2.3 机床热误差及形成机理
2.3.1 机床热变形机理
金属材料具有热胀冷缩的热特性,当机床处于工作状态时,由于机床运动部件产生摩擦热、切削热以及外部热源等引起(机床—工件—刀具—夹具)工艺系统变形,这种变形称为热变形。由机床热变形引起的误差称为热变形误差,简称热误差。在精密及超精密加工中,热误差的影响非常严重,占机床总误差的40%~70%。
机床热变形机理如图2-10所示。机床在内外热源的共同作用下产生热量 Q ,该热量通过辐射、对流、传导等方式传递给机床零、部件,引起机床零、部件的温升Δ T ,使相应零、部件产生变形 Δ ,导致机床在加工过程中刀具和工件间产生相对位移 δ ,从而使工件的加工精度下降。
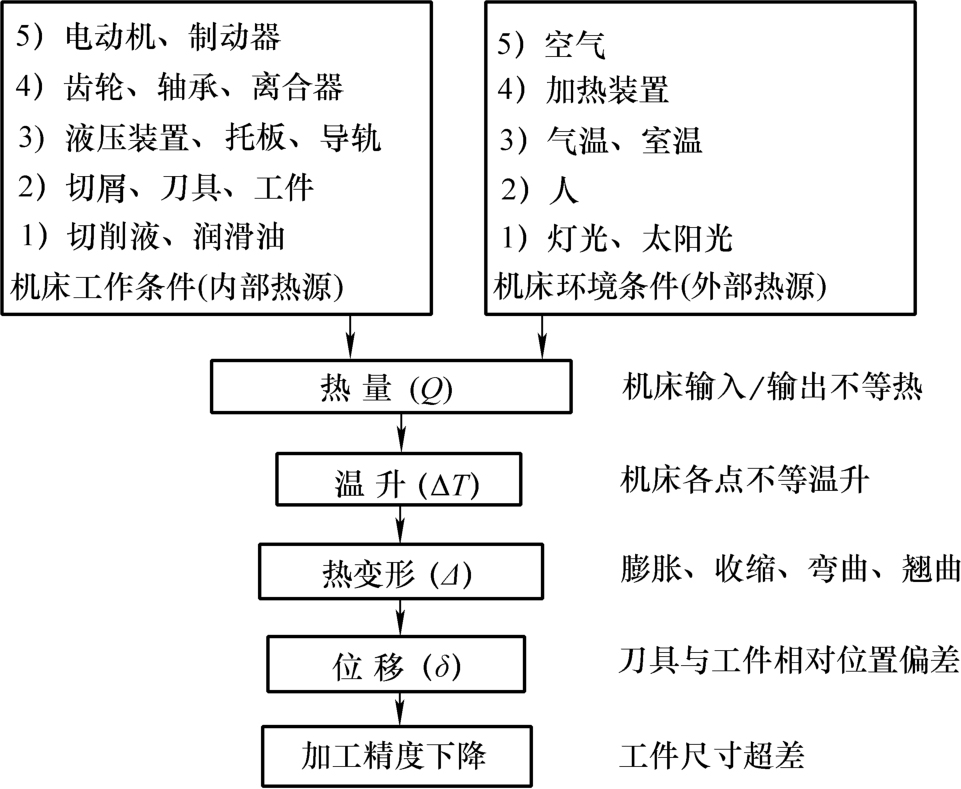
图2-10 机床热变形机理
由上述机床热变形机理不难看出,机床热变形的基本过程是热源→温升(温度场)→热变形。但是,由于机床部件在热变形后会导致摩擦加剧,从而使温升增大。因此,上述过程不是单一方向的,而是相互作用的。
2.3.2 机床热源及温度场
1. 机床热源
机床热源主要可分为两大类:内部热源和外部热源。前者来自切削过程本身,如切削热、运动部件的摩擦热,后者来自切削时的外部条件,如环境温度、阳光、灯光的辐射热等。图2-11为机床热源分布图。
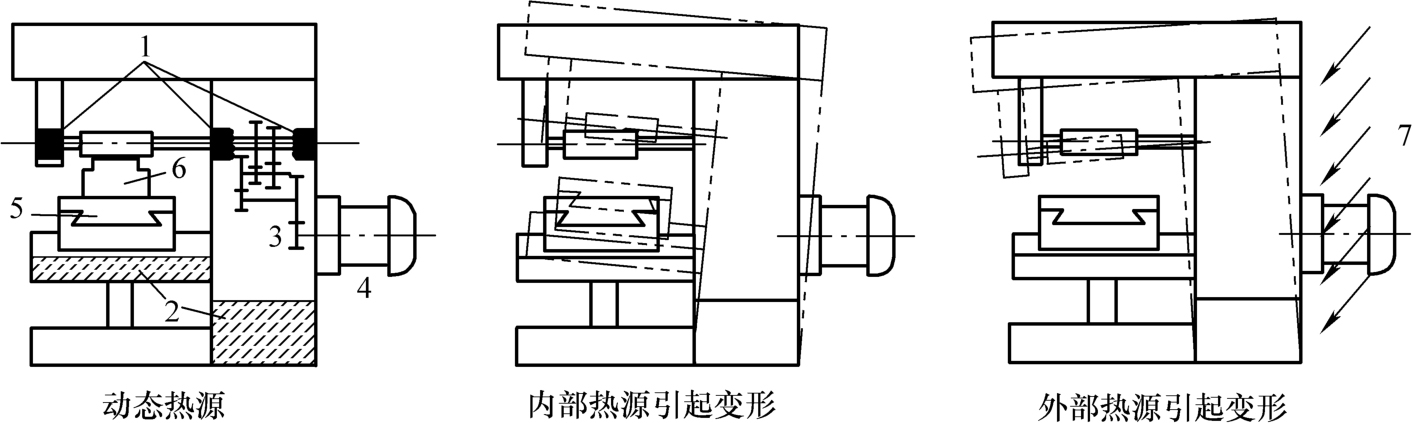
图2-11 机床热源
1—轴承及轴承座 2—齿轮及润滑油 3—传动及制动装置 4—泵及电动机 5—导轨 6—切削运动及摩擦 7—外部热源
(1)切削(或磨削)热 在金属切削过程中,由机械能变为被切削材料的变形能,从而产生大量的热量,产生热量的多少将随被切削材料的性质及切削用量的大小而不同。车削时的发热量 Q 可由式(2-2)确定

式中, F z 为切削过程中切削力的垂直分力(N),与被切材料的性质及切削用量有关; v 为切削速度; τ 为切削时间; Q 为发热量(J)。
切削所产生的热量主要通过传热分配到工件、刀具和切屑,其分配的百分比与切削速度有关。对于不同加工种类,其切削热的计算与分配各不相同。在车削过程中,大量的热为切屑带走(速度越高,百分比越大);传给工件的热量次之,一般在30%以下;而传给刀具的热量又次之,一般不大于5%,高速切削时甚至在1%以下。
对于铣削及刨削加工,传给工件的热量一般在30%以下。对于钻孔和卧式镗孔,因有大量切屑留在孔内,故其传给工件的热量就比车削高,在钻孔加工中(特别是垂直钻孔中)传给工件的热量往往在50%以上。
