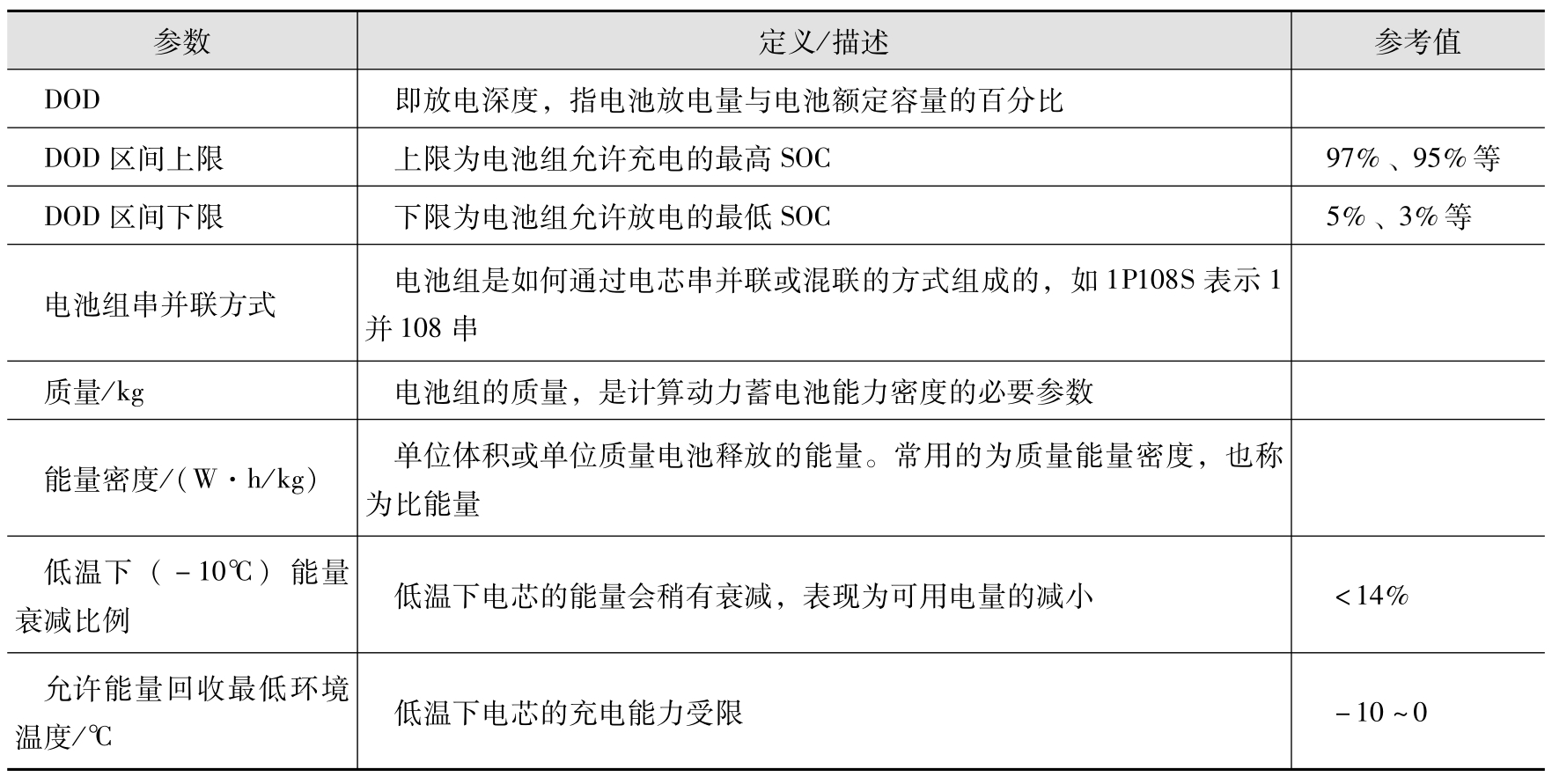
2)电学特性参数。通常可以通过试验(如混合脉冲特性试验)数据来对电池等效电路模型的参数进行离线标定。进行混合脉冲特性试验是为了设计动力蓄电池在2s或10s的短时间内、不同的SOC下和不同的工作温度下的充放电能力。同时,通过该试验还可以获得众多电池的电路模型参数。
混合脉冲特性的试验原理图如图1-40所示。
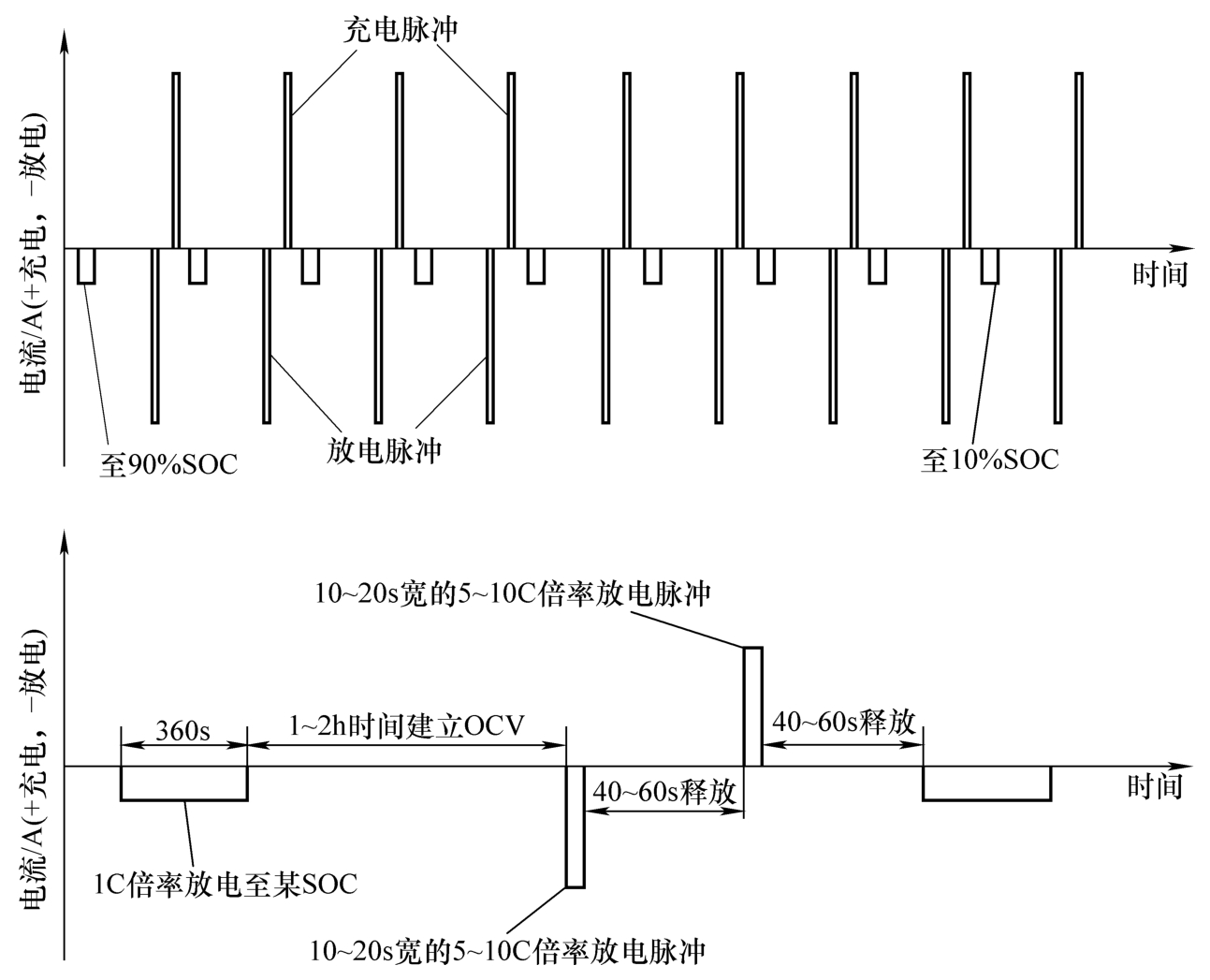
图1-40 混合脉冲特性试验原理图
根据电池等效电路,电池端电压和电流的关系可以由如下计算式表示:
端电压为

开路电压为

欧姆电阻器电压为

动态电流为
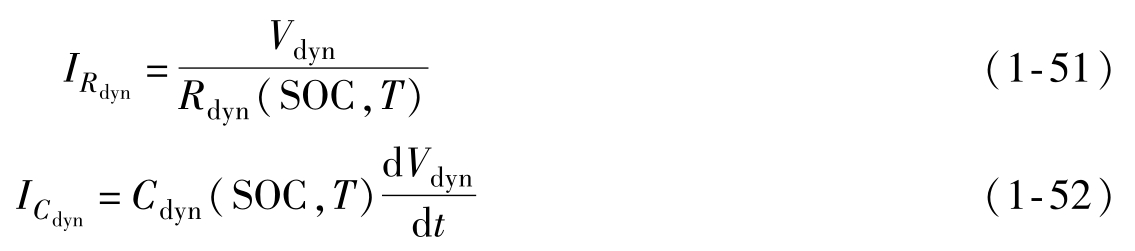
综上所述,动态电压可以用以下微分方程表示:

则电路的总微分方程为

式中 I terminal ——电池系统端电流(A);
V terminal ——电池系统端电压(V);