至于磨削,因其传给磨屑的热量较少,大部分热量是传给工件的。据试验分析,传给工件的热量通常在总热量的84%左右,传给磨屑的热量仅为4%,传给砂轮的热量约占12%左右。有时工件磨削区域的温度可达800~1000℃以上,它将使部分工件表面出现烧伤缺陷并使工件产生较大的热变形,从而影响工件的加工精度。
(2)机床运动副的摩擦热 机床内有各种运动副,如工作台与导轨、摩擦离合器、齿轮传动副、制动器、丝杠与螺母等。它们的运动会产生一定的摩擦力(或摩擦转矩)和摩擦热而形成热源。这些热源使机床部件的温度升高,由于机床各点的温升不同,致使机床产生畸变。
摩擦热的计算一般先计算出运动副摩擦消耗功,然后转化为摩擦热。运动副单位面积消耗的摩擦功率可用式(2-3)计算:

式中, A 为单位面积的功率消耗(W/m 2 ); f 为摩擦系数; p 为压强(N/m 2 ); v 为速度(m/s)。
(3)滚动轴承摩擦热的计算 滚动轴承发热量主要是由轴承的摩擦力矩产生,其计算公式为:

式中, Q b 为轴承发热量; n 为轴承转速(r/min); M 为轴承摩擦力矩(N·mm)。
轴承摩擦力矩是指由轴承滚动摩擦、滑动摩擦和润滑剂摩擦的总和产生的阻滞轴承运转的阻力,可由下式计算:
式中, M 0 为与载荷无关的摩擦力矩; M 1 为与载荷有关的摩擦力矩。

式中, f 0 为与润滑有关的因数,角接触球轴承脂润滑,单列取 f 0 =2; n 为轴承转速(r/min); ν 0 为在轴承工作温度下润滑剂的运动粘度(mm 2 /s); D m 为轴承平均直径(mm)。
式中, f 1 为与轴承类型和载荷有关的因数; P 1 为计算轴承摩擦力矩时的轴承载荷(N)。对于角接触球轴承:
式中, P 0 为当量静载荷(N); C 0 为基本额定定载荷(N)。
式中, X 0 为静径向系数,向心球轴承单列公称角为25°时取 X 0 =0.5; Y 0 为静轴向系数,向心球轴承单列公称角为25°时取 Y 0 =0.5; F r 为径向载荷(N); F z 为轴向载荷(N)。
2. 机床温度场
(1)基本概念
1)机床温度场:是在某一瞬间机床上若干点的温度分布的总称,温度场是时间和空间位置的函数,在直角坐标系内温度场可表示为
2)非稳态温度场。物体上各点的温度不仅是坐标位置的函数而且也是时间的函数,物体上这种温度分布随时间而变化的温度场称为非稳态温度场。
3)稳态温度场。物体上各点温度不随时间变化或变化很小,只是坐标位置的函数,物体上这种温度分布称为稳态温度场。
4)热平衡状态。单位时间内输入物体的热量与向周围介质散发的热量相等,物体上各点温度保持各自的稳定值,物体处于热平衡状态,各点温度不随时间变化或变化很小,只是坐标位置的函数。