T ——电池温度(℃);
V oc 、 R ohm 、 R dyn 、 C dyn ——电路模型参数,均为关于电池温度和SOC的函数,通过混合脉冲特性试验结果计算得到。
3)SOC的估算。在动力蓄电池的应用中,SOC是汽车动力性和经济性的重要影响因素,同时通过仪表显示剩余的电量和预测的剩余行驶里程,也可给驾驶人一个重要的判断依据(判断何时需要给汽车充电、当前状态下车辆可供行驶的剩余里程)。但是因多种因素,SOC的计算误差偏大,因此结合多种方法合并测定SOC就具有很大的必要性。一般以电池的电压、电流、温度、使用状态、使用时间等因素来估算SOC。
常用的SOC估算方法见表1-15。
表1-15 常用的SOC估算方法
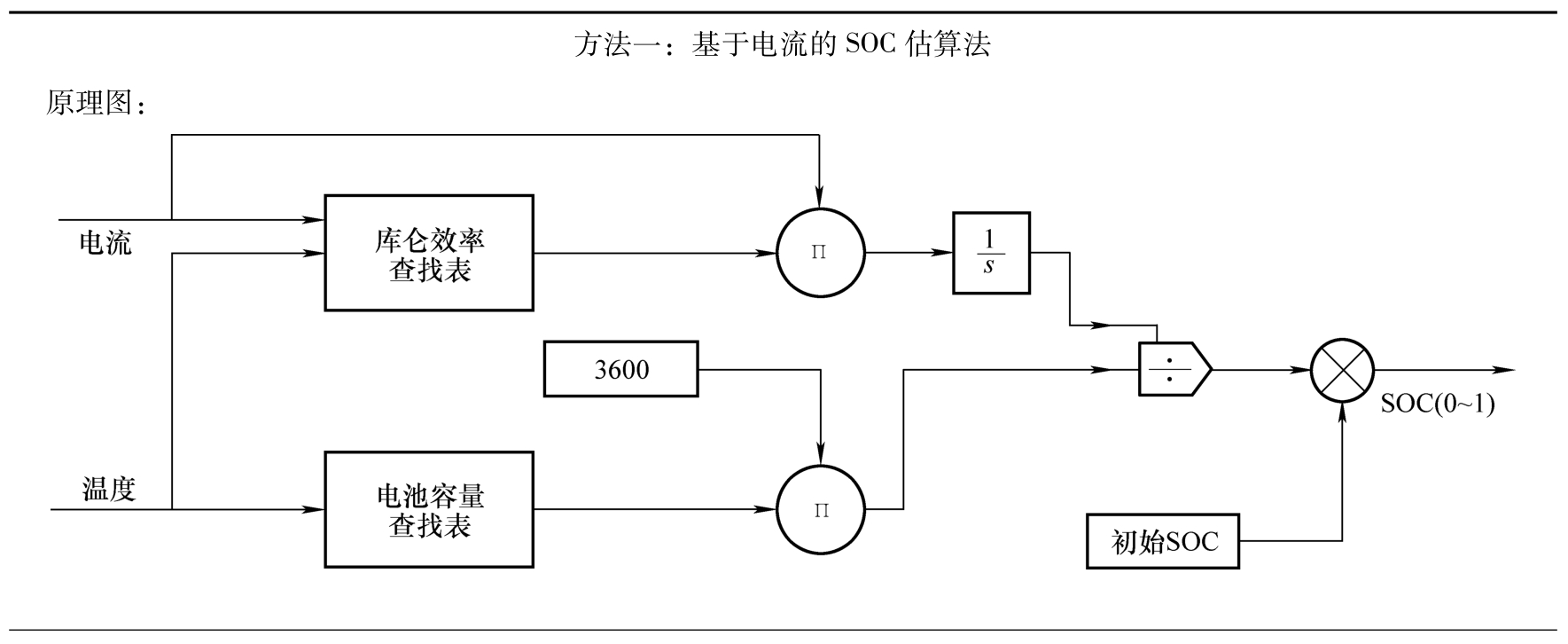
(续)
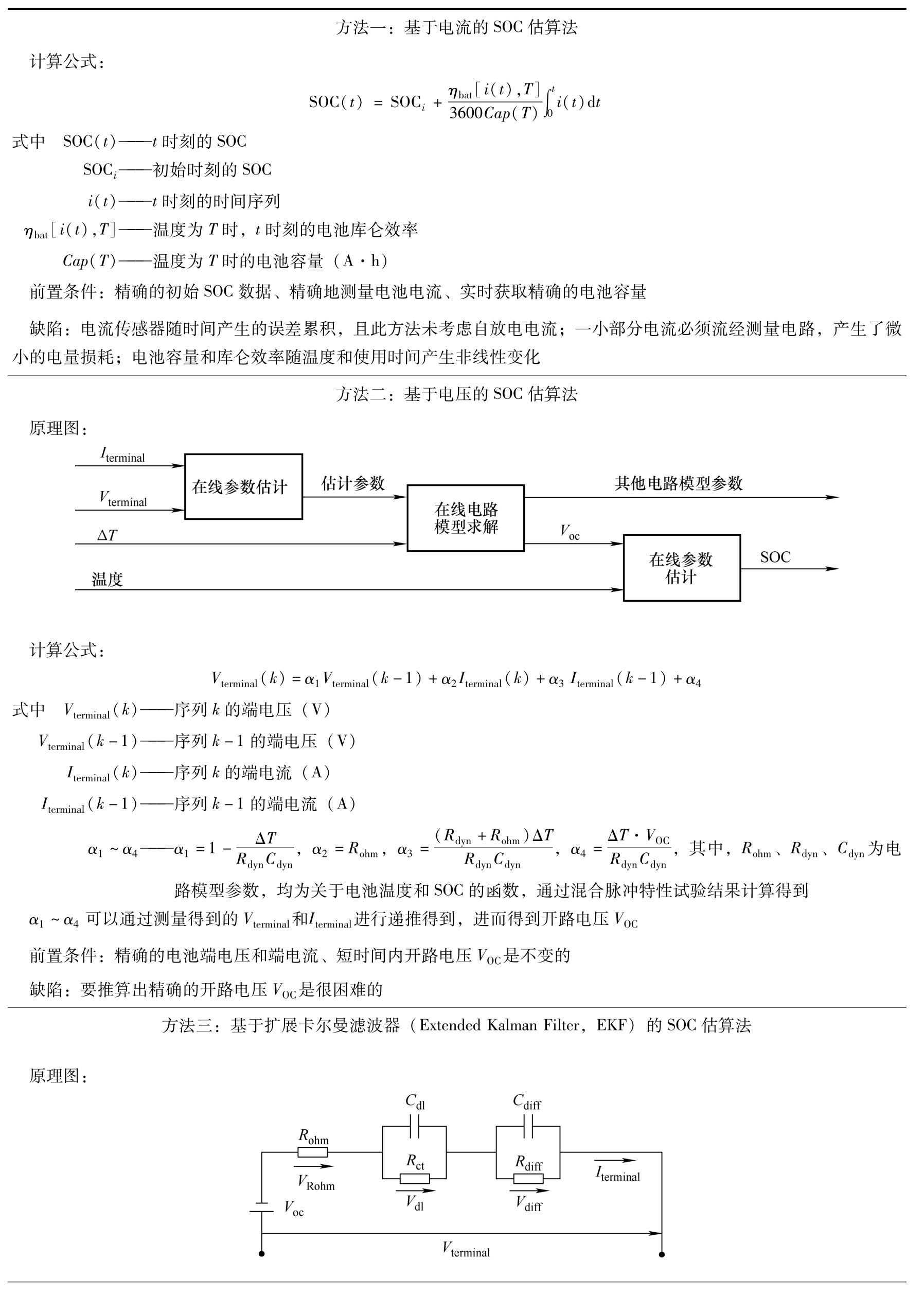
(续)
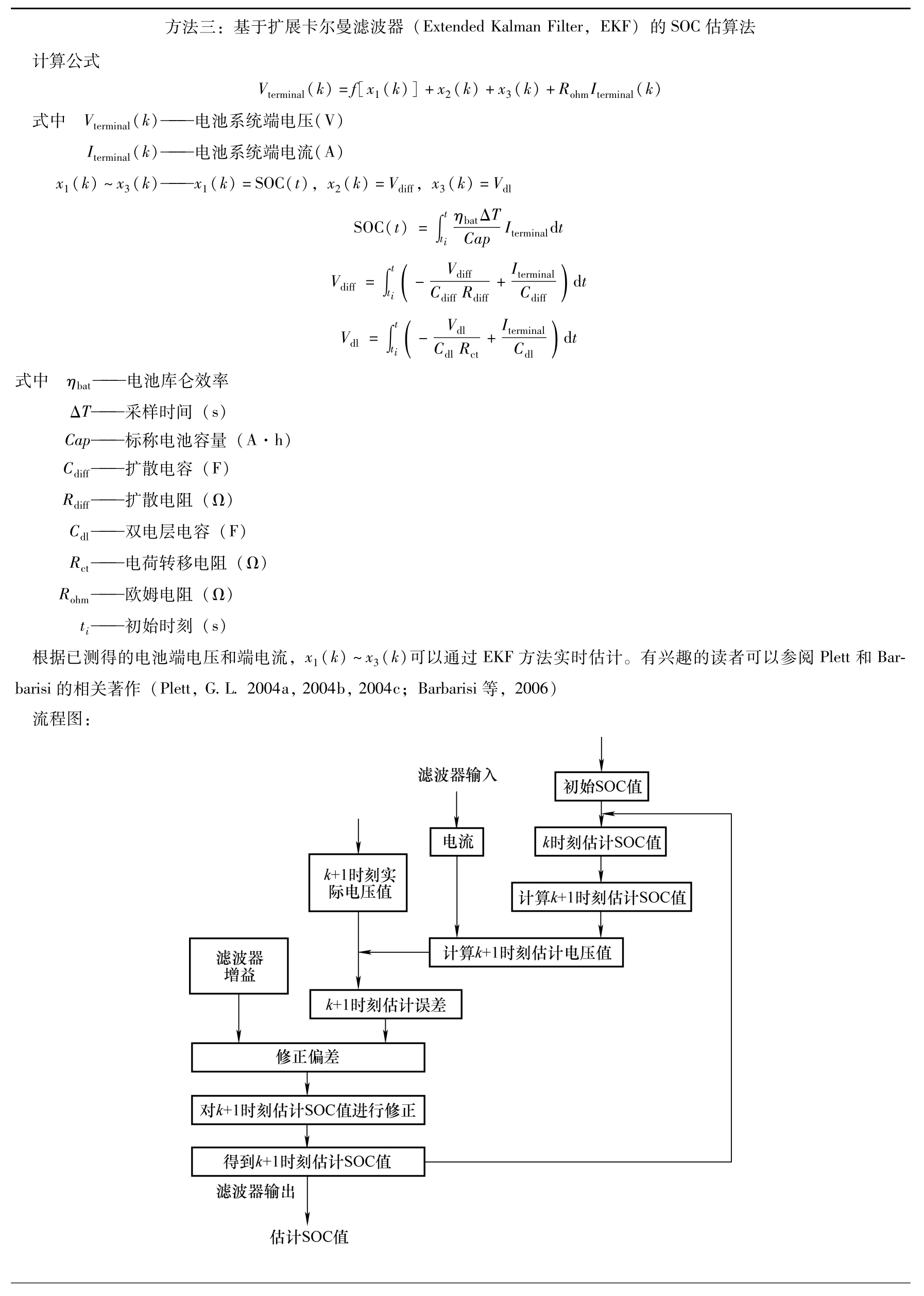