5)热平衡时间:达到热平衡所需时间。小型机床一般需要2~4h,中型机床一般需要4~6h,大型机床一般需要10~14h。
(2)机床温度场有限元分析 以数控系统为SINUMERIK 840D的XYTZ型三轴加工中心为例,机床参数为:最高转速为8000r/min,快速进给速度为33m/min, X 、 Y 、 Z 轴行程分别为850mm、560mm、650mm。机床切削参数为: n =2000r/min, f =0.2mm/r。建立机床有限元模型如图2-12所示。
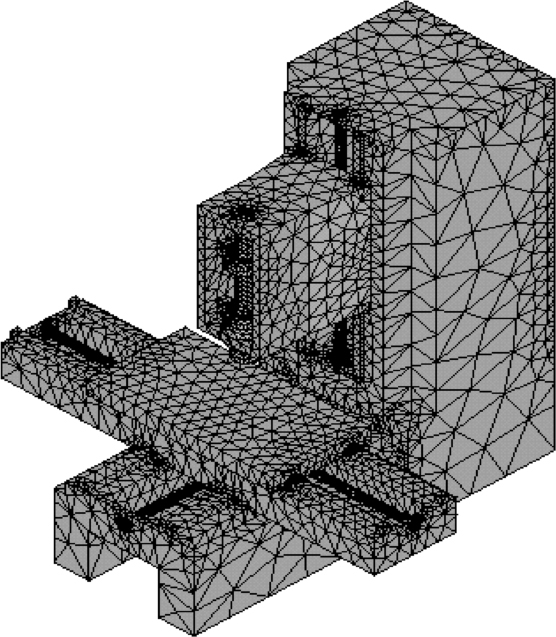
图2-12 机床有限元模型
假定机床初始温度及环境温度为20℃,为模拟一天内机床温度场变化规律,机床首先空运行4h,模拟上午的机床温度变化规律。图2-13为机床温度场云图。由图2-13可以看出,4h内机床主轴温度最高为35℃,温升为15℃;其次是丝杠螺母26℃,温升为6℃;最小是导轨23℃,温升为3℃。
通过机床温度场分析得出:机床在初始运行时温升最大,主轴1000s内温升8℃,随着运行时间的增加,逐渐趋于热平衡,在机床运行8000~14400s内的最大温升为1℃,最小温升仅为0.03℃。
由图2-13可以初步确定温度传感器的布置位置,即机床主轴、丝杠螺母和导轨处。
图2-14为主轴、丝杠螺母及导轨温升曲线图。由图2-14可以看出,主轴和丝杠螺母达到热平衡时间为8000s,而导轨达到热平衡时间较短,为5000s。机床整机热平衡时间为8000s。
为模拟中午休息后继续工作时的机床温度场变化规律,机床停机1h自然冷却,然后继续运行4h,图2-15为停机1h及继续运行4h的机床温度场云图。
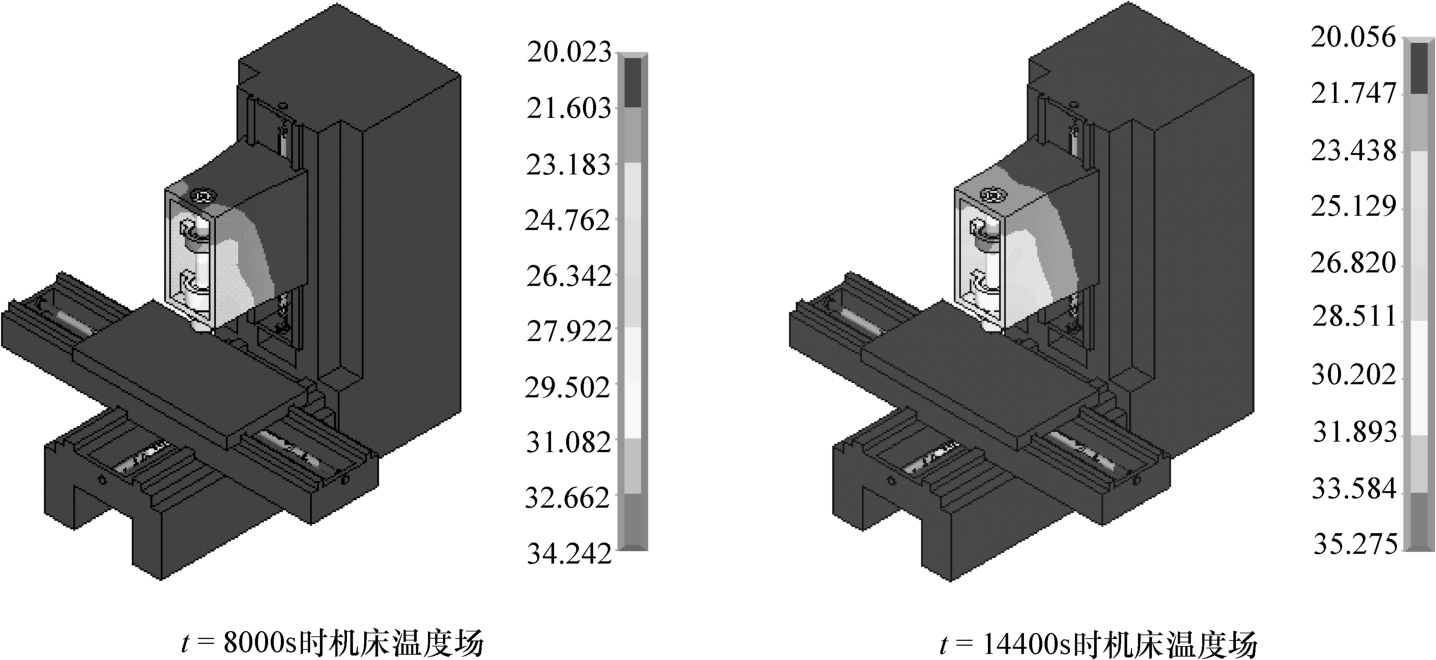
图2-13 机床温度场云图
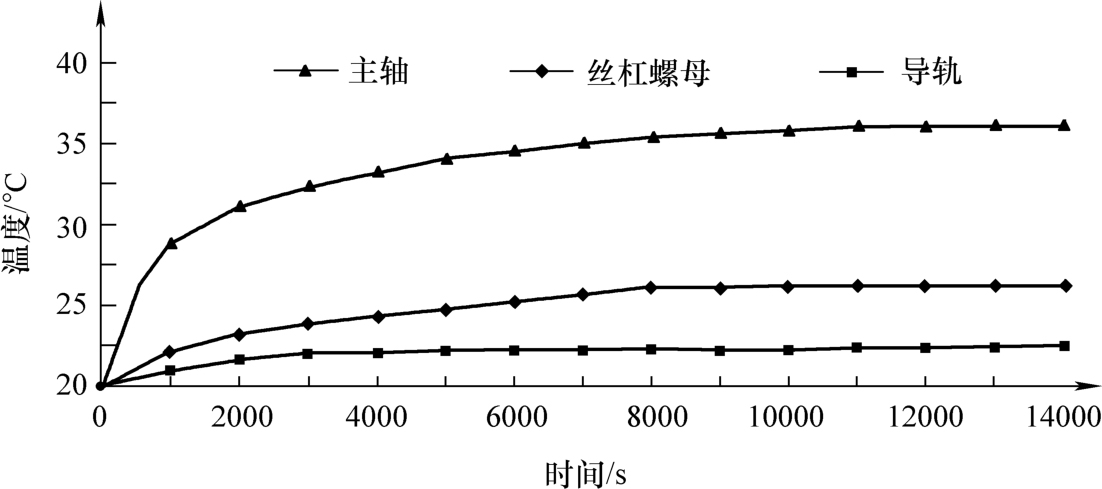
图2-14 主轴、丝杠螺母、导轨温升曲线
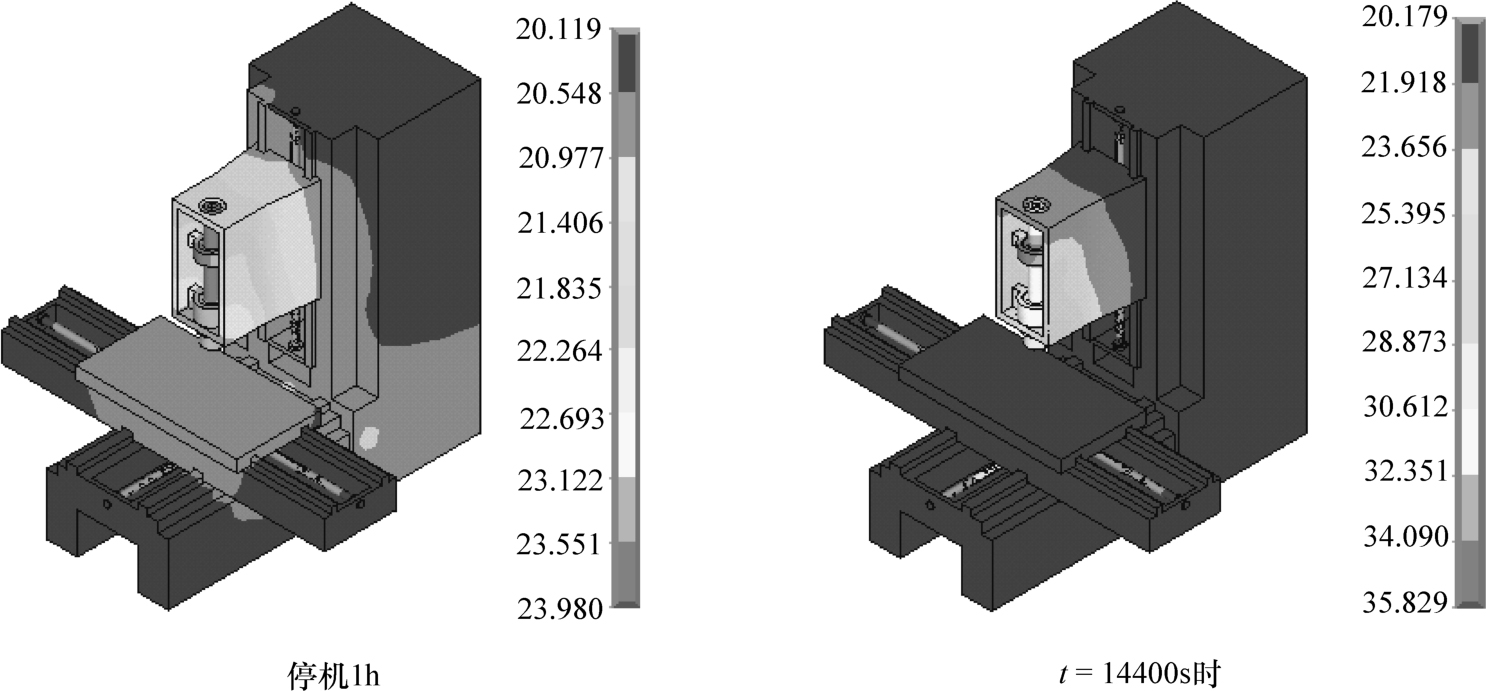
图2-15 停机1h及继续运行4h的机床温度场云图
由图2-15可以看出,停机1h后机床的最高温度降为24℃,在主轴位置,机床整机的温度大幅下降;再次运行后机床温度继续升高,温度场变化规律与初始温升4h的变化规律基本相同。
图2-16为一个工作日内机床主轴、丝杠及导轨的温度变化曲线图。
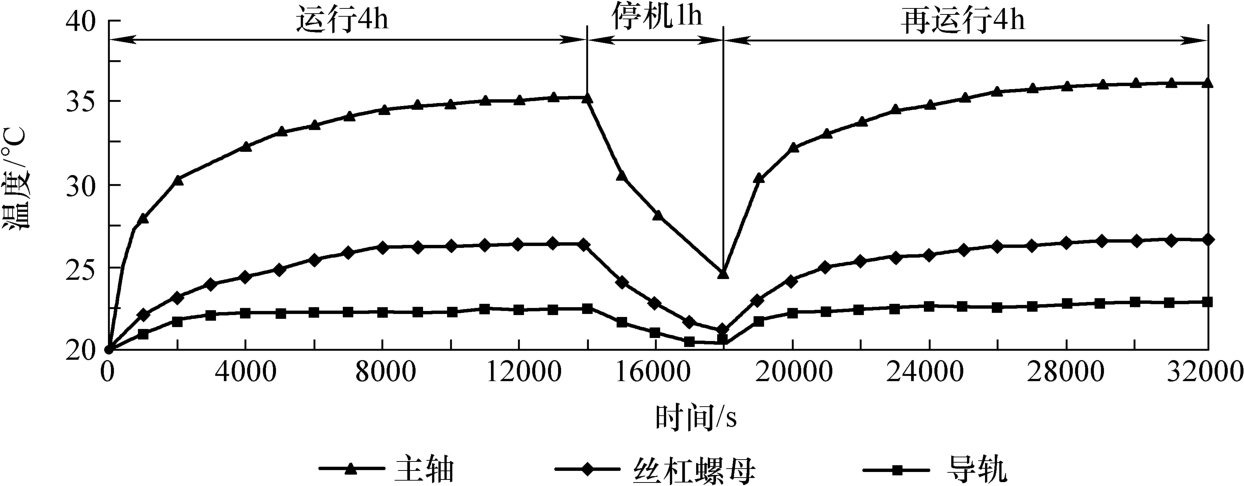