(续)
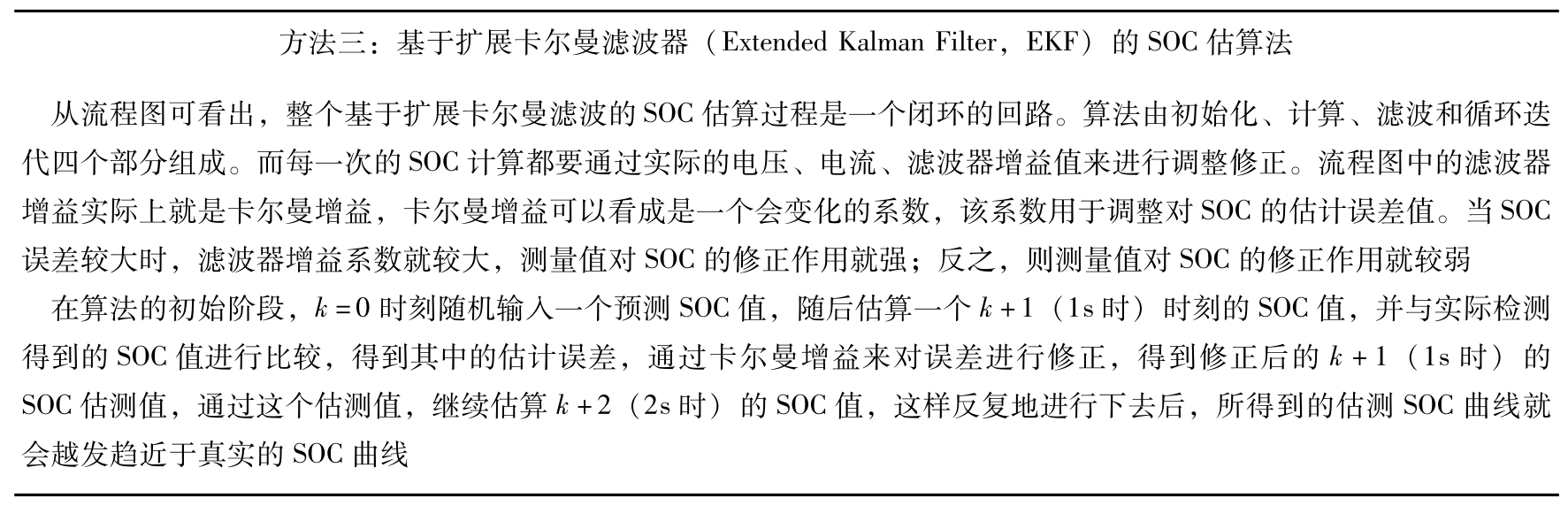
3.动力蓄电池特性曲线
采用AVL Cruise进行车辆动力性仿真分析,一般要用到以下动力蓄电池特性曲线:OCV-SOC曲线、Ohm-SOC曲线、Power Map。
1)开路电压-荷电状态(OCV-SOC)曲线。OCV-SOC曲线是电池在SOC标定过程中非常重要的一条曲线,通常在电动汽车运行了一段时间后,在车辆静置再起动前,电池管理系统(BMS)会调用该曲线,对SOC值进行一次校正,并通过一定的算法和其他校正系数得到一个SOC值的更新。因此该曲线的准确性就显得尤为重要,可能直接影响SOC的精度。典型的OCV-SOC曲线如图1-41所示。
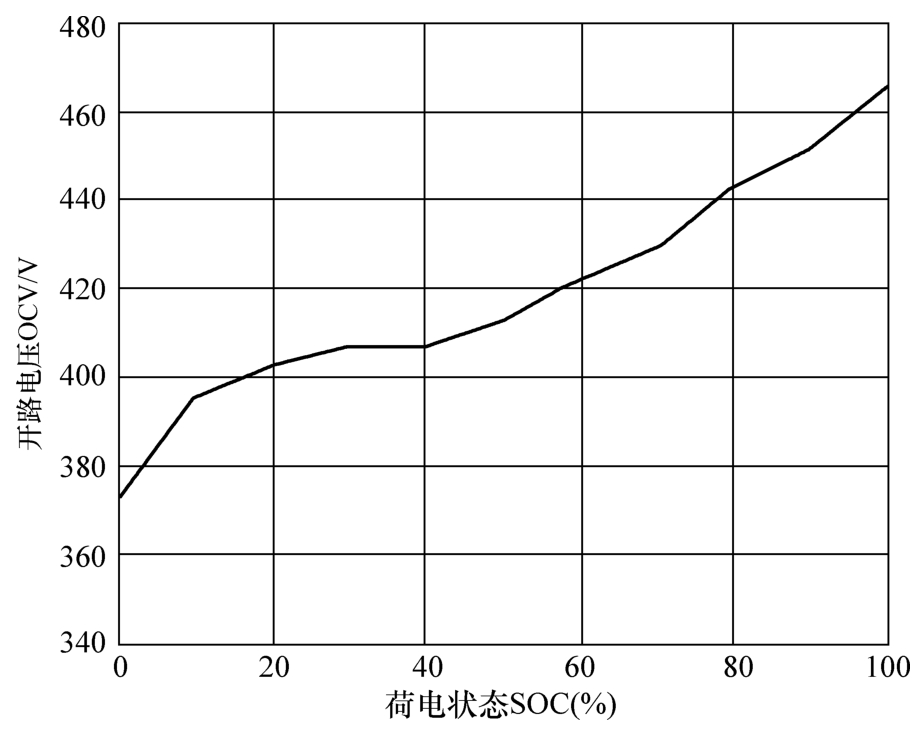
图1-41 典型的OCV-SOC曲线