图2-16 一天内主轴、丝杠、导轨温升曲线
由图2-16可以看出,机床一天内的温度变化规律基本一致,即刚启动时机床温升快,随着运行时间的增加,机床逐渐趋于热平衡,这一温度场变化规律为机床热误差建模及测温点的布置提供理论依据。
(3)机床温度场对加工精度的影响
1)机床刚起动时,从冷态开始升温,机床热变形最严重,以后逐渐减少并趋于稳定。在机床起动阶段的热误差也最为严重,使加工精度下降。在精密及超精密加工中经常采用预热机床的方式来使机床达到热平衡或基本热平衡,以避免机床起动阶段热误差对加工精度的影响。为了减少热平衡所需时间,可在预热中高速运转主轴、高速移动工作台或刀架等。
2)停机后机床温度波动,即温度从升高(或不变)变成降低,当机床再次起动时,使加工精度不稳定,该阶段通常发生在换班或休息。为减小该阶段热误差的影响,通常采用不停机的工作方式,即在一天中机床始终处于工作状态,在某些大型工件的加工中,有时甚至连续几天不停机。
3)加工误差与温度变化有关。温度变化大,则加工误差也大。机床温度变化通常与切削用量(主轴转速、进给速度、背吃刀量)、刀具和工件材料等有关。随着切削用量的增加以及被加工材料加工性能的变化,导致机床温升加剧。
2.3.3 机床热变形分析
1. 机床热变形理论计算
(1)无约束条件下的杆件热变形 将一杆件置于一温升为常量的介质中,并且把它的一端固定,则杆的热伸长Δ L 为

式中, α T 为线膨胀系数; L 为杆的原始长度;Δ T 为温升。
对于任意温度场如图2-17所示,杆的伸长量为

式中, T ( x )为温度场函数。
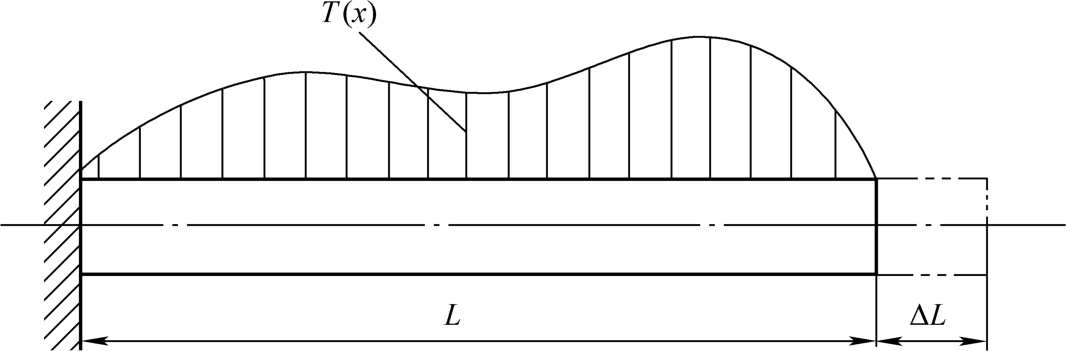
图2-17 任意温度场下杆的热伸长
(2)有约束条件下的杆件热变形 当弹性体受到外在的约束及体内各部分之间的相互约束时,上述变形便不能自由发生而将伴随着变温应力的生成。此时杆件的热变形为两者的和:

式中, σ 为热应力; E 为弹性模量。由于Δ L/L 为杆件的总应变,用 ε 表示,由弹性力学可知, ε =d u/ d x ( u 为沿 x 方向的位移)。由此可得等截面杆一维变温位移的微分方程为

解式(2-8)可得

式中, C 1 = σ/E ,由导热方程可得 T = k 1 x + k 2 。根据边界条件可获得式(2-9)的解。
(3)简单梁的变温挠度 如果温度沿梁的高度不是常数,则梁会在温度应力的作用下产生挠曲。如图2-18所示,有一简单梁,在处于均匀温度时是直的。若其顶面温度变为 T 1 ,底面温度变为 T 2 ,则相应的温变分别为Δ T 1 = T 1 -T 0 ,Δ T 2 = T 2 -T 0 ,梁的顶面与底面的温变差将造成梁的弯曲。