2)内阻-荷电状态(Ohm-SOC)曲线。对锂离子电池而言,电池内阻分为欧姆内阻和极化内阻。欧姆内阻由电极材料、电解液、隔膜电阻及各部分零件的接触电阻组成。极化内阻是指电化学反应时由极化引起的电阻,包括电化学极极化和浓差极化引起的电阻。典型的Ohm-SOC曲线(即电池内阻)如图1-42所示。
3)功率图(Power Map)。动力蓄电池的Power Map代表了其在不同环境温度、不同SOC下能够输出的功率,这决定了电动汽车在确保必要的用电器能够正常工作的前提下,使电机获得尽可能大的电功率,并转换为机械功率,最终输出到整车上以获得动力性。典型的Power Map如图1-43和图1-44所示。
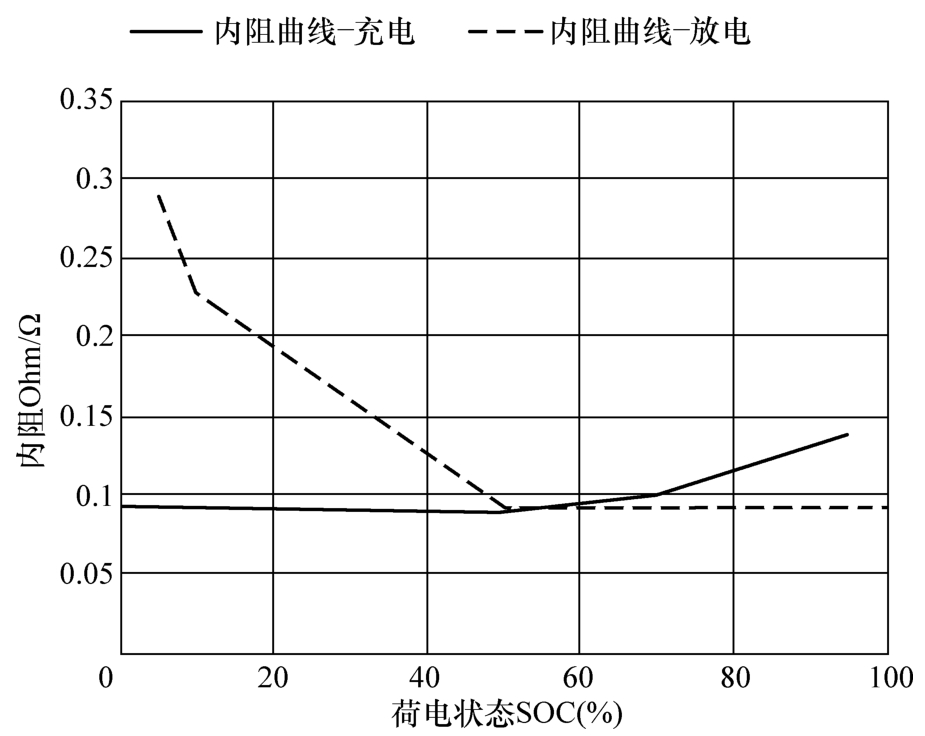
图1-42 典型的Ohm-SOC曲线
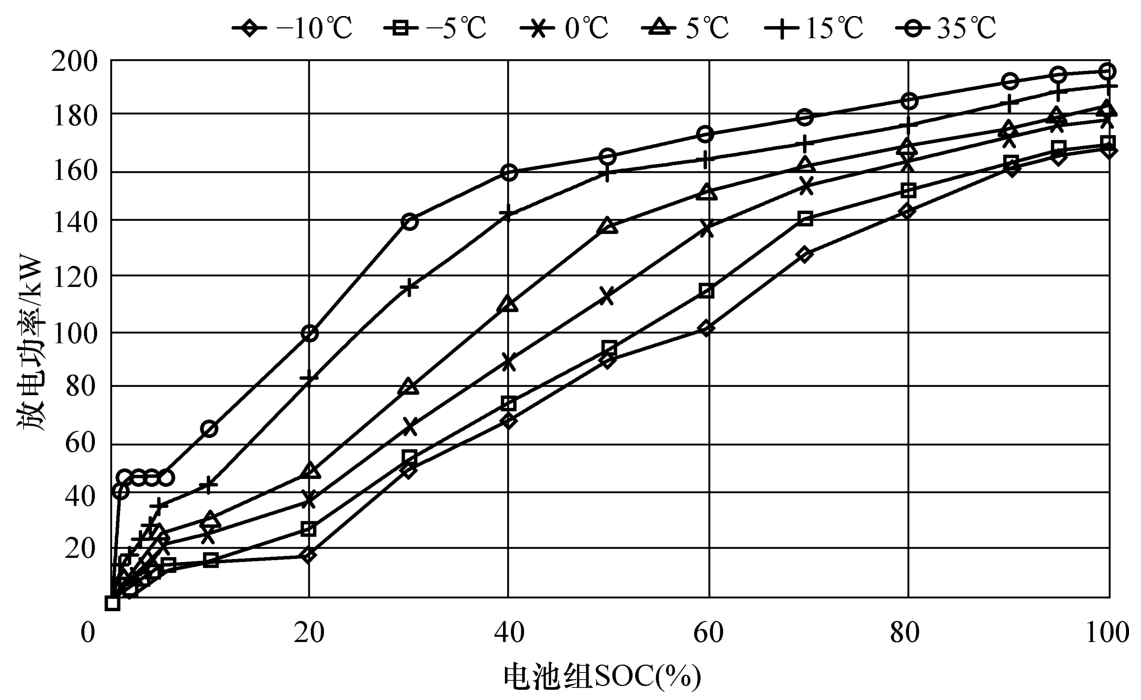
图1-43 某电池组不同温度放电功率(60s)
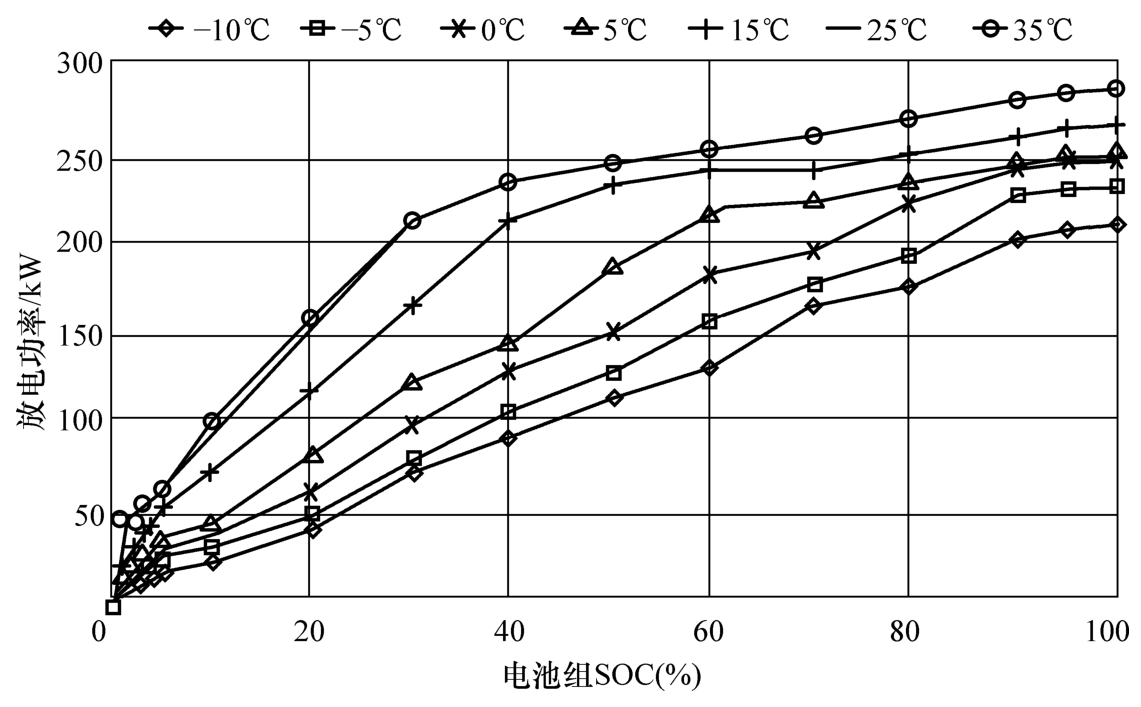
图1-44 某电池组不同温度放电功率(10s)
1.2.8 高压电系统性能设计
1.冲放电过程中的功率平衡
(1)高压线束的限制 在进行电动汽车车型设计时,需考虑以下用电/充电设备的高压线束设计:动力蓄电池的母线、电机的母线和直流(DC)充电高压线束。
高压线束的线径限制了其能够传递的电流,一般汽车用高压线束载流量见表1-16。
表1-16 汽车常用高压线束载流量限制

(2)高压用电器的功率平衡 所有高压用电器的能量均来源于动力蓄电池,为了保证所有用电器能够正常工作,要求动力蓄电池的输出功率(峰值和持续)应大于或等于所有用电器的工作功率之和(峰值和持续)。在给定的电压平台下,动力蓄电池的输出功率主要受高压线束的限制。故而在选取高压线束的线径时,要考虑车辆的动力性要求。图1-45所示为某电动汽车的功率平衡图。
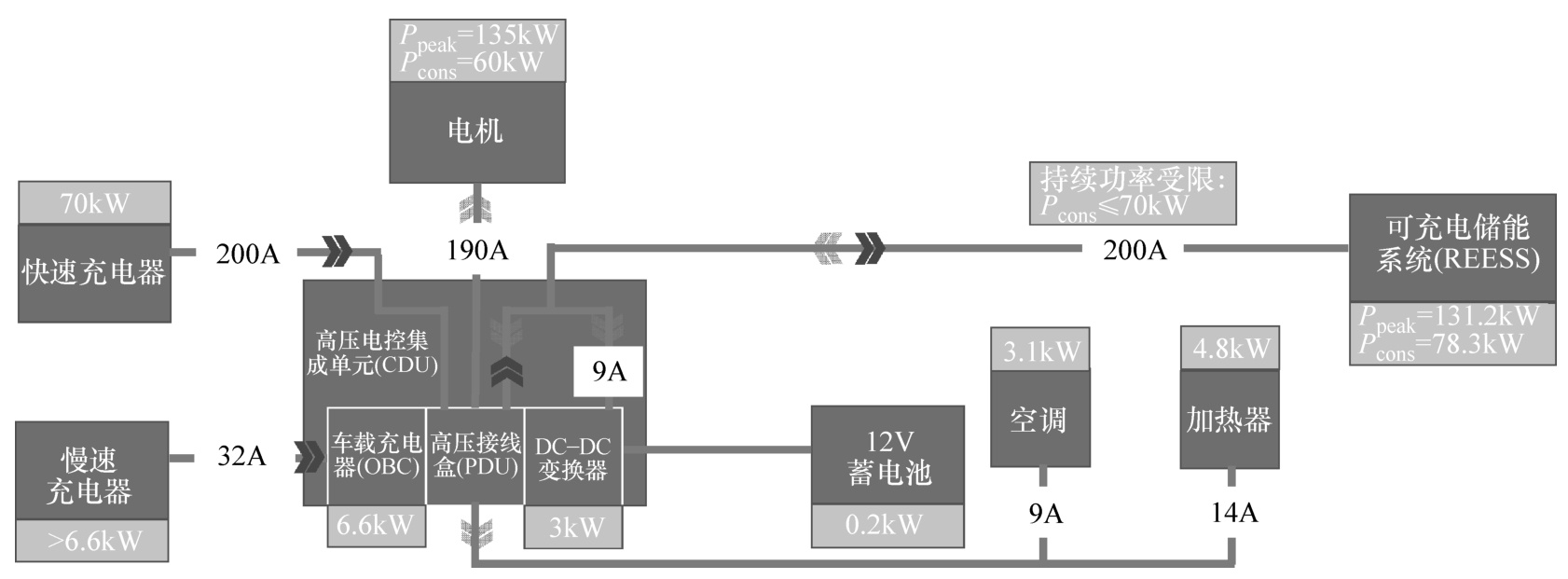
图1-45 某电动汽车的功率平衡图