从中取出长度为d x 的单元,该单元的底部与顶部的长度变化分别为 α T Δ T 2 d x 和 α T Δ T 1 d x ,如果Δ T 2 >Δ T 1 ,则单元的两个侧面将彼此相对旋转d ϕ 角度。根据图中所示的几何关系可知:

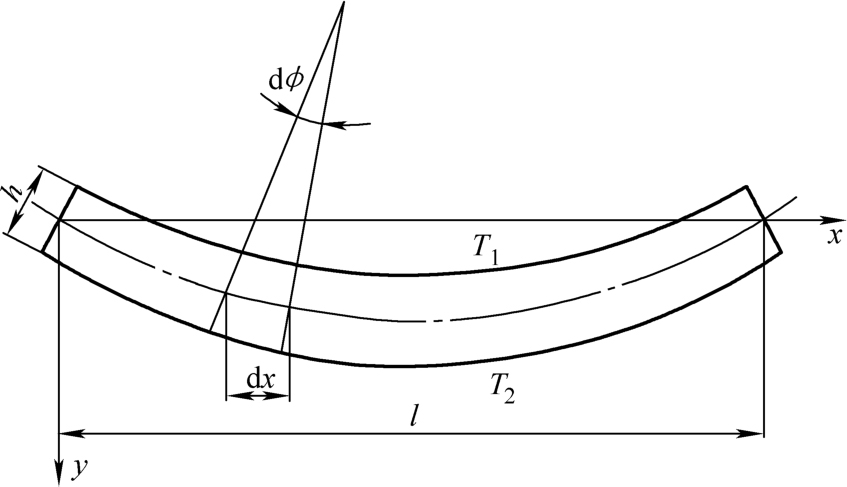
图2-18 简单梁的变温挠曲
若温变差不大,则梁的挠度很小,这时挠曲线是一个很平坦的曲线,有下列关系
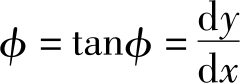
将此式对 x 求导,并代入式(2-10)可得

式中,“-”号与材科力学中的正负号规律相同,梁向上弯曲时取“+”。
根据材料力学的挠曲线方程
可知,梁在全长范围内的
为一定值,根据边界条件,当
x
=0时,
y
=0;当
x
=
l
时,
y
=0。可求得梁的变温挠曲线方程

2. 机床热变形有限元分析
为模拟机床在一天内热变形规律,进行了基于ANSYS的机床热变形分析,机床有限元模型如图2-12所示,在进行机床热变形有限元分析前,首先要引入支撑条件。
(1)引入支撑条件 数控机床通常由4个地脚螺栓固定于基座上,即在每个地脚螺栓上引入了6个约束:3个移动和3个转动。因此,在机床4个底角施加约束,约束自由度为3个移动和3个转动。考虑组成机床的主要材料为钢和铸铁,取钢的弹性模量为210GPa,泊松比为0.3,线膨胀系数为1.1×10 -5 ;取铸铁的弹性模量120GPa,泊松比0.3,线胀系数为1×10 -5 。将2.3.2节计算的不同时间温度场作为载荷施加到加工中心有限元模型即可进行数控机床热变形有限元分析。
(2)基于ANSYS的数控机床热变形分析 同2.3.2节,模拟一天内机床热变形规律,首先将2.3.2节中机床初始运行4h内的温度场数据作为载荷施加到机床有限元模型,模拟机床在上午工作时的热变形规律。图2-19为机床热变形云图。
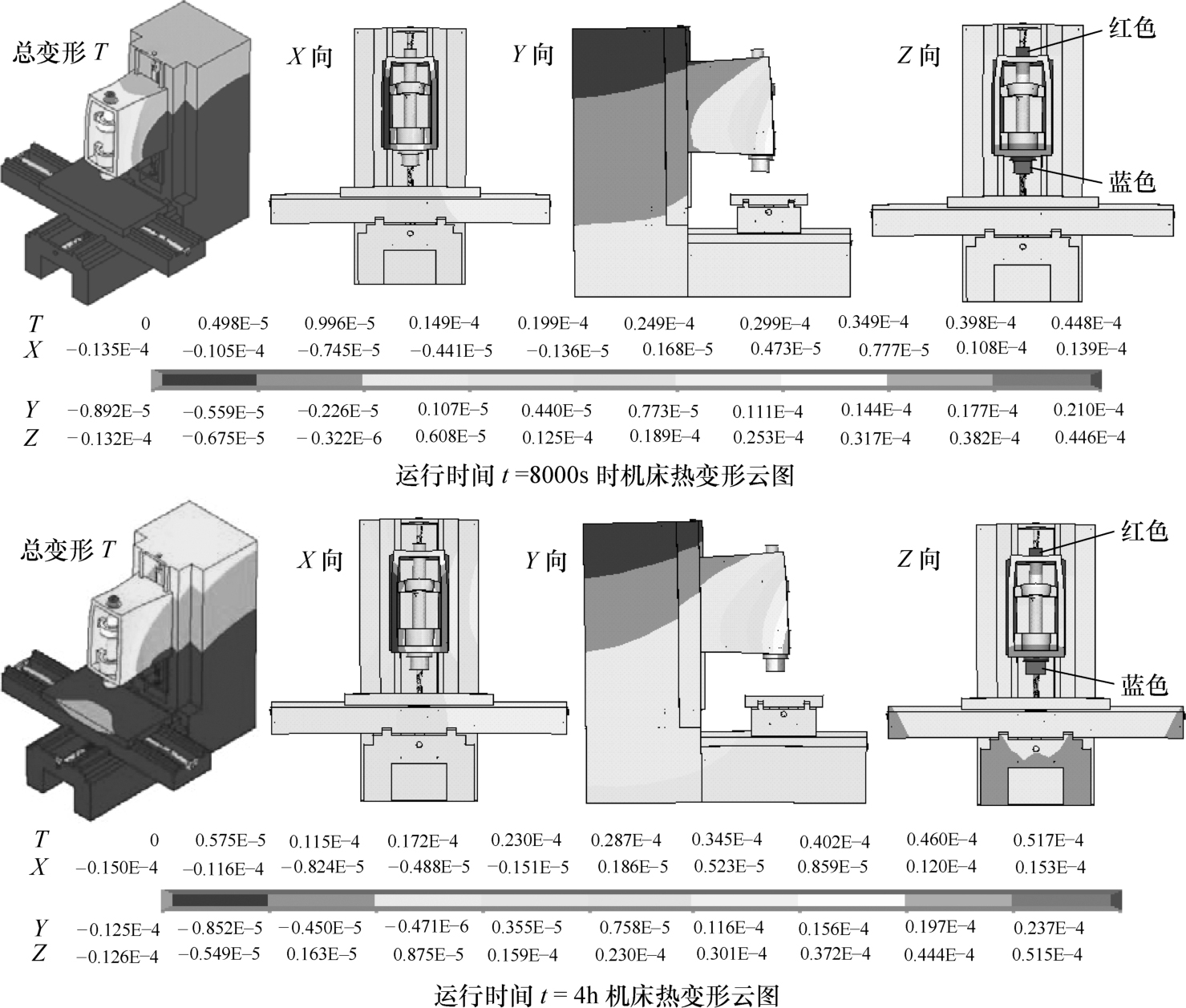
图2-19 机床热变形云图
由图2-19可以看出,机床运行4h后的整机热变形趋势为床身呈中凸弯曲,最大变形量在床身中部;立柱向后倾斜,最大变形量在立柱的上端;主轴膨胀并弯曲,最大变形量在主轴顶端。
从图2-19还可以看出,机床8000s的热变形云图与机床14400s的热变形云图基本相同,在8000~14400s内,机床 X 向热变形增加1.4μm, Y 向热变形增加2.7μm, Z 向主轴前端热变形基本保持不变(图中 Z 向变形主轴前端蓝色区域),虽然主轴顶端热变形增加6.9μm(图中 Z 向变形主轴顶端红色区域),但是主轴顶端对机床精度不产生影响,因此,可以确定机床整机热变形达到平衡的时间为8000s。
为模拟中午休息1h的机床热变形规律,将2.3.2节的停机1h温度场作为载荷施加到机床有限元模型,图2-20为停机1h后的机床热变形云图。
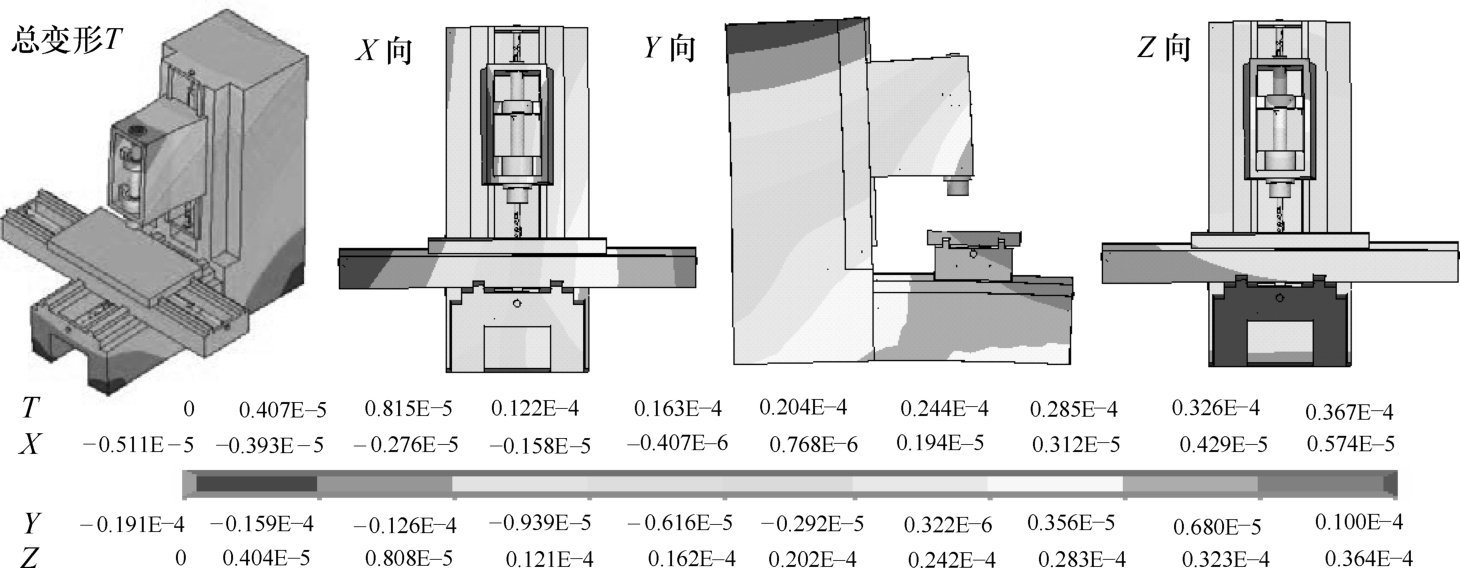
图2-20 停机1h后机床热变形云图
由机床热变形的有限元分析得出:机床停机1h的温度虽然大幅下降,但是机床热变形却表现出先增加后减小的特性,说明机床热变形具有滞后性。
为分析机床继续运行的热变形规律,将2.3.2节继续运行的机床温度场数据作为载荷施加到机床有限元模型,图2-21为继续运行4h的热变形云图。由图2-21可以看出,机床继续运行5000s和14400s的热变形云图基本相同,在9400s内,机床 X 、 Y 、 Z 向热变形分别增加1.8μm、4.3μm、1.3μm,可以确定机床继续运行后整机热变形达到平衡的时间为5000s,对比机床初始运行时到达热变形平衡的时间8000s,机床再次运行后热变形达到平衡的时间明显减小,这主要是因为停机1h后,机床还存在残余热变形。由以上分析可知,机床停机后继续运行时必须重新建立数学模型。
图2-22为一个工作日内机床温度及各轴最大热变形曲线。由图2-22可以看出,机床一天内的热变形随着温度的增加而增大,并且热变形与温度成比例关系,但是停机后机床热变形有一明显阶越,也就是说机床热变形具有滞后性。
图2-22还表明,虽然停机前后的机床温度场及热变形变化规律相同,但是由于停机后残余热变形的影响,停机前后同一温度下对应的热变形却各不相同,因此必须建立停机前后的机床热误差模型。
3. 机床热变形形态及对策
(1)机床热变形形态 由于机床本身结构形状及机床零部件间的约束条件不同,机床热变形的状态也各不相同。总的来说,机床热变形状态包括倾斜、弯曲、翘曲、扭曲和畸变等变形状态。图2-23为机床热变形状态图。
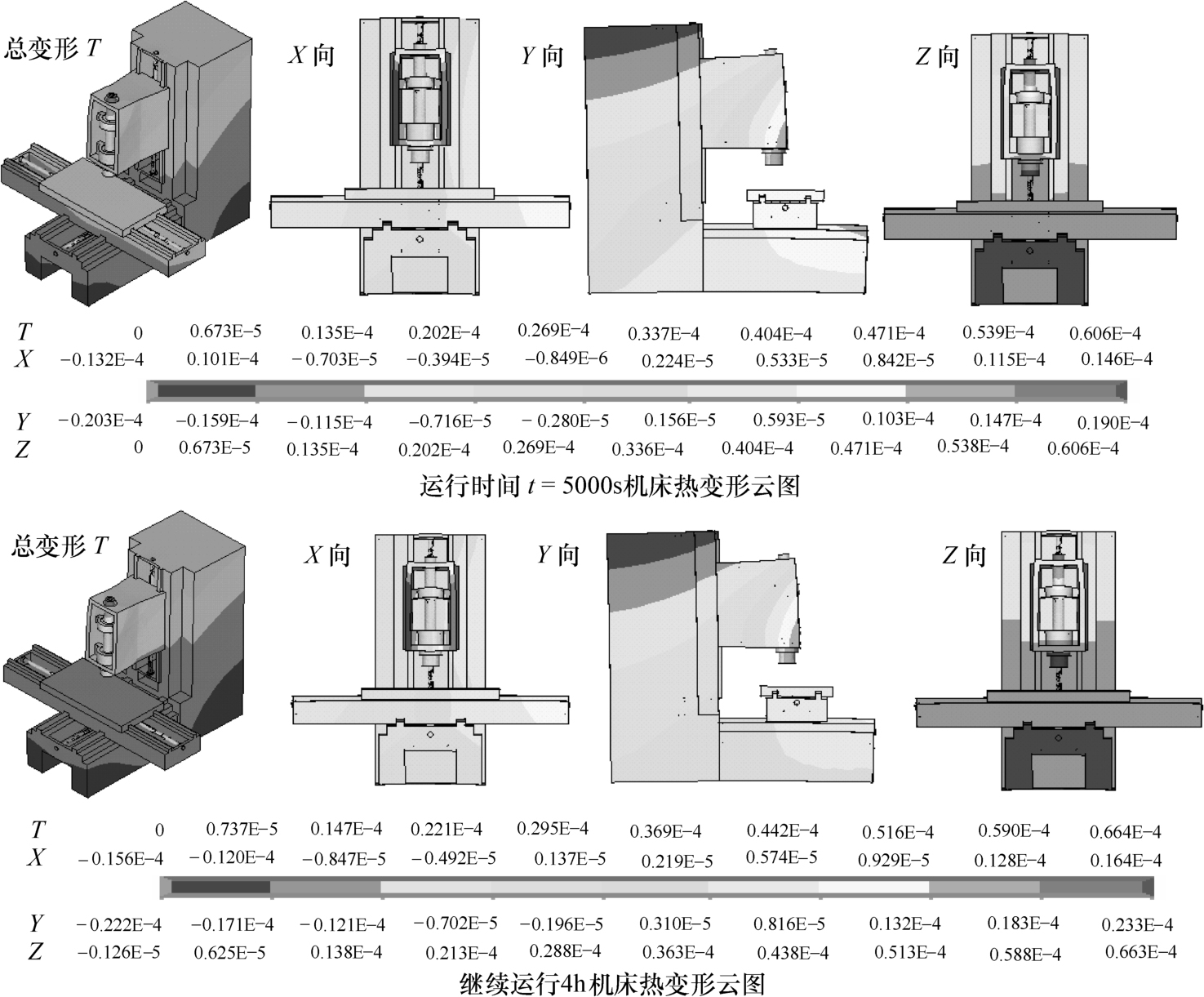
图2-21 继续运行4h后机床热变形云图
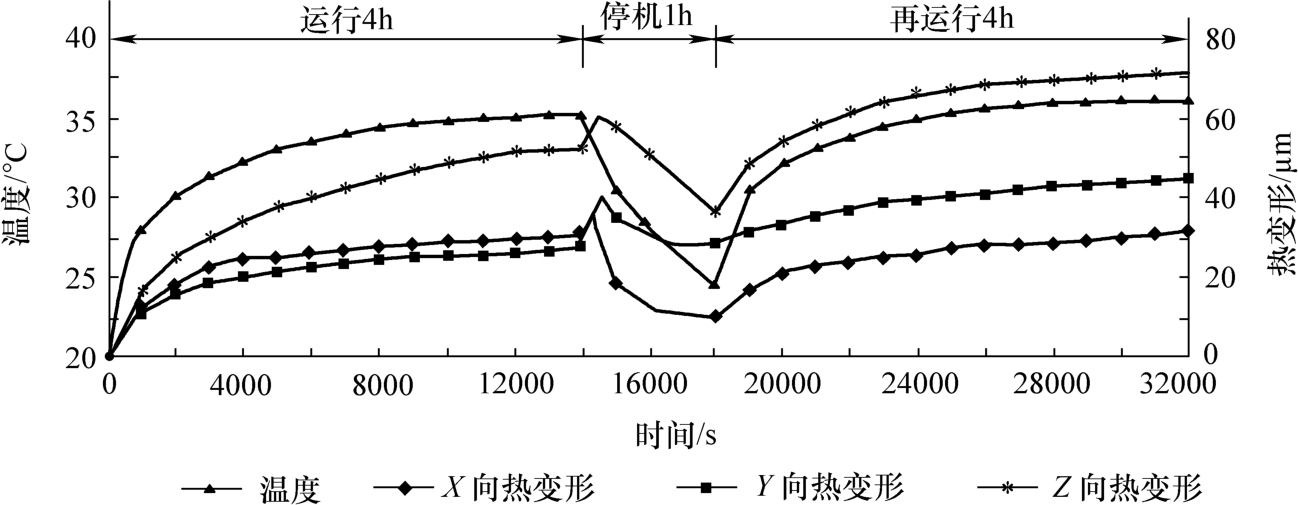
图2-22 一天内机床温度及热变形曲线
1)普通车床:主轴箱温度高,右边温度高于左边,主轴轴线被抬高并右高左低倾斜;床身温度上高下低,故弯曲而中凸。
2)升降台铣床:主轴及机床中部温度高,故主轴被抬高并倾斜,立柱外翻;工作台温度上高下低,故弯曲而中凸。