(3)低压用电器的功率平衡 在设计DC-DC变换器时要考虑所有低压用电器的峰值功率需求,但是对车辆进行动力性和经济性试验时,很多用电器是不工作的,即使是工作的用电器,也运行在额定功率或限制功率状态。表1-17所列为某车型在环境温度(25℃)、转毂试验台上运行时的低压用电器清单。
表1-17 某车型低压用电器功耗清单
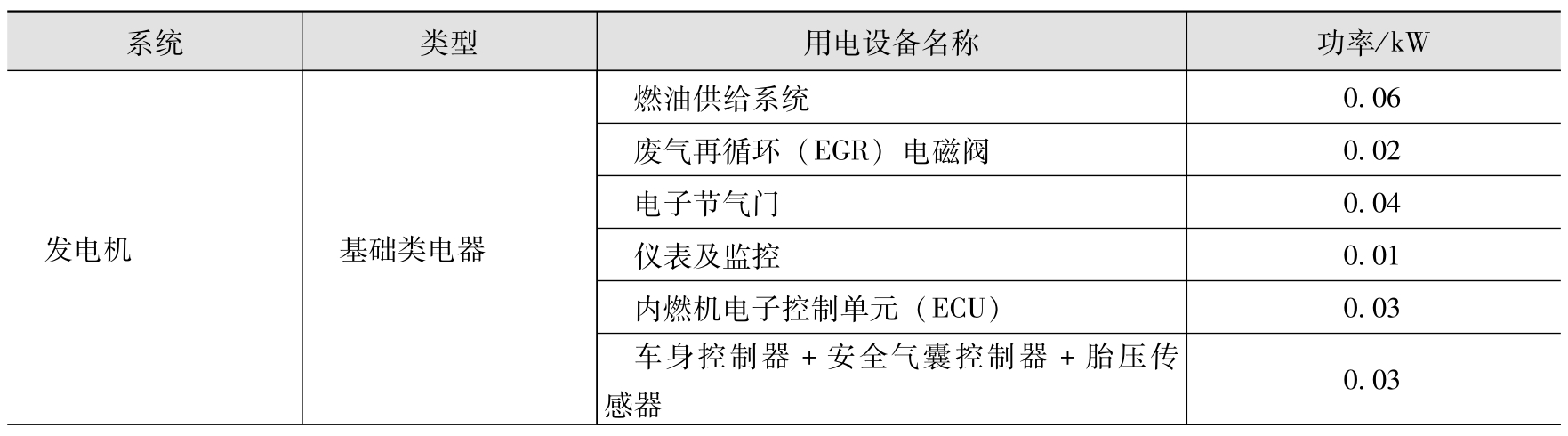
(续)
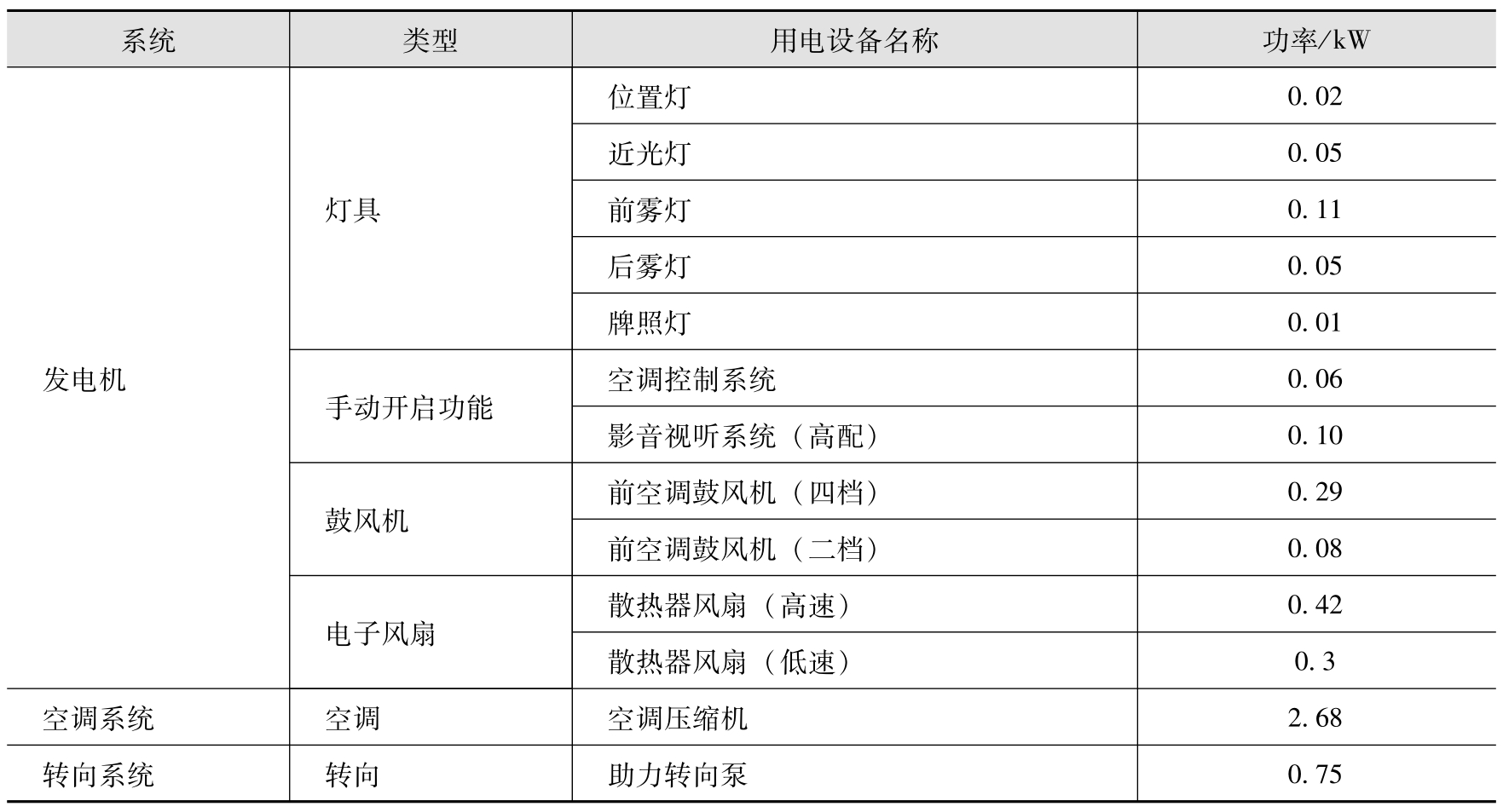
低压用电器的能量来源于12V蓄电池,而12V蓄电池中的能量是通过DC-DC变换器从动力蓄电池中转换得来的。
2.充放电过程中的效率优化
(1)充电方式 纯电动汽车有交流充电和直流充电两种充电方式。连接方式有以下三种:
1)连接方式A。将电动汽车和交流电网连接时,使用和电动汽车永久连接在一起的充电电缆和供电插头,其中电缆组件也是车辆的一部分,如图1-46所示。
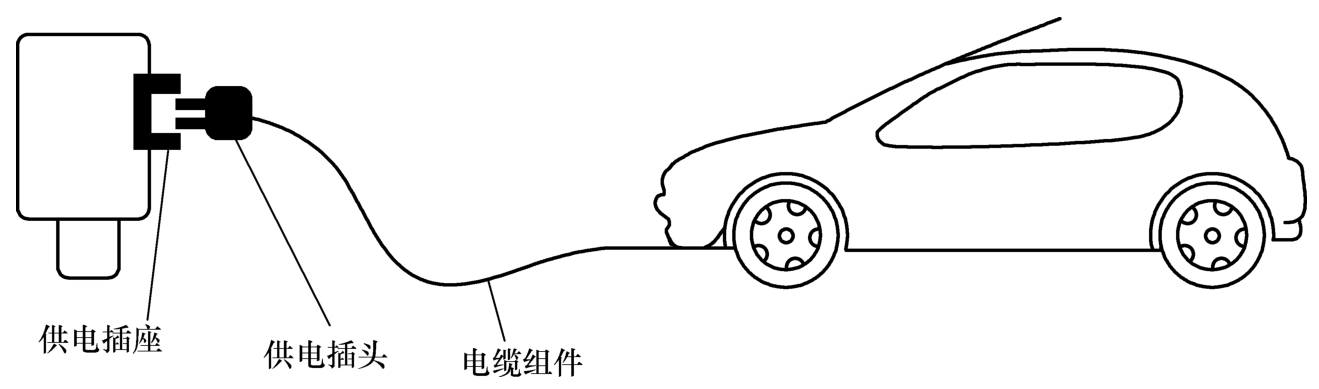
图1-46 连接方式A示意图
2)连接方式B。将电动汽车和交流电网连接时,使用带有车辆插头和供电插头的独立的活动电缆组件,其中可拆卸电缆组件不是车辆或者充电设备的一部分,如图1-47所示。
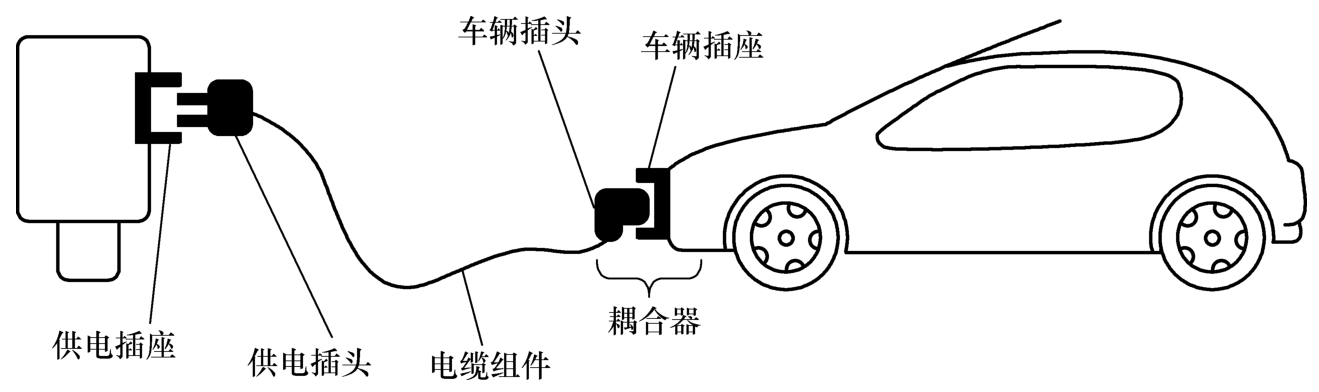
图1-47 连接方式B示意图
3)连接方式C。将电动汽车和交流电网连接时,使用了和供电设备永久连接在一起的充电电缆和车辆插头,其中电缆组件也是车辆的一部分,如图1-48所示。
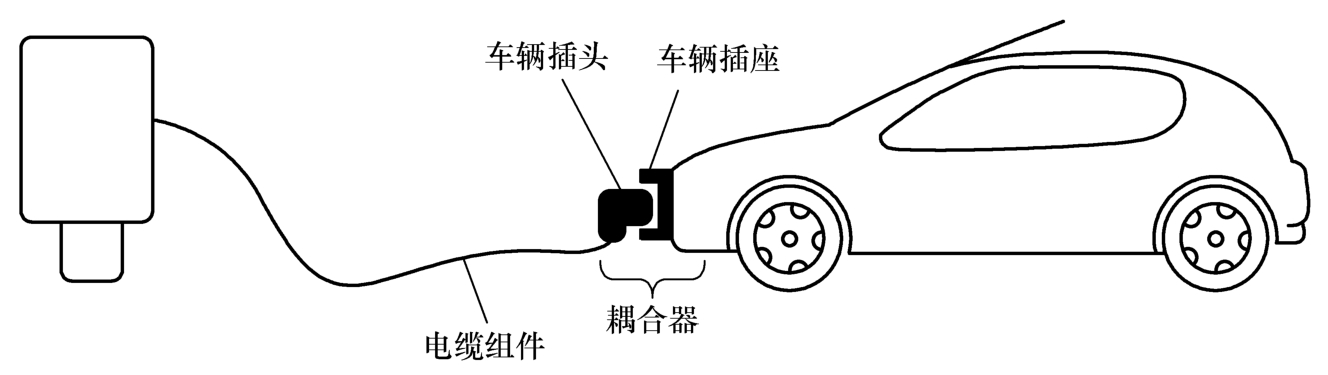
图1-48 连接方式C示意图
国家标准GB/T 18386—2017《电动汽车 能量消耗率和续驶里程 试验方法》,对于EV车型的充电方式有如下要求:采用交流充电方式时电量测量设备应安装于车辆插头和供电设备之间;如果车辆仅有直流充电方式,则电量测量设备应安装于车辆插头和电网之间。
(2)整体充放电过程中的效率研究 交流充电过程中,主要的充放电效率损失来源于车载充电器(OBC)(含充电插头),以及动力蓄电池内部铜排、接插件等的内阻损失。一般交流充电的整体效率在90%左右。图1-49所示为交流充电示意图。