3)卧式磨床:主轴箱右侧温度高,故主轴向内倾斜。
4)立式磨床:立柱左侧温高,主轴被抬高并倾斜,立柱外翻。
5)龙门刨或龙门铣:主轴右侧及床身上部温度高,故立柱向外倾斜,床身向上弯曲。
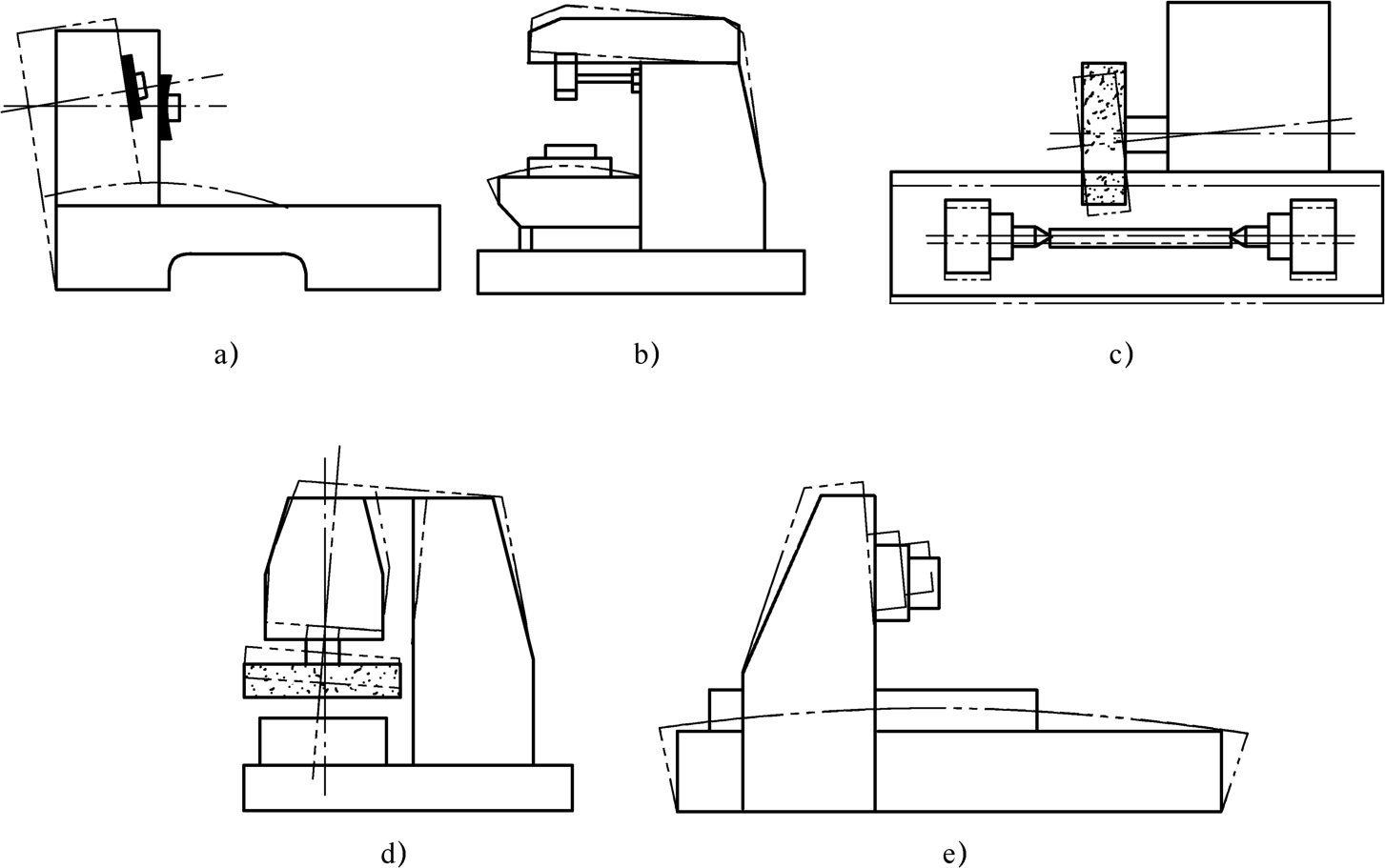
图2-23 机床热变形状态
a)普通车床 b)升降台铣床 c)卧式磨床 d)立式磨床 e)龙门刨或龙门铣
(2)控制机床热变形的对策
1)优化机床设计,减小热变形。利用“热对称面”概念,设计热对称结构或使热源对称分布。热对称结构对热源来说是对称的,在热变形后,其中心对称线的位置基本不改变,使之减少对加工精度的影响。此外,还可以改进机床结构,使热变形发生在不影响加工精度的方向,或把热源从机床本体中分漓出去或减少其发热量。从机床的热刚度着手进行机床热态特性优化设计,进一步可综合考虑静刚度、动刚度、热刚度的总体优化设计。
2)强制冷却,控制机床温升。对内热源强制冷却,是近来采用较多的措施之一,如风冷、水冷、油冷、冷冻机制冷以及采用热管技术,迅速地将大量的热量散开,以减少或消除船源的影响。目前,加工中心机床普遍采用冷冻机对润滑液进行强制冷却,以控制主轴轴承和其他工作部件温升。热管技术是近年来国内外将热源的热量迅速传递与散发达到均衡温度场作用的新技术。热管一般由工作液体、毛细多孔材料、管壳三部分组成,即一根抽成真空的金属封闭管壳(如黄铜管),其管内壁衬有毛细多孔材料,并浸在工作液体(如水、丙酮等)中。热管工作时,将管的一端置于热源处,另一端置于冷却处。在热源处的毛细多孔材料中的工作液体受热(起吸热降温作用)汽化,压力增大,使其形成压力差,工质蒸汽沿管流向冷却端,蒸汽在此处放热而凝结成工作液体,在毛细多孔材料吸力作用下,返回热端,形成工作液体由热端带热量至冷端的循环,致使热源处温升降低。
3)设置辅助热源。利用人工热源,促使机床缩短温升平衡过程、减少加工中温度场变化,以达到稳定热态加工精度的目的。
4)应用补偿技术。在生产中测出大批量工件尺寸,然后对下次加工用量进行补偿。随着数控机床的发展,产生了热位移数控补偿技术:分析机床零、部件,特别是工件与刀具的相对热位移规律,建立热位移数学模型,实行开环或闭环补偿。随着光电技术的发展,各种传感器被应用于机床温度及位移的测量,通过测量结果进行实时动态建模补偿。
5)控制环境温度。工艺系统热变形不仅受到内部热源的影响,也受到外部热源的影响。环境温度对大型机床床身导轨、工作台精度的影响最为敏感,有时随室温上升呈中凸,有时随室温下降呈中凹。为了保证精密加工与装配不受环境温度变化的影响,通常建立恒温车间(甚至恒温工厂),实行季节性调温,或进行喷油冷却控制机床局部环境温度,使机床外部温度变化的影响减到最小。