直流充电过程中,主要的充放电效率损失来源于直流充电桩(冷却系统功耗),以及充电接口、动力电池充电母线、内部铜排、接插件等的内阻损失。图1-50所示为直流充电示意图。
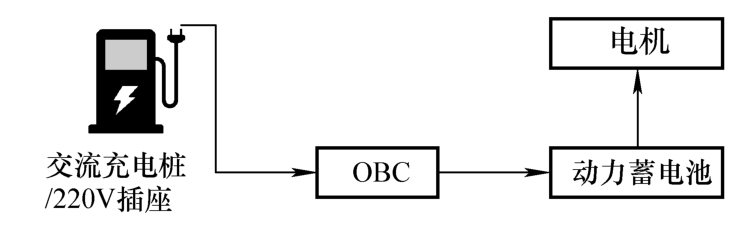
图1-49 交流充电示意图
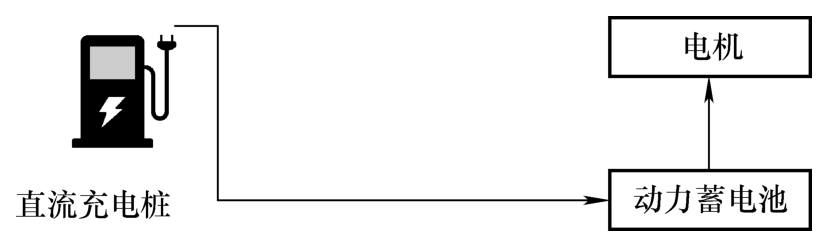
图1-50 直流充电示意图
根据试验统计数据,直流快充方式因电网充电桩的效率损失,整体效率约为85%~95%。表1-18所列为国内某检测机构试验实测的部分车型充放电效率数据。
表1-18 国内某检测机构试验实测的部分车型充放电效率数据
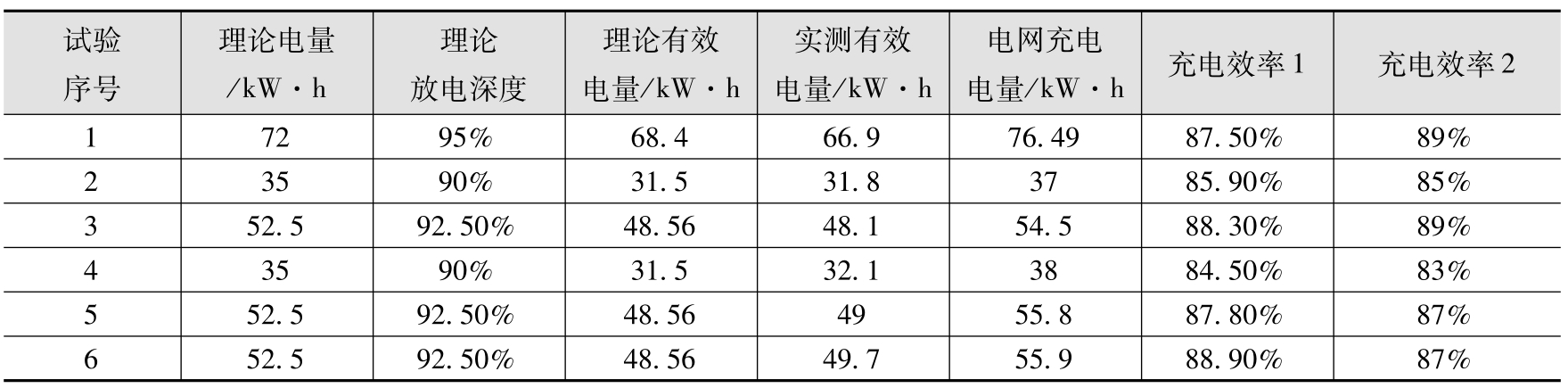
注:充电效率1为实测有效电量与电网充电电量的比值,充电效率2为理论有效电量与电网充电电量的比值。