4. 机床热误差元素
(1)移动副热误差元素 机床热变形最终反映在机床运动部件上,机床运动部件由于机床热变形的影响,其运动轨迹偏离理想运动轨迹而产生热误差。当工作台沿
X
方向移动时,存在6个热误差元素,分别为3个移动误差:
X
向线性位移热误差
、
Y
向直线度热误差
和
Z
向直线度热误差
;3个转动误差:绕
X
轴的倾斜热误差
、绕
Z
轴的偏摆热误差
和绕
Y
轴的俯仰热误差
。
同理,工作台沿
Y
方向移动时,存在3个移动误差:
Y
向线性位移热误差
、
X
向直线度热误差
和
Z
向直线度热误差
;3个转动误差:绕
Y
轴的倾斜热误差
、绕
Z
轴的偏摆热误差
和绕
X
轴的俯仰热误差
。
同理,工作台沿
Z
方向移动时,存在3个移动误差:
Z
向线性位移热误差
、
Y
向直线度热误差
和
X
向直线度热误差
;3个转动热误差:绕
Z
轴的倾斜热误差
、绕
X
轴的偏摆热误差
和绕
Y
轴的俯仰热误差
。
由于机床3个坐标轴
X
、
Y
、
Z
相互垂直,故还存在3个垂直度热误差:
、
、
。
(2)转动副热误差元素 机床转动副绕转轴转动时存在6个热误差元素,包括3个移动热误差和3个转角热误差。当
A
轴绕转轴
X
转动时,由于机床热变形的影响,产生6个热误差元素,3个移动误差:
X
向线性位移热误差
、
Y
向直线度热误差
和
Z
向直线度热误差
;3个转角误差:绕
X
轴的转角热误差
、绕
Z
轴的转角热误差
和绕
Y
轴的转角热误差
。
同理,
B
轴绕转轴
Y
转动,存在3个移动误差:
X
向直线度热误差
、
Y
向线性位移热误差
和
Z
向直线度热误差
;3个转角误差:绕
X
轴的转角热误差
、绕
Z
轴的转角热误差
和绕
Y
轴的转角热误差
。
同理,
C
轴绕转轴
Z
转动,存在3个移动误差:
X
向直线度热误差
、
Y
向直线度热误差
和
Z
向线性位移热误差
;3个转角误差:绕
X
轴的转角热误差
、绕
Z
轴的转角热误差
和绕
Y
轴的转角热误差
。
由于
A
、
B
、
C
轴分别平行于
YOZ
平面、
XOZ
平面和
XOY
平面,故还存在6个平行度热误差元素,
、
、
、
、
和
。
(3)主轴热漂移误差元素 主轴旋转时存在5个热漂移误差元素,包括3个移动热误差和2个转角热误差,3个移动误差:
X
向直线度热误差
、
Y
向直线度热误差
和
Z
向线性位移热误差
;2个转角误差:绕
X
轴的转角热误差
和绕
Y
轴的转角热误差
